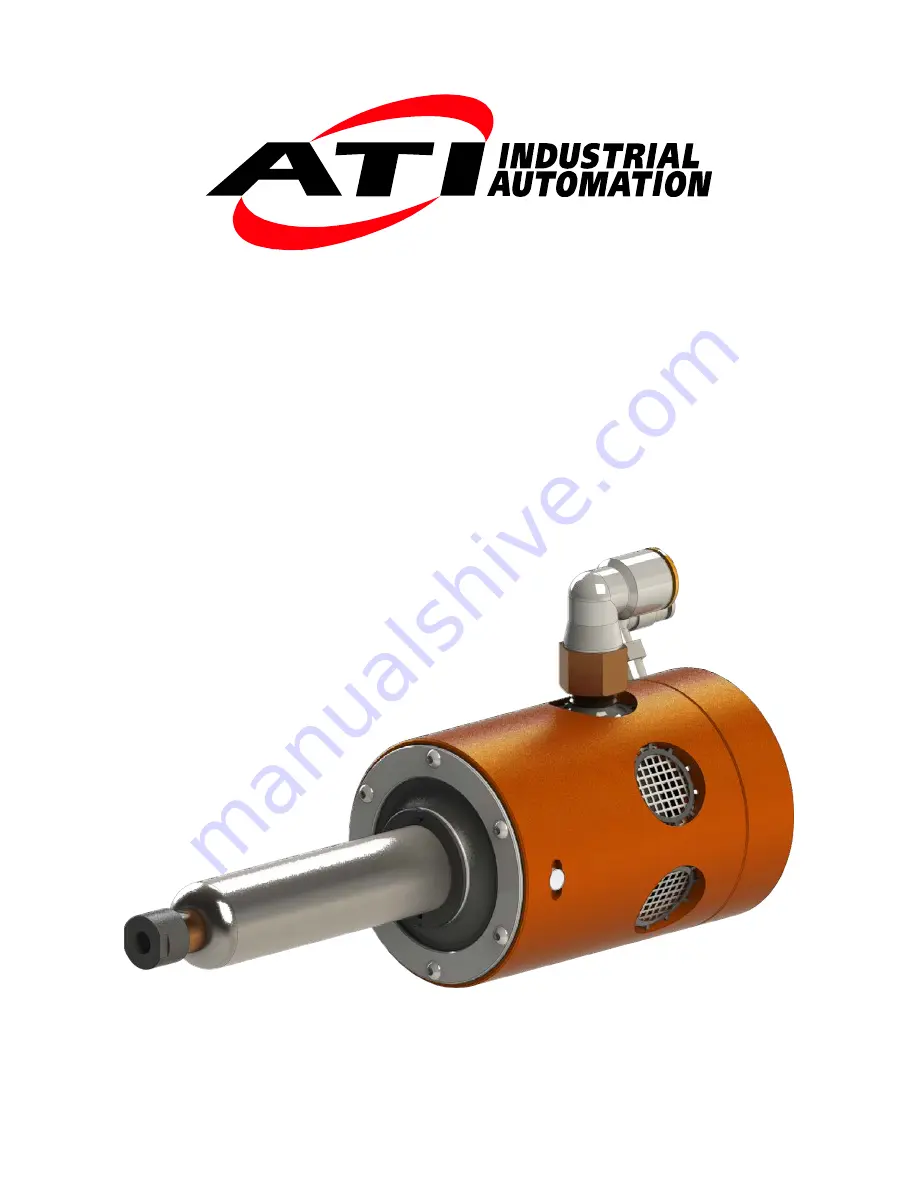
Engineered Products for Robotic Productivity
Pinnacle Park • 1031 Goodworth Drive • Apex, NC 27539 USA • Tel: +1.919.772.0115 • Fax: +1.919.772.8259 • www.ati-ia.com • Email: [email protected]
ATI Single-Axis, Radially-Compliant
Robotic Deburring Tools
Flexdeburr™
(Model 9150-RS-340)
Product Manual
Document #: 9610-50-1016