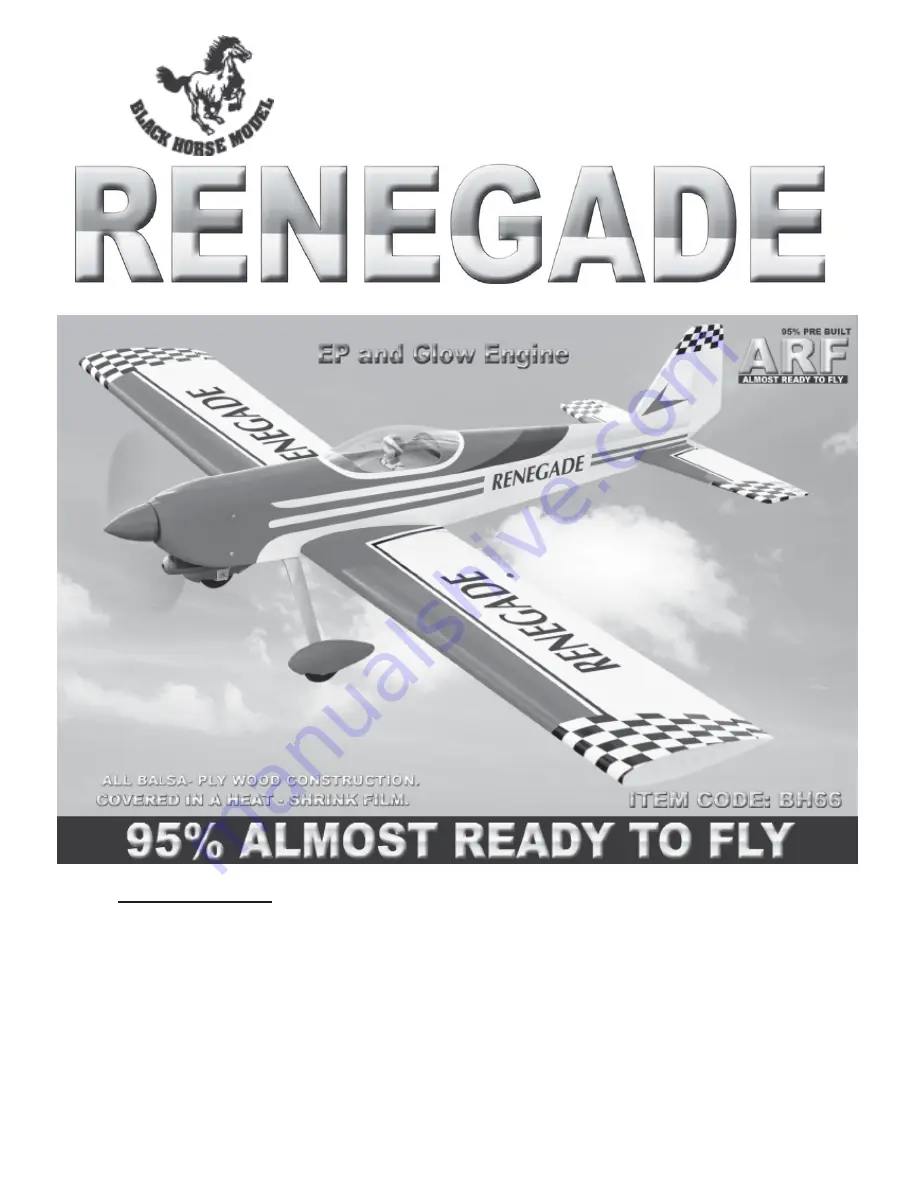
Instruction Manual book
SPECIFICATION
Made in Vietnam.
Wingspan : 1,580mm. 62.20 in.
Length : 1,255 mm. 49.41in.
Weight : 2.5kg. 5.50lbs.
Parts Listing required (not included).
Radio : 4 channels.
Servo : 4-5 servos.
Glow Engine : 46-55 cu.in. 2 stroke.
Propeller : 12 x 6.
Speed Control: 60A.
Electric Motor: BL 2826/06 OUTRUNER.
Battery: 4Cells-Li-Poly-14.8- 5.000 mAh.