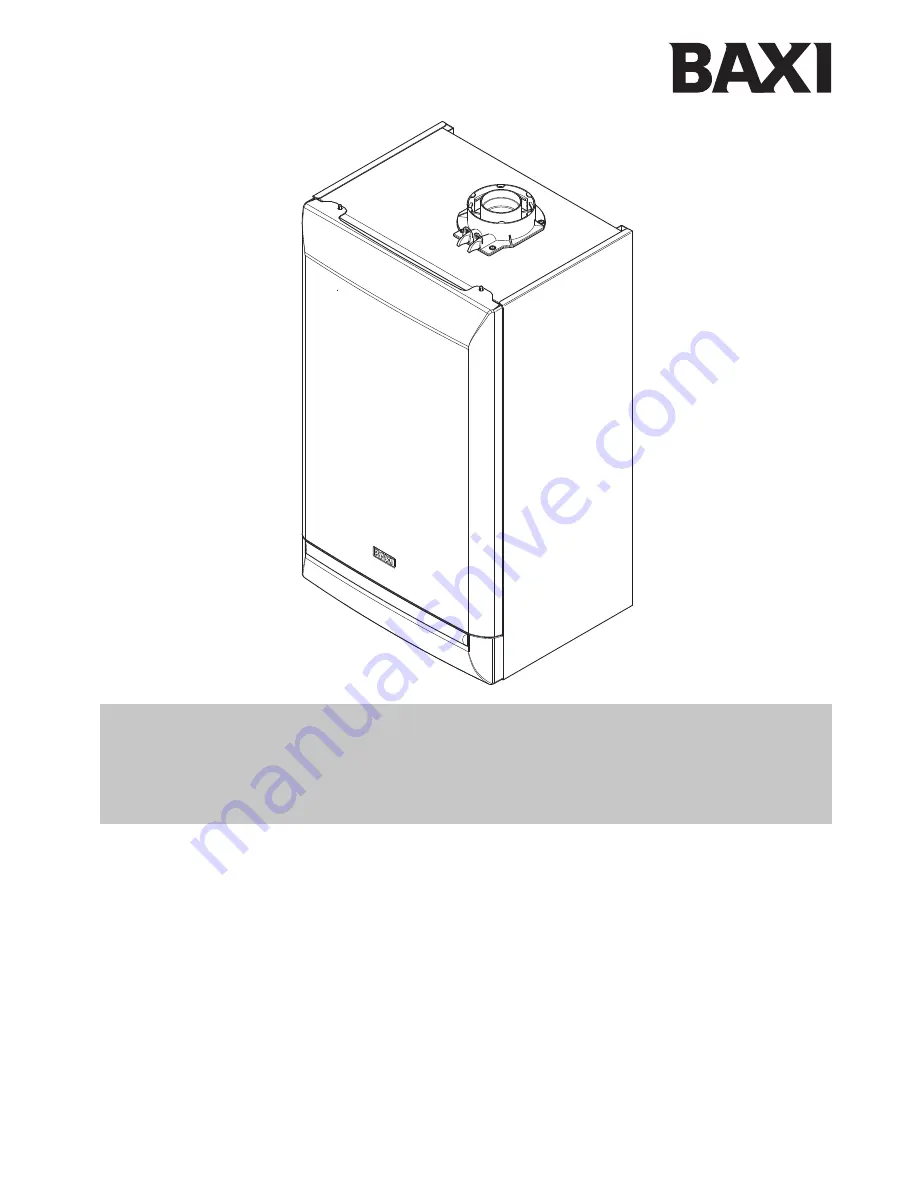
M
Megao System
Installation and Service Manual
Gas Fired Wall Mounted Condensing System Boiler
15 - 18 - 24 - 28 - 32
en
United Kingdom
These instructions include the Benchmark Commissioning Checklist and should be left with the
user for safe keeping. They must be read in conjunction with the Flue Installation Guide.