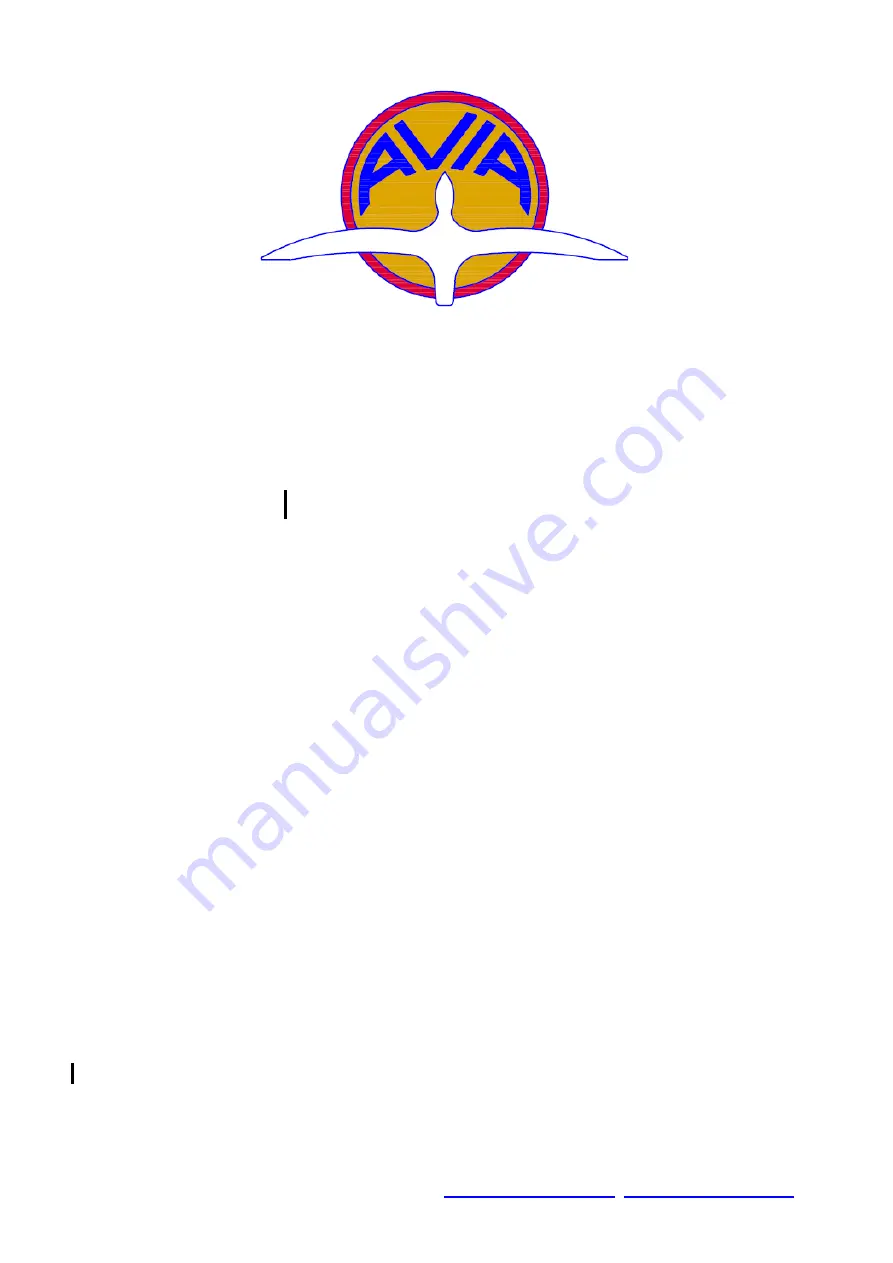
O
O
P
P
E
E
R
R
A
A
T
T
I
I
O
O
N
N
A
A
N
N
D
D
I
I
N
N
S
S
T
T
A
A
L
L
L
L
A
A
T
T
I
I
O
O
N
N
M
M
A
A
N
N
U
U
A
A
L
L
REVERSIBLE HYDRAULICALLY CONTROLLED
VARIABLE PITCH PROPELLERS
(CONSTANT SPEED)
AV-723-1-D-C-F-R(P)
AV-725-1-E-C-F-R(P), (W)
AV-803-1-E-C-F-R(W)
AV-804-1-E-C-F-R(W)
AV-844-1-E-C-F-R(G), (P), (W)
Document number:
E
E
N
N
-
-
1
1
3
3
2
2
0
0
ATA 61-10-20
Issue 4: October 06, 2017
Revision: March 4, 2019
The technical content of this document is approved
under authority of DOA No. EASA.21J.072.
Avia Propeller s.r.o., Beranových 65/666, 199 00 Praha 9 - Let
ň
any, CZECH REPUBLIC
Tel.: +420/296336511, Fax.: +420/296336519,
,
www.aviapropeller.com