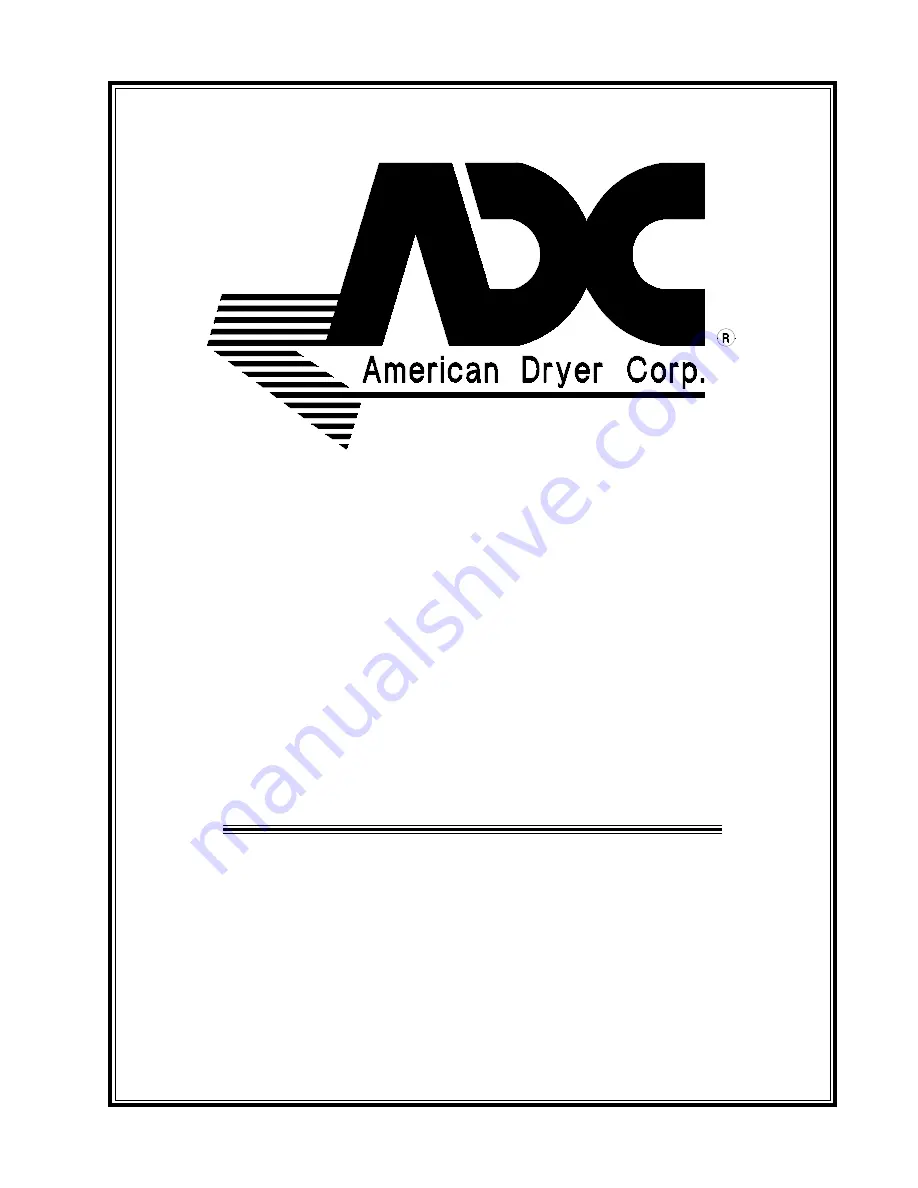
AD-540
Mechanical/Electrical
Service Procedure
090603SRS/tcosta
ADC
Part No. 450246
American Dryer Corporation
88 Currant Road
Fall River, MA 02720-4781
Telephone: (508) 678-9000 / Fax: (508) 678-9447
e-mail: [email protected]
www.amdry.com
Summary of Contents for AD-540
Page 64: ...60 ...
Page 65: ...ADC450246 1 09 08 03 0 ...