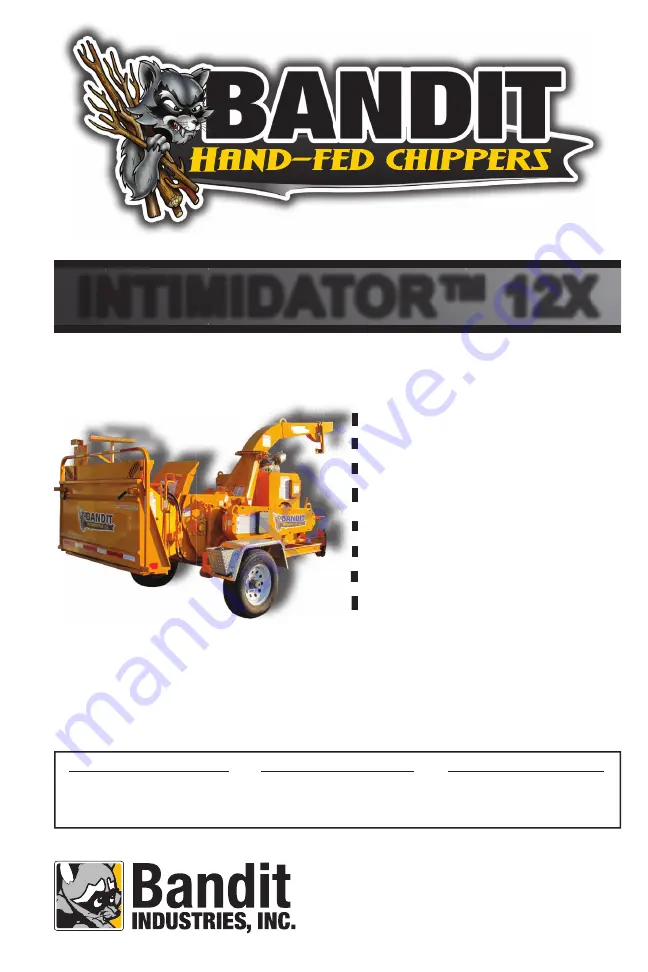
INTIMIDATOR™ 12X
Model No: __________________________
Serial No: __________________________
Engine Make: _______________________
Serial No: __________________________
Clutch Make: ________________________
Model: ___________ S/N _____________
DEALER:
Name: _____________________________
Address: ___________________________
City/State: __________________________
Phone No: __________________________
Delivery Date: _______________________
Copyright 12/19
ATTENTION:
Depending on what replacement parts you are ordering, we will need the following information:
CHIPPER COMPONENTS
Serial Number
Model Number of Chipper
ENGINE COMPONENTS
Brand
Engine Serial Number
Engine Model Number
CLUTCH COMPONENTS
Brand
Clutch Serial Number
Clutch Model Number
INTIMIDATOR™ 12X
OPERATING & PARTS MANUAL
6750 Millbrook Rd. • Remus, MI 49340 • 1-989-561-2270
MANUFACTURED BY BANDIT INDUSTRIES, INC
PHONE:
(
989
)
561-2270
PHONE:
(
800
)
952-0178 IN USA
FAX:
(
989
)
561-2273 ~ SALES DEPT.
FAX:
(
989
)
561-2962 ~ PARTS/SERVICE
WEBSITE:
www.banditchippers.com
Содержание INTIMIDATOR 12X
Страница 18: ......
Страница 80: ...66 12 19 Replacement Parts Model 12X HYDRAULIC FUEL TANK ASSEMBLY 6 9 8 8 4 10 11 3 3 2 2 7 1 5 9...
Страница 84: ...70 12 19 Replacement Parts Model 12X OPTIONAL HYDRAULIC BUMP BAR 1 6 12 14 13 11 10 9 9 15 7 8 2 4 5 5 3 6 7 8...
Страница 86: ...72 12 19 Service Record Model 12X SERVICE RECORD DATE DESCRIPTION AMOUNT...