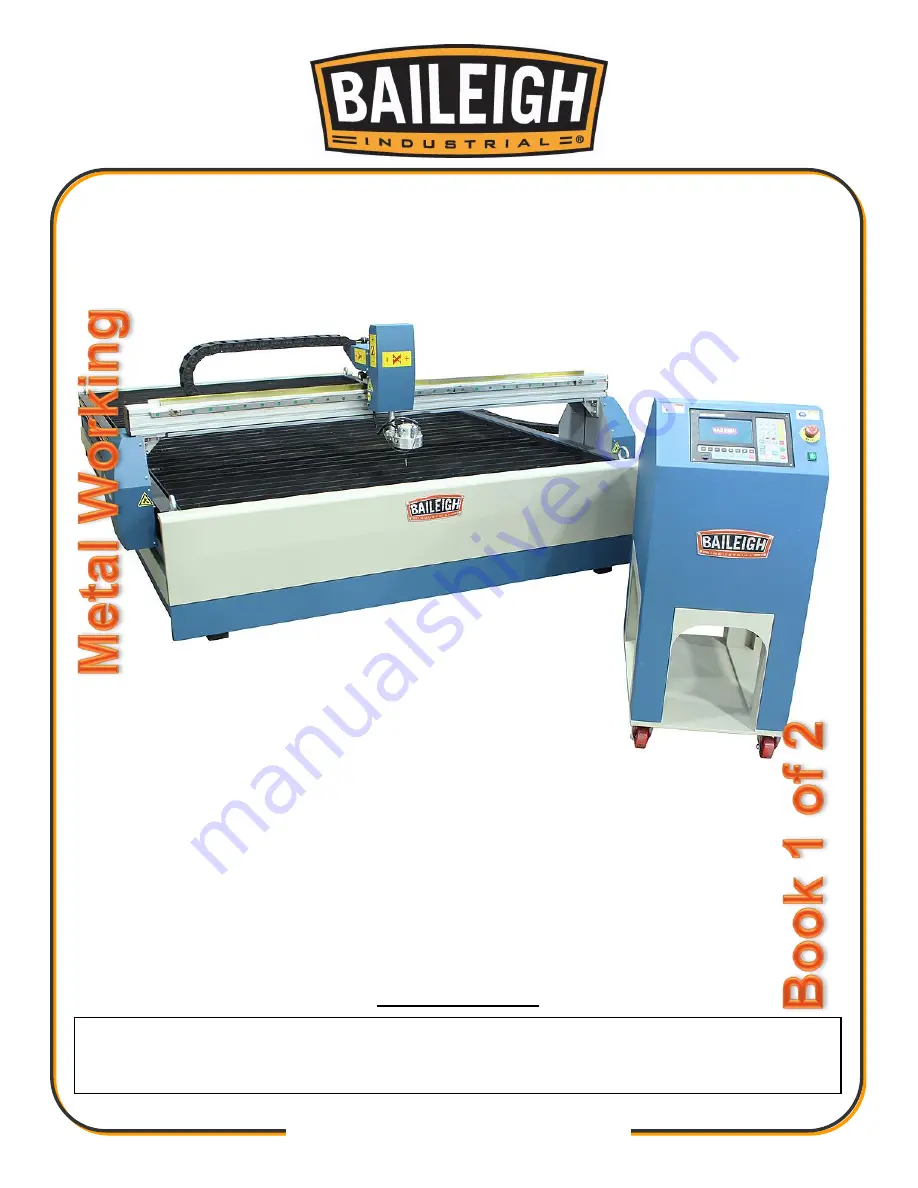
OPERATOR’S MANUAL
PLASMA CUTTING TABLE
MODEL: PT-44AH-W
Baileigh Industrial Holdings LLC
P.O. Box 531
Manitowoc, WI 54221-0531
Phone: 920.684.4990
Fax: 920.684.3944
© 2019 Baileigh Industrial Holdings LLC
REPRODUCTION OF THIS MANUAL IN ANY FORM WITHOUT WRITTEN APPROVAL OF BAILEIGH INDUSTRIAL
HOLDINGS LLC IS PROHIBITED. Baileigh Industrial Holdings LLC, Inc. does not assume and hereby disclaims any
liability for any damage or loss caused by an omission or er
ror in this Operator’s Manual, resulting from accident,
negligence, or other occurrence.
Rev. 07/2019
Summary of Contents for PT-44AH-W
Page 43: ...41 41 ELECTRICAL DIAGRAM ...
Page 46: ...44 44 NOTES ...