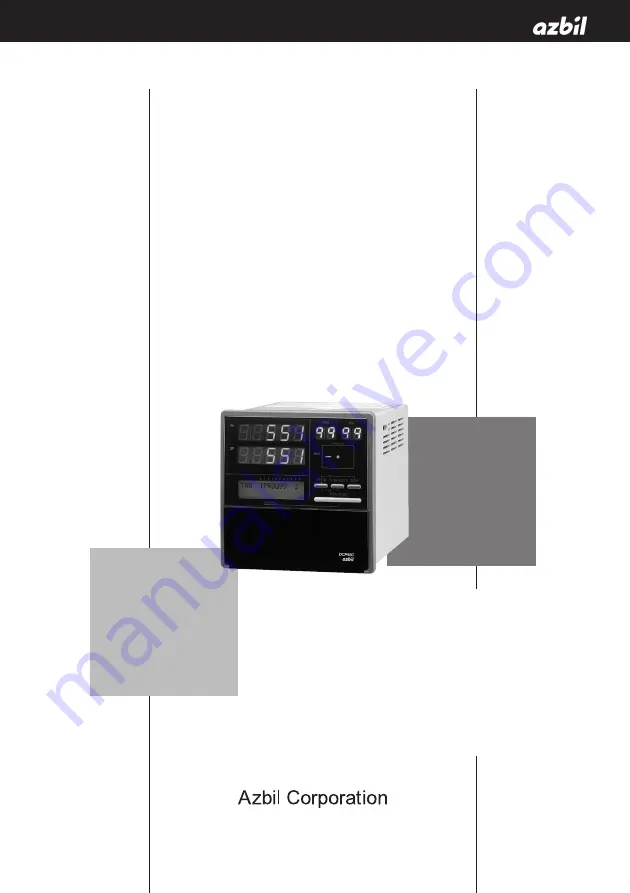
DCP551 Mark
ΙΙ
DIGITRONIK
Digital Control Programmer
User's Manual
No. CP-SP-1032E
Thank you for purchasing an Azbil
Corporation product.
This manual contains information for
ensuring the correct use of this
product.
It also provides necessary information
for installation, maintenance, and
troubleshooting.
This manual should be read by those
who design and maintain equipment
that uses this product. Be sure to
keep this manual nearby for handy
reference.
(Not for use in Japan)