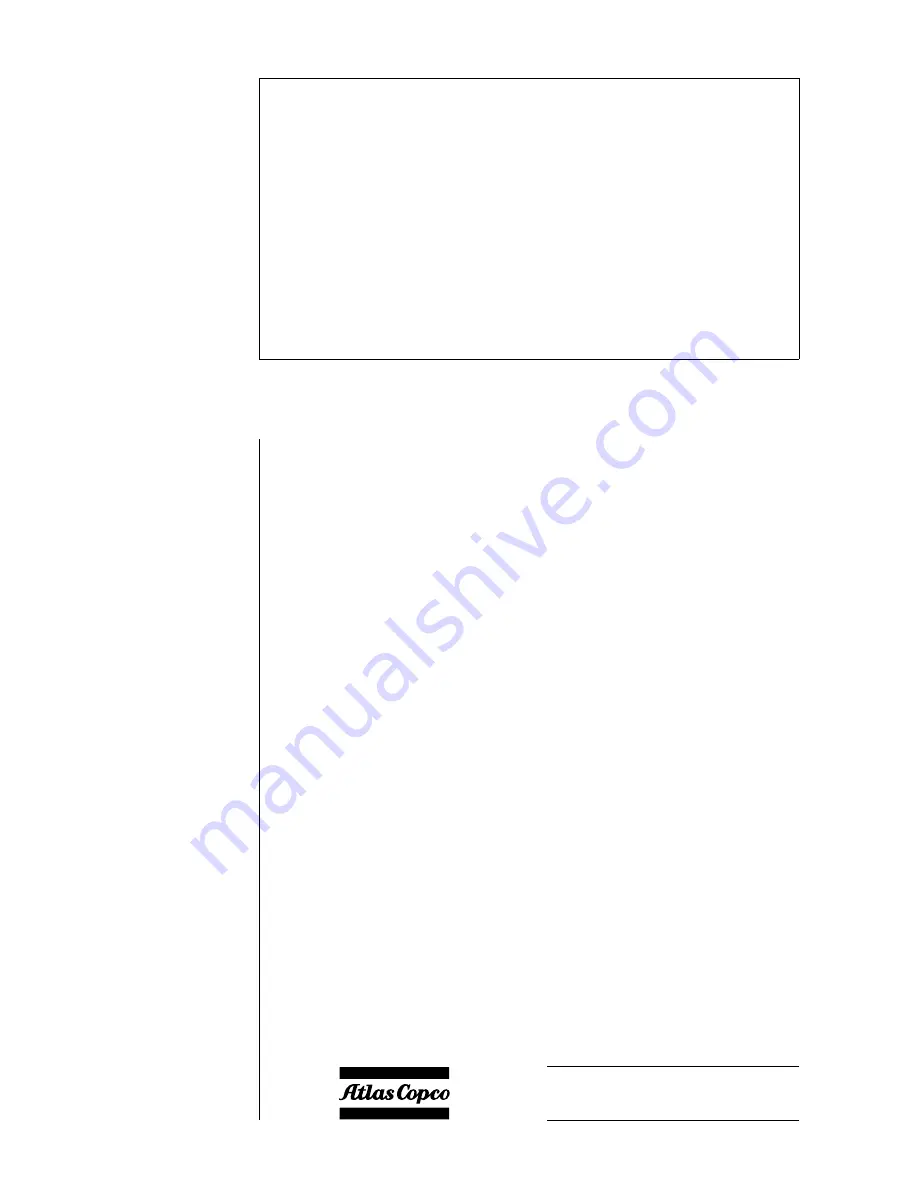
ATLAS COPCO - PORTABLE AIR DIVISION
www.atlascopco.com
Instruction Manual
for Portable Compressors
XASE1600 Gd
Instruction manual for portable compressors ...................................... 3
Manuel d’instructions pour compresseurs mobiles .......................... 25
Libro de instrucciones para compresores transportables ................. 47
Manual de instruções para compressores portáteis .......................... 69
Circuit diagrams – Schémas de circuits –
Esquema de conexiones – Esquemas eléctricos ................................ 91
Parts list – Liste de pièces – Lista de las partes – Lista de peças....... 97
Glossary – Glossaire – Glosario
– Glossário ..................................... 165
Registration code
Collection:APC XII
Tab
:
38
Printed Matter N°
2950 0400 04
EN
09/2001