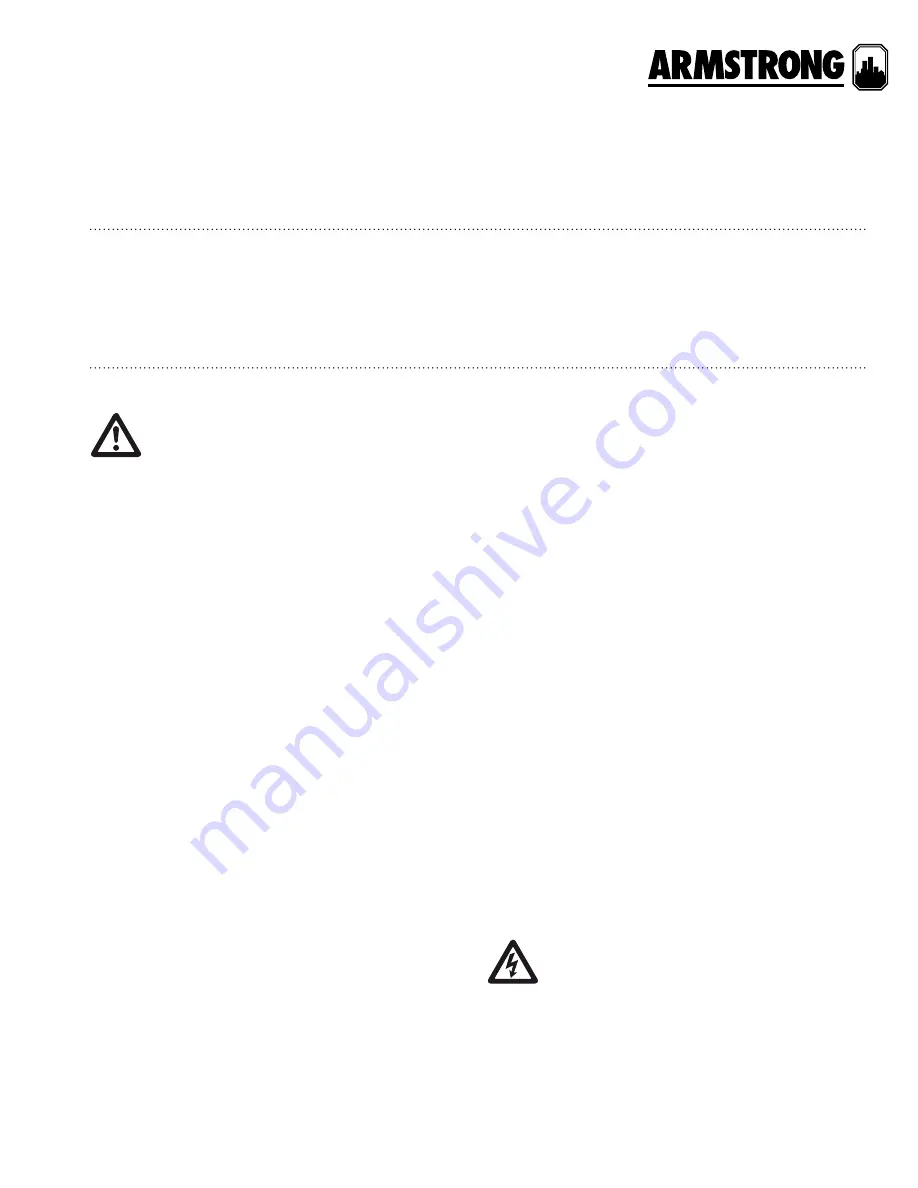
caution
Always disconnect power supply from motor
before servicing.
1.0 installation
For convenience, Armstrong circulators generally are installed
in vertical pipelines, but may be changed easily on the job for
horizontal pipelines or for opposite flow directions. To make the
change, remove the body capscrews, taking care body gasket is
kept in position, and rotate body to desired direction at
90°
or
180°
from the original position.
With the arrow on the body pointing in direction of the flow,
insert body capscrews and tighten evenly. On models
s55
and
s57
a gap between the bearing bracket and pump body (vo-
lute) is normal. Do no over tighten body capscrews! Turn pump
shaft manually at coupler to make sure shaft turns freely and
impeller does not rub in body. Always install with motor shaft
in a horizontal position. For
non maintenance free
models the
oil cups or oil well cover must be facing up.
All
ecm
models are shipped for upward discharge as pumps of
this size usually are installed in an upward direction on hydronic
systems, so the point of zero pressure change - namely, the
compression tank connection - can be made easily to the sys-
tem on the suction side of the circulator.
The pump should be installed in a position to permit proper
lubrication and servicing. Motor and bearing brackets are to be
kept free of insulation. Pump and motor unit are designed to be
supported by the in-line piping only. Do not support in any oth-
er manner. A height of approximately four feet above the floor
is recommended. When placing the pump between flanges,
tighten flange bolts evenly and do not tighten excessively.
Gate valves should be installed on the discharge and suction
side of the pump to facilitate service. On larger pump sizes, a
check valve should be located on the discharge side of pump
between the pump body and the gate valve to prevent damage
due to water hammer.
2.0 system cleanliness
Before starting the pump, the system must be thoroughly
cleaned, flushed and drained, then replenished with clean
liquid. Welding slag and other foreign materials, 'stopleak'
and cleaning compounds, excessive or improper water treat-
ment - all are detrimental to the pump. Warranty will be void if
any of these conditions are allowed to exist. (Refer to
File no.
6090.645
design and care of closed hydronic systems.)
3.0 starting up
The pump must be fully primed on start-up. Fill system piping
and pump body with liquid and vent complete system, turning
pump by hand to dislodge air from body. Make sure fittings and
drain valves are airtight, then add any additional fill required.
Check motor against available electric supply, then start pump
making sure rotation is correct. When viewed from motor end,
rotation is clockwise. If pressure does not develop, stop pump,
re-check, vent and fill. Never attempt to fill the system when
the pump is running.
note:
ecm
motors have a
15
second soft start-up time once plugged in,
and a
30
second time to achieve full speed (thus different from standard
induction motors)
4.0 electrical wiring
The electrical wiring must be installed in strict ac-
cordance with the Canadian Electrical Code (Canada)
or the U.S. National Electrical Code (USA),or
bs7671
(Europe) as well as local codes and regulations.
1
Electrical installation should be conducted by a qualified
electrician. Installers should be equipped with proper
personal protective equipment.
2
Always make sure the electric power is disconnected and
locked out before wiring the circulator.
File No:
10.791
Date:
june 17, 2019
Supersedes:
10.791
Date:
april 6, 2018
IN-LINE ECM CIRCULATING PUMPS
|
MODELS
S55, 57, 69 AND H53, 54, 63 TO H67
|
I N S TA L L AT I O N
A N D O P E R AT I N G I N S T R U C T I O N S