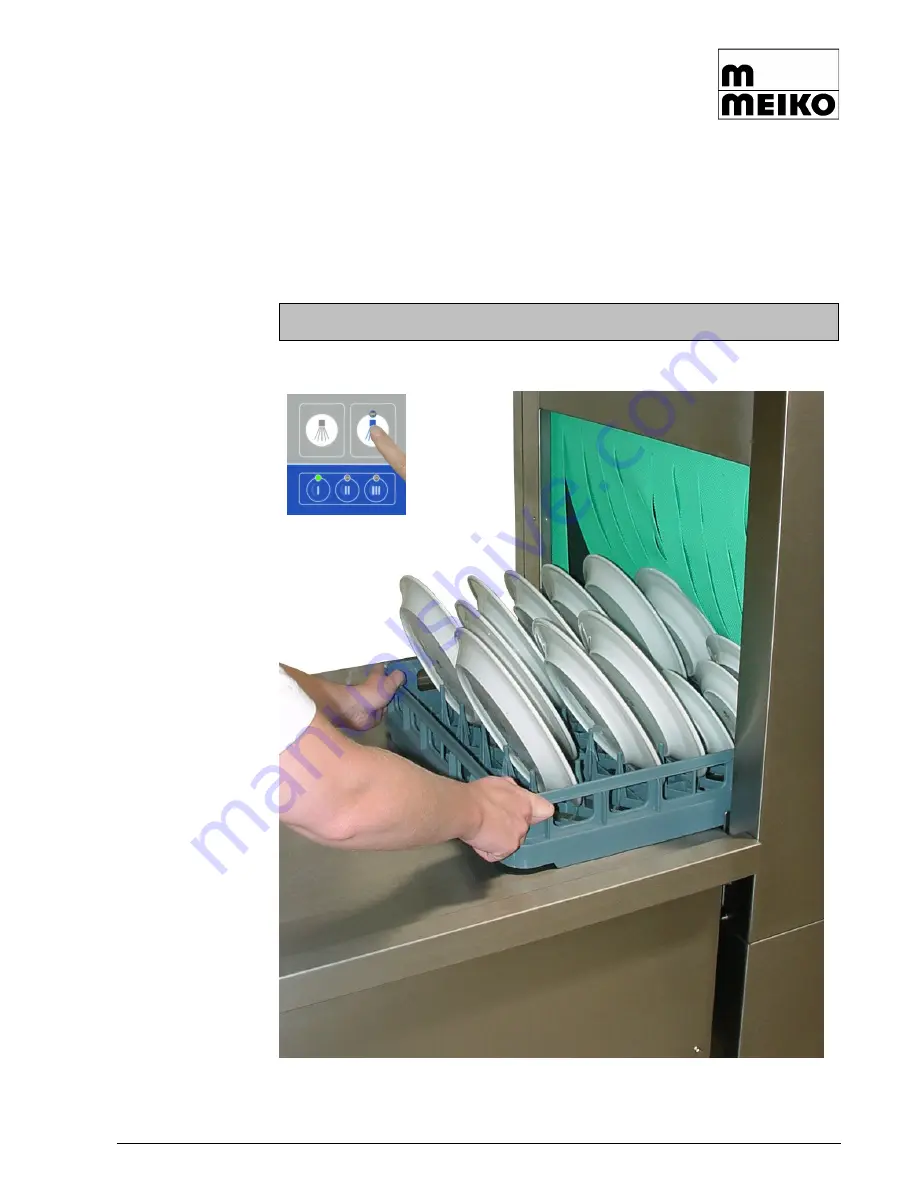
Datei:BA-K-tronic_MIKE_9626212_EN_2005-12-01.doc
Update: 2017-01-05
9626212
1/44
W e reserv e the right to change execution and construction !
MEIKO Maschinenbau GmbH & Co. KG, Englerstraße 3, D-77652 Offenburg, Tel.: +49/781/203-0, Fax: +49/781/203-1121
Operating Instructions
MEIKO - Dishwashing machine
model K-Tronic
TRANSLATION OF THE "ORIGINAL OPERATING INSTRUCTIONS"
The original operating instructions can be downloaded from: https://partnernet.meiko.de
Summary of Contents for K-Tronic
Page 44: ......