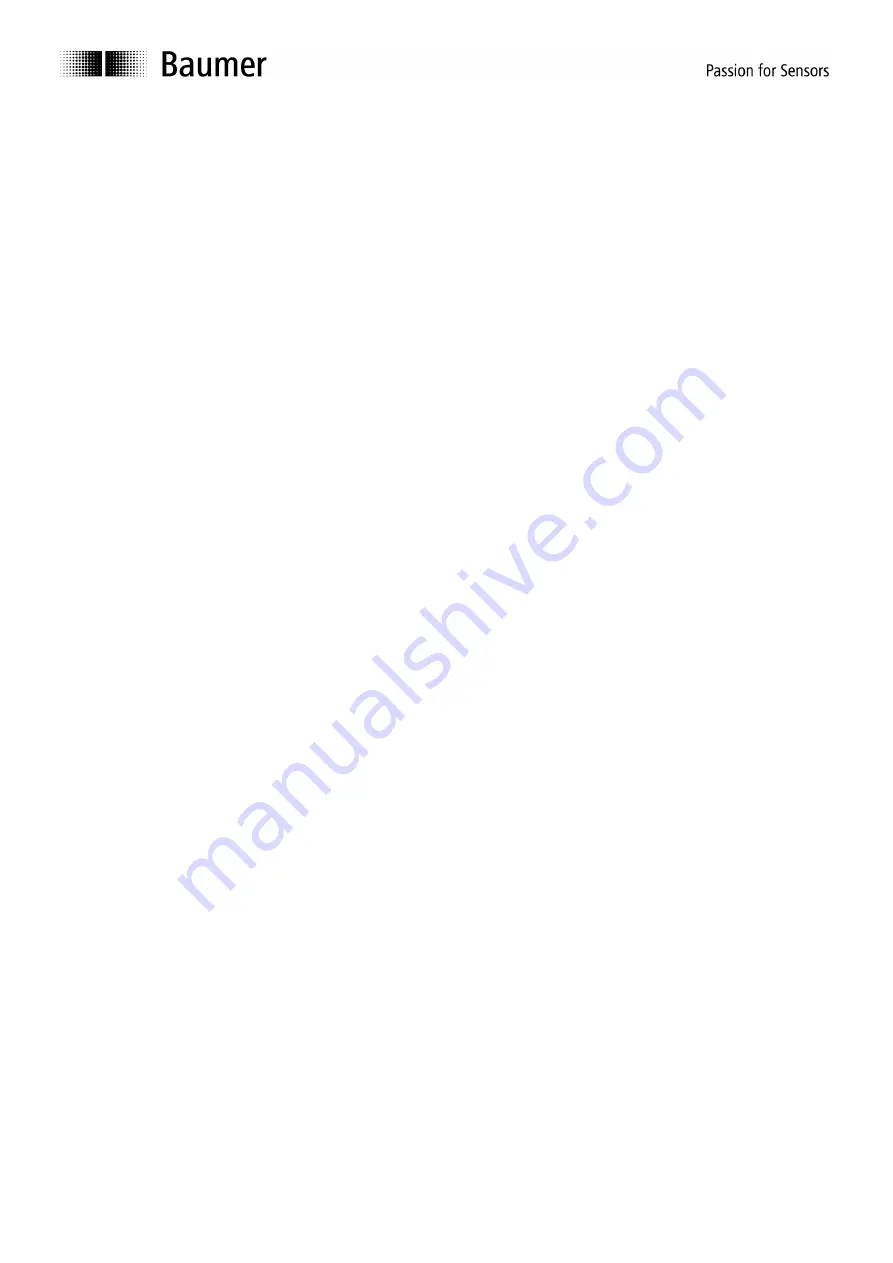
Baumer IVO GmbH & Co. KG
Dauchinger Strasse 58-62
DE-78056 Villingen-Schwenningen
Phone +49 (0)7720 942-0
Fax +49 (0)7720 942-900
05.11 · 174.02.035/4
Subject to technical and design modifications.
www.baumer.com
Errors and omissions excepted.
Manual
Absolute Encoder with CANopen Lift Protocol
Firmaware version from 1.00