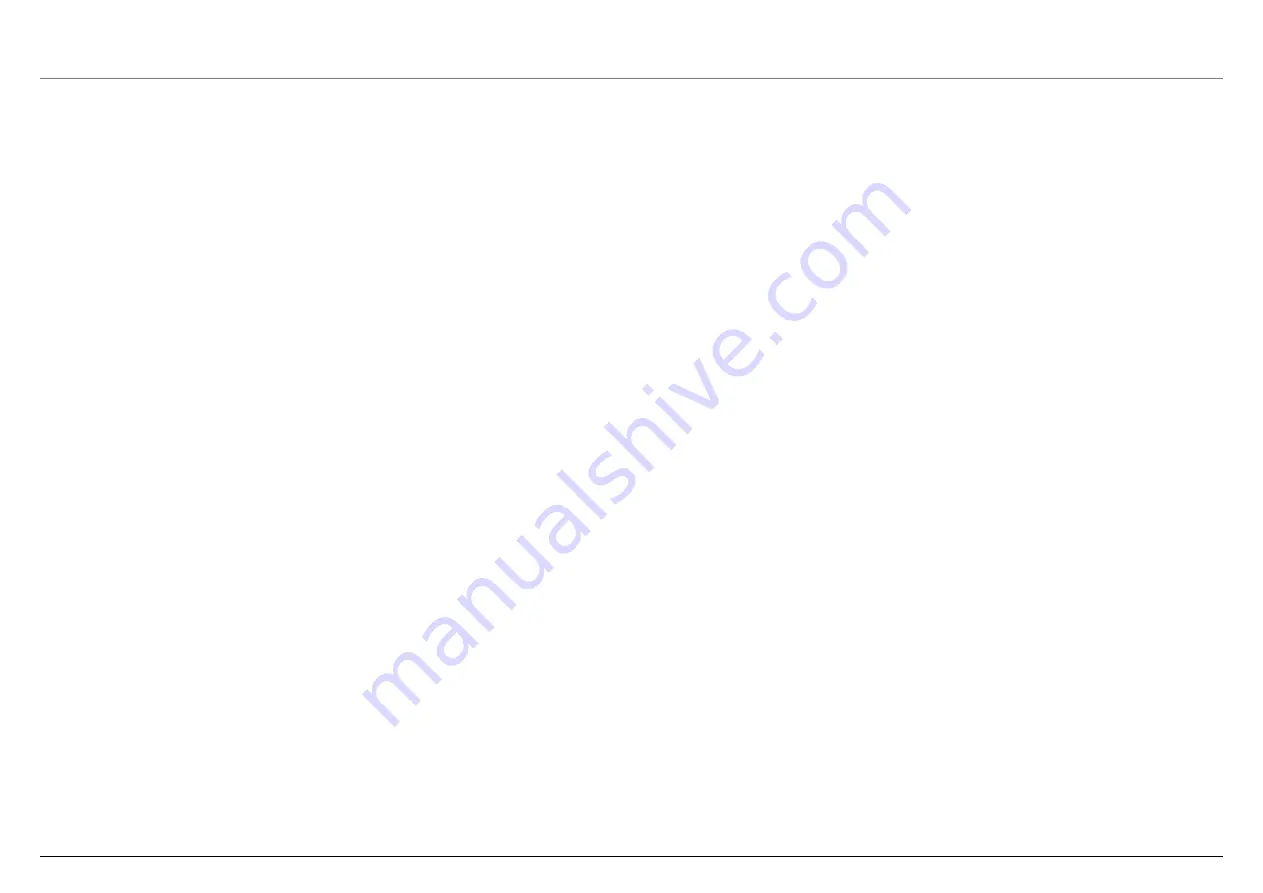
W
W
W
F
F
F
V
V
V
C
C
C
V
V
V
I
I
I
S
S
S
I
I
I
O
O
O
N
N
N
1
1
1
6
6
6
W
W
W
A
A
A
S
S
S
H
H
H
E
E
E
R
R
R
R
R
R
E
E
E
P
P
P
A
A
A
I
I
I
R
R
R
I
I
I
N
N
N
S
S
S
T
T
T
R
R
R
U
U
U
C
C
C
T
T
T
I
I
I
O
O
O
N
N
N
SAFETY ........................................................ 2
INSTALLATION ............................................ 3
Basic installation ................................................................ 3
Feet (leveling legs).............................................................. 3
(aqua secure)................................................ 3
Water connections.............................................................. 4
Transport (shipping bolts) ................................................. 4
Drain hoses ......................................................................... 5
Installation hints ................................................................. 5
OPERATION ................................................. 6
Controls ............................................................................... 6
Child lock............................................................................. 6
Display symbols.................................................................. 7
Spin speeds......................................................................... 7
Changing signal volume..................................................... 8
COMPONENTS............................................. 9
Comparison to WFMC Nexxt washers............................... 9
WFVC washer components................................................ 9
Operation ........................................................................... 21
REPAIR....................................................... 23
Disassembly / Reassembly .............................................. 23
Diagnosing (troubleshooting).......................................... 33
Washer vibration............................................................... 35
Motor control troubleshooting ........................................ 35
Customer diagnosing (from Operating Instructions) .... 36
Customer fault displays (from Operating Instructions) 38
Customer maintenance .................................................... 38
FAULT DIAGNOSTICS ...............................40
Test program / fault (error) codes ................................... 40
TECHNICAL SPECIFICATIONS.................42
Washer ratings.................................................................. 42
702_58300000143607_ara_en_a
Page 1 of 42