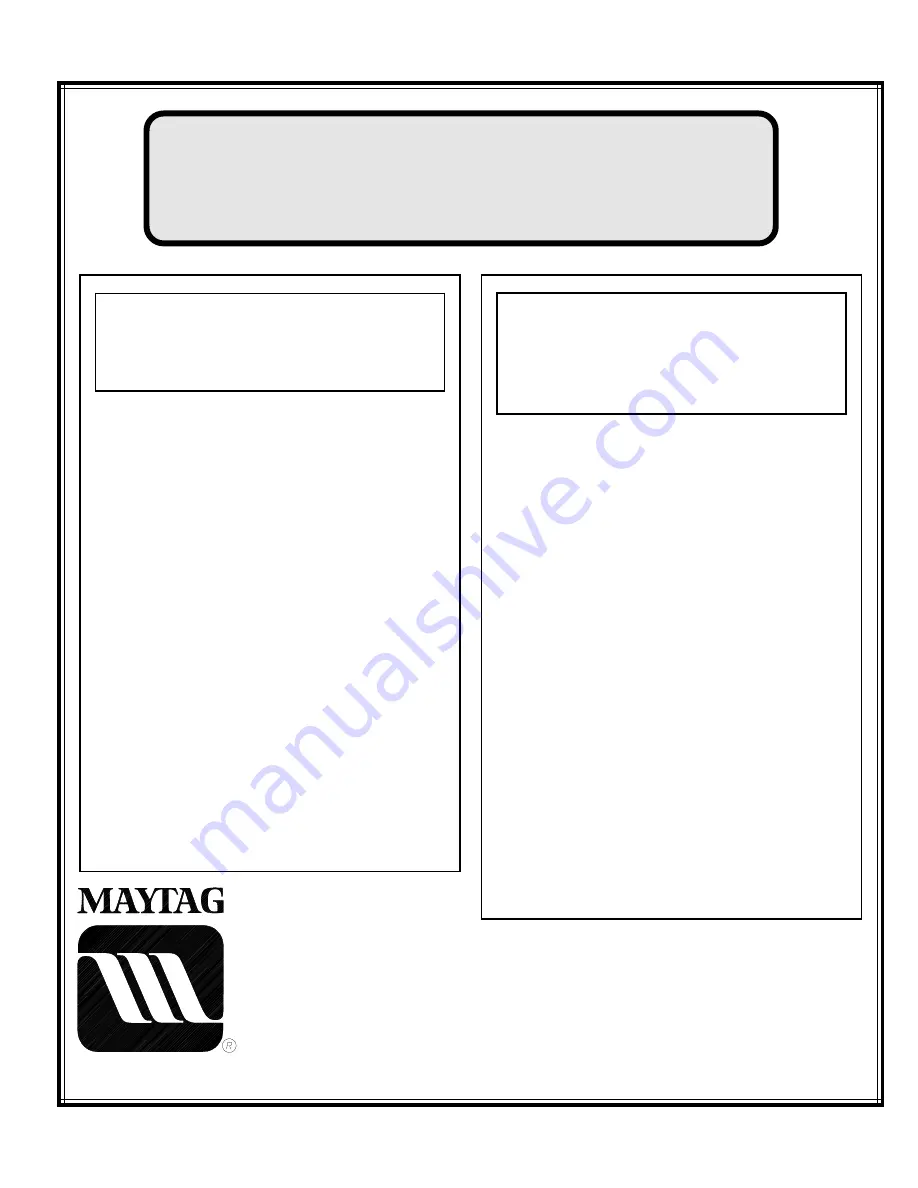
MLG31PCB
Phase 7 Coin
Installation Manual
073003MGOLDSTEIN/tcosta
Part No. 113203
RETAIN THESE INSTRUCTIONS IN A SAFE
PLACE FOR FUTURE REFERENCE
WARNING: For your safety the information in
this manual must be followed to minimize the
risk of fire or explosion or to prevent property
damage, personal injury or death.
Do not store or use gasoline or other flammable
vapors and liquids in the vicinity of this or any
other appliance.
WHAT TO DO IF YOU SMELL GAS:
Do not try to light any appliance.
Do not touch any electrical switch; do not
use any phone in your building.
Clear the room, building or area of all
occupants.
Immediately call your gas supplier from a
neighbors phone. Follow the gas suppliers
instructions.
If you cannot reach your gas supplier, call
the fire department.
Installation and service must be performed by a
qualified installer, service agency or the gas
supplier.
AVERTISSEMENT: Assurez-vous de bien
suivre les instructions données dans cette notice
pour réduire au minimum le risque dincendie
ou dexplosion ou pour éviter tout dommage
matériel, toute blessure ou la mort.
Ne pas entreposer ni utiliser dessence ni
dautres vapeurs ou liquides inflammables à
proximité de cet appareil ou de tout autre
appareil.
QUE FAIRE SI VOUS SENTEZ UNE ODEUR
DE GAZ:
Ne pas tenter dallumer dappareils.
Ne touchez à aucun interrupteur. Ne pas
vous servir des téléphones se trouvant dans
le bâtiment.
Évacuez la pièce, le bâtiment ou la zone.
Appelez immédiatement votre fournisseur
de gaz depuis un voisin. Suivez les
instructions du fournisseur.
Si vous ne pouvez rejoindre le fournisseur
de gaz, appelez le service des incendies.
Linstallation et lentretien doivent être assurés par
un installateur ou un service dentretien qualifié
ou par le fournisseur de gaz.