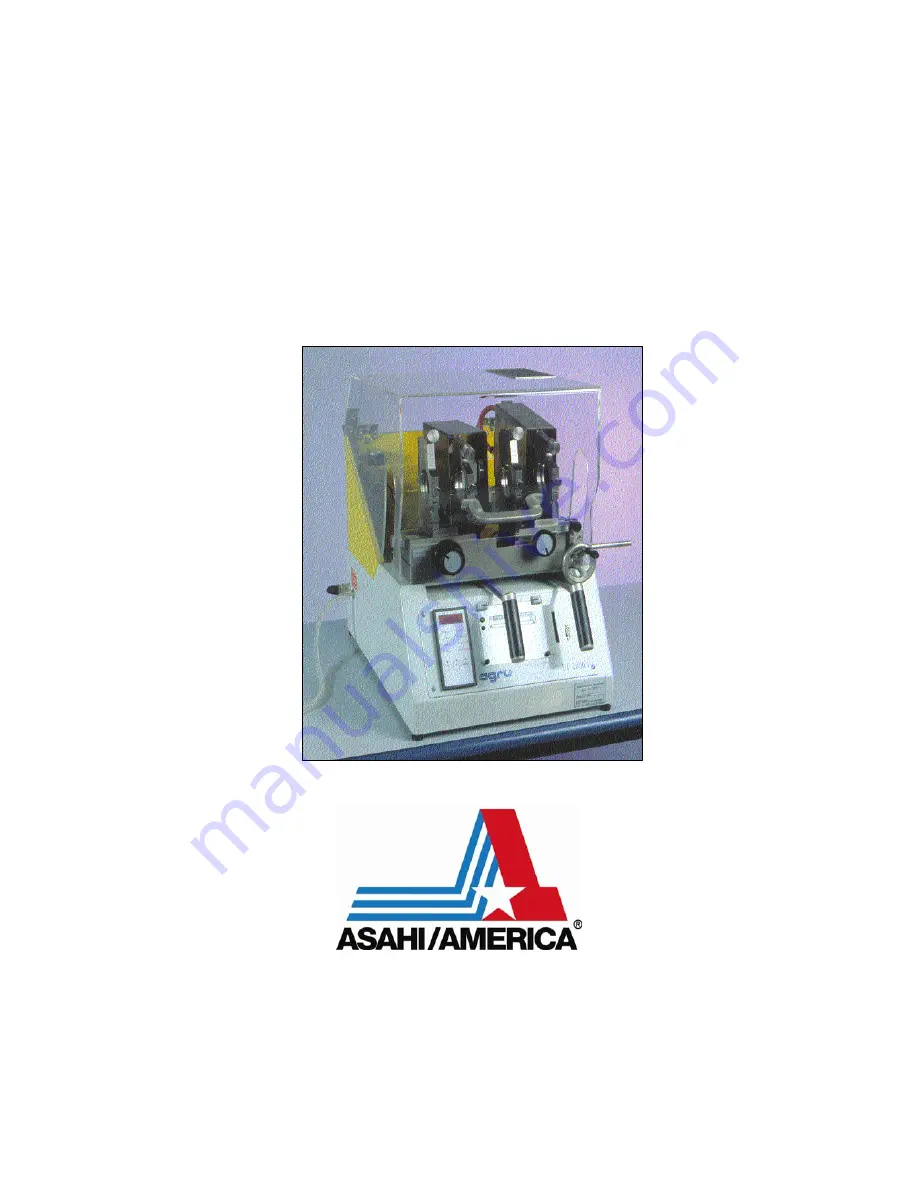
Proweld™ Equipment Manual
UF2000/1
35 Green Street, PO Box 653, Malden, MA 02148
Tel: (781) 321-5409 - Fax: (781) 321-4421 Toll Free: (800) 343-3618
www.asahi-america.com – [email protected]
Direct Sales: East (800) 232-7244
Proweld™ Equipment Manual
UF2000/1
35 Green Street, PO Box 653, Malden, MA 02148
Tel: (781) 321-5409 - Fax: (781) 321-4421 Toll Free: (800) 343-3618
www.asahi-america.com – [email protected]
Direct Sales: East (800) 232-7244