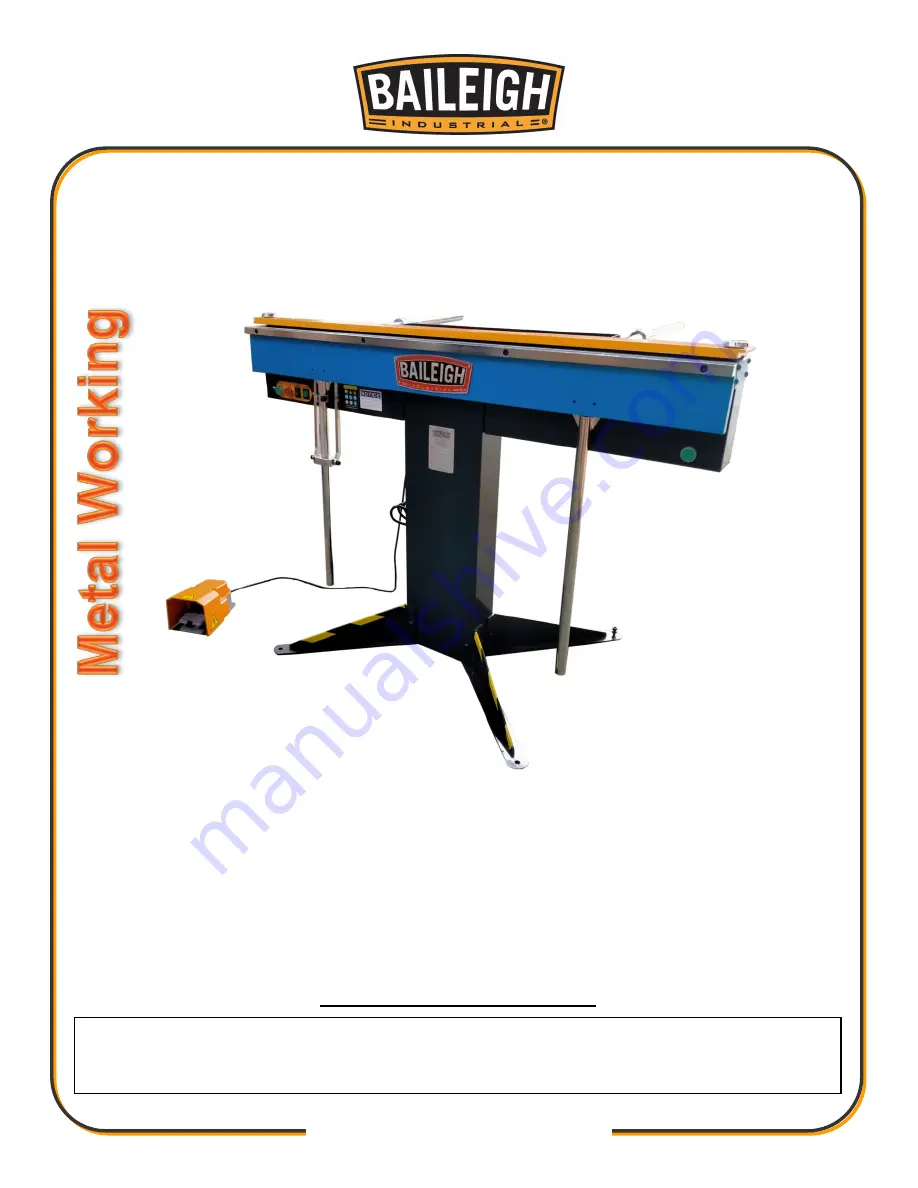
OPERATOR’S MANUAL
MAGNETIC BOX AND PAN BRAKE
MODEL: BB-4816M-V2
Baileigh Industrial
P.O. Box 531
Manitowoc, WI 54221-0531
Phone: 920.684.4990
Fax: 920.684.3944
© 2022 Baileigh Industrial
REPRODUCTION OF THIS MANUAL IN ANY FORM WITHOUT WRITTEN APPROVAL OF BAILEIGH INDUSTRIAL IS
PROHIBITED. Baileigh Industrial, Inc. does not assume and hereby disclaims any liability for any damage or loss
caused by an omission or error in this Operator’s Manual, resulting from accident, negligence, or other occurrence.
Edition 2 03/2023
Summary of Contents for BB-4816M-V2
Page 12: ...10 10 3 4 1 2...
Page 16: ...14 14 OVERALL DIMENSIONS...
Page 30: ...28 28 PARTS DIAGRAM...