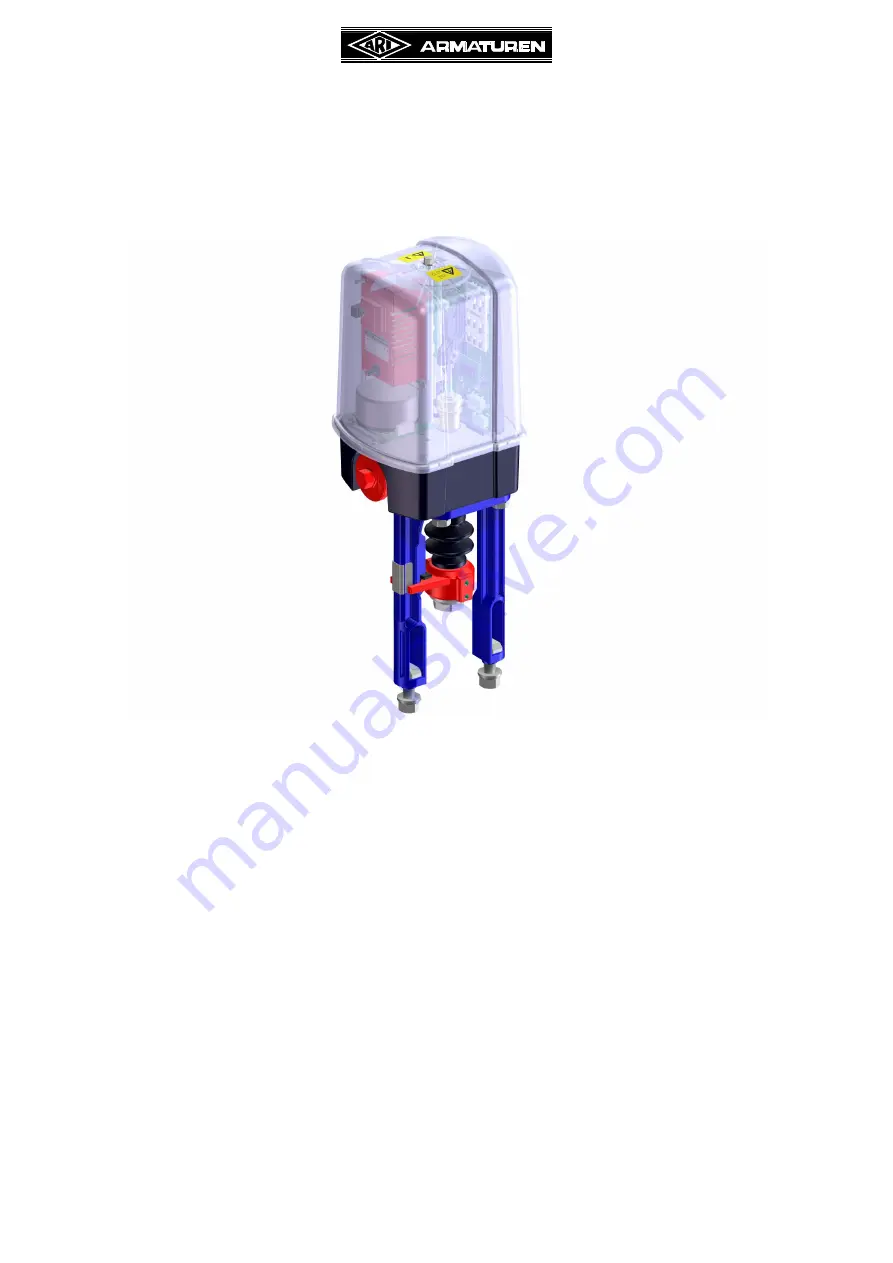
Rev. 0040501006 3814 englisch
1.0 General information on operating instructions............................................................................................. 2-3
2.0 Notes on possible dangers ............................................................................................................................. 2-3
Operating and Installation Instructions
Thrust actuator
ARI-PREMIO
®
-Plus 2G
Inhaltsverzeichnis