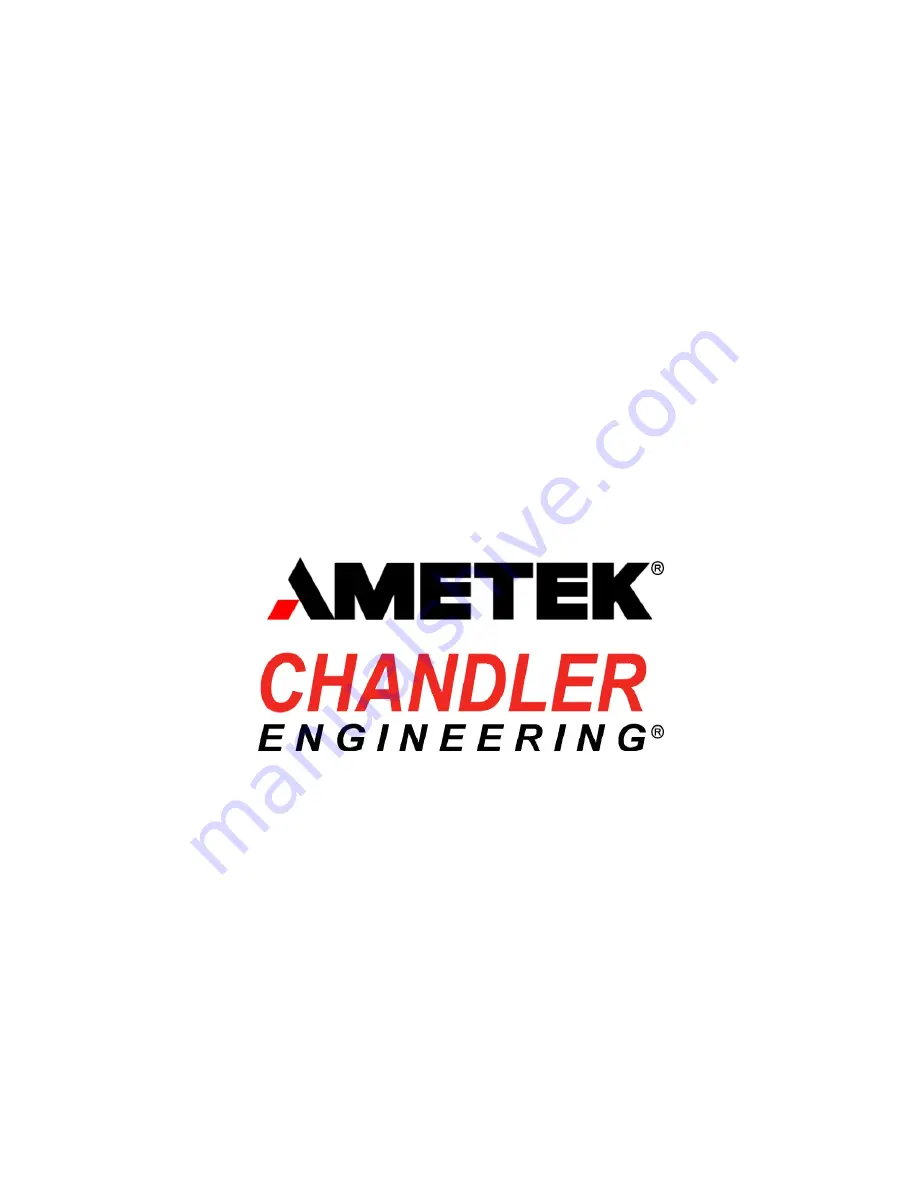
Instruction Manual
Pressurized Curing Chamber
Model 1910
(Original Instructions)
Revision B – September 2019
P/N: 19-0175-CE
S/N: ____________
2001 N. Indianwood Ave.
Broken Arrow, OK 74012
Telephone: 918-250-7200
Fax: 918-459-0165
E-mail: [email protected]
Website: http://www.chandlereng.com
Summary of Contents for Chandler Engineering 1910
Page 4: ...T 2 TABLE OF CONTENTS This page is intentionally left blank ...
Page 10: ...P 6 PREFACE This page is intentionally left blank ...
Page 12: ...1 2 SECTION 1 INSTALLATION This page is intentionally left blank ...
Page 21: ...SECTION 2 OPERATION 2 9 Help Screen The Help Screen displays this manual ...
Page 24: ...2 12 SECTION 2 OPERATION This page is intentionally left blank ...
Page 27: ......
Page 29: ...4 2 SECTION 4 TROUBLESHOOTING GUIDE This page is intentionally left blank ...
Page 31: ...5 2 SECTION 5 REPLACEMENT PARTS This page is intentionally left blank ...
Page 33: ......
Page 38: ...CHANDLER ENGINEERING ...
Page 40: ...P1 P7 P11 PLC1 P3 P18 P12 P5 P6 CHANDLER ENGINEERING ...
Page 41: ...CHANDLER ENGINEERING ...