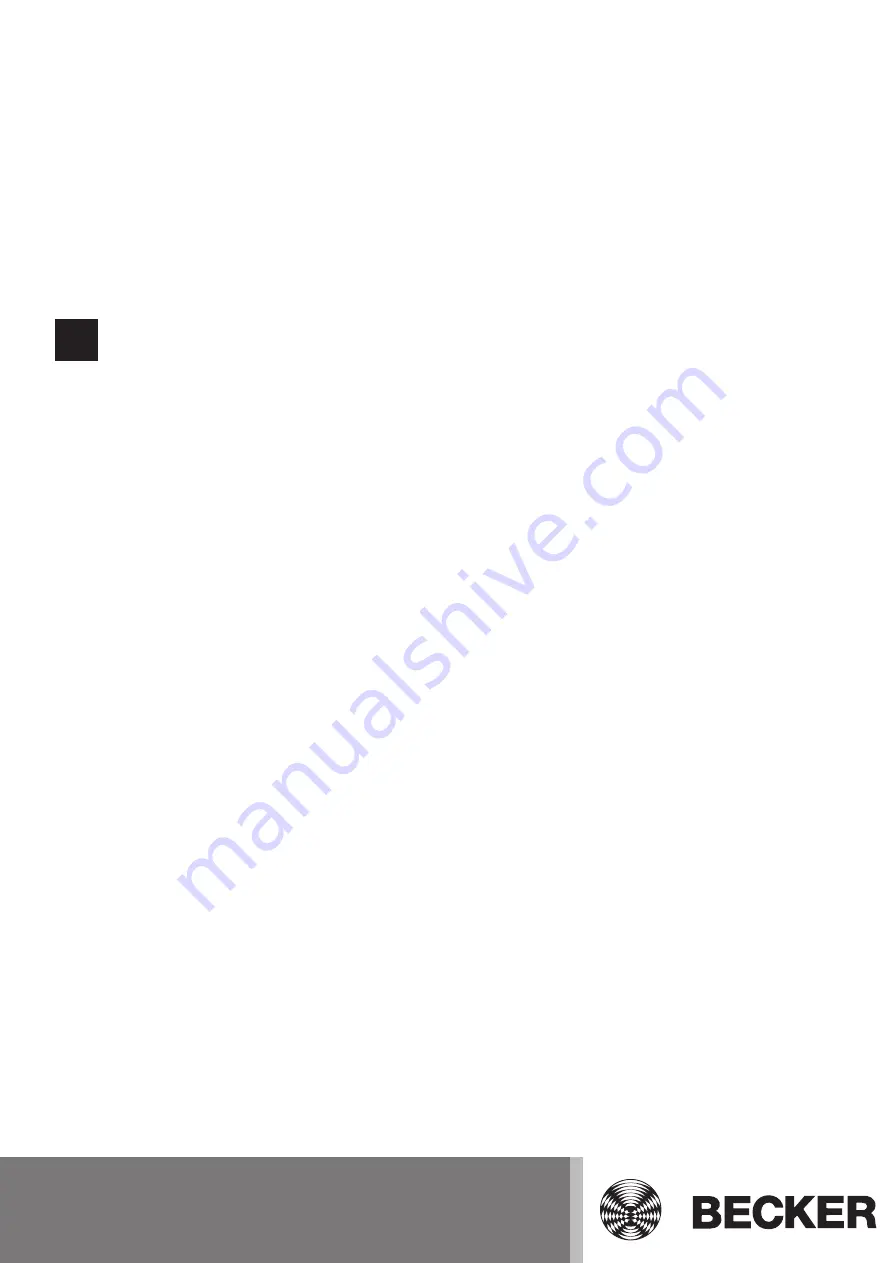
P5-20...R40-17
Model: C18 PLUS
en
Assembly and Operating Instructions
Tubular drive with integrated radio transceiver for
ZIP systems
Important information for:
• Fitters / • Electricians / • Users
Please forward accordingly!
These instructions must be kept safe for future reference.
Becker-Antriebe GmbH
Friedrich-Ebert-Straße 2-4
35764 Sinn/Germany
www.becker-antriebe.com
2010 301 285 0a 06/07/2022
Summary of Contents for P5-20-C18 PLUS
Page 33: ...Declaration of conformity 33 en ...
Page 34: ...34 ...
Page 35: ...35 ...
Page 36: ......