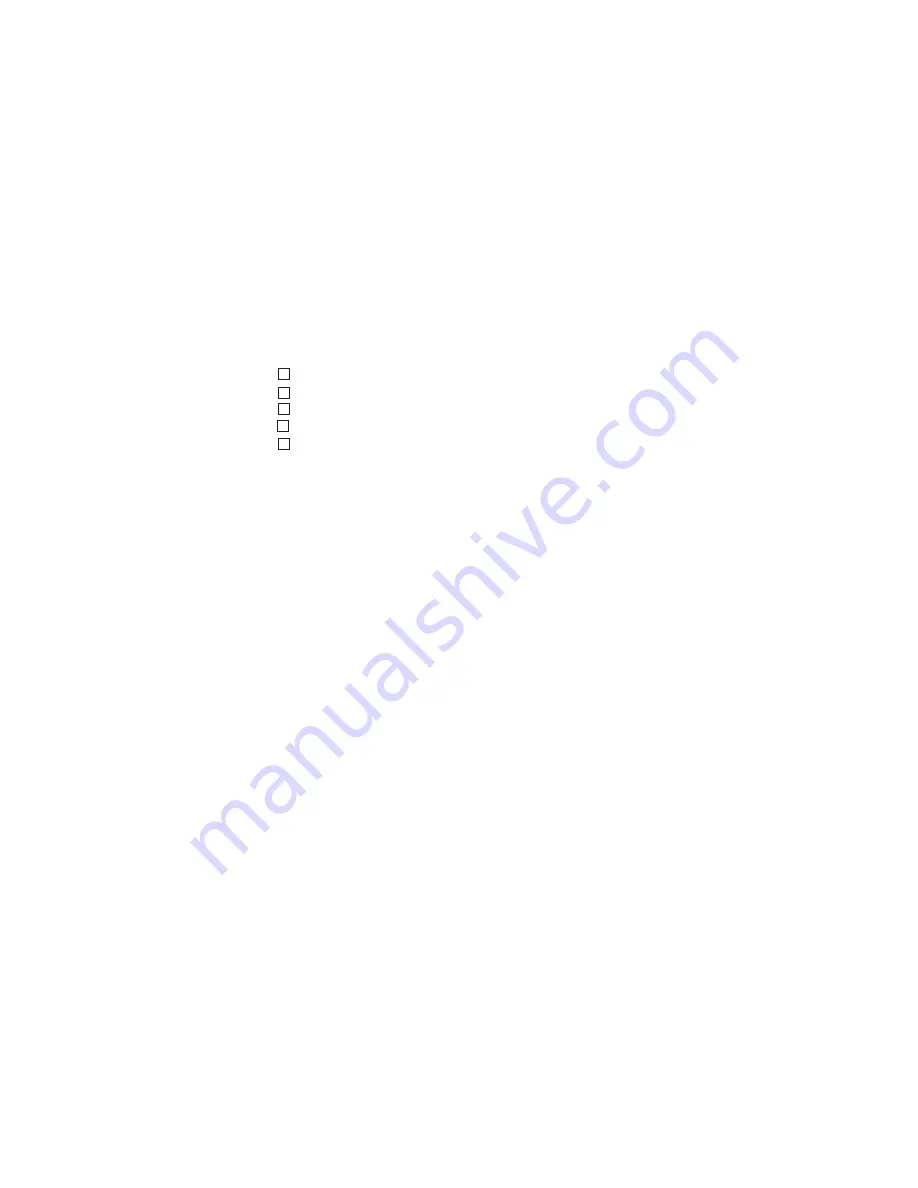
Dear Customer
This instruction manual will help you get to know your new machine. Read the
manual carefully and you will soon be familiar with all the great features of your
new product. Meanwhile, please remember safety rules and operate as
instructed.
If you treat your product carefully, this definitely helps to prolong its enduring
quality and reliability-things which are both essential prerequisites for getting
outstanding results.
Production specification may change without advance notice.
The model you purchase is for:
Dura ARC200
Dura ARC200II
Please find corresponding models from the “Contents”.
Important:
Please take special note of safety rules and operate as instruction in case of
damage and serious injury.
Dura ARC160
Dura ARC160II
Dura ARC250
1
Summary of Contents for Dura ARC160
Page 31: ...MEMO ...