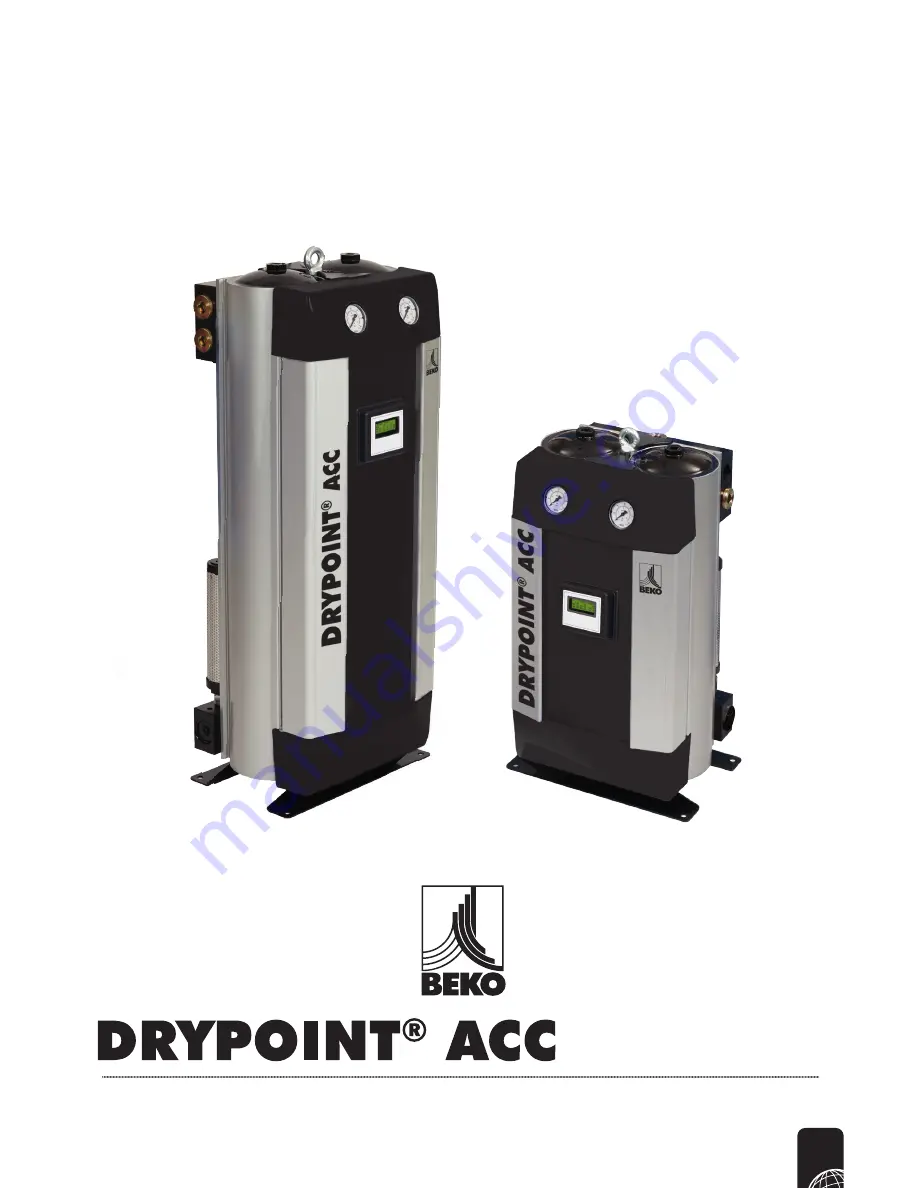
EN
Instruction & Technical Manual
46 - 110
BEKO TECHNOLOGIES CORP. 900 Great SW Parkway, Atlanta, Georgia 30336,
USA
+1 (800) 235-6797 Phone +1 (404) 629-6666 Fax [email protected] www.bekousa.com
EN
Instruction & Technical Manual
46 - 110
BEKO TECHNOLOGIES CORP. 900 Great SW Parkway, Atlanta, Georgia 30336,
USA
+1 (800) 235-6797 Phone +1 (404) 629-6666 Fax [email protected] www.bekousa.com