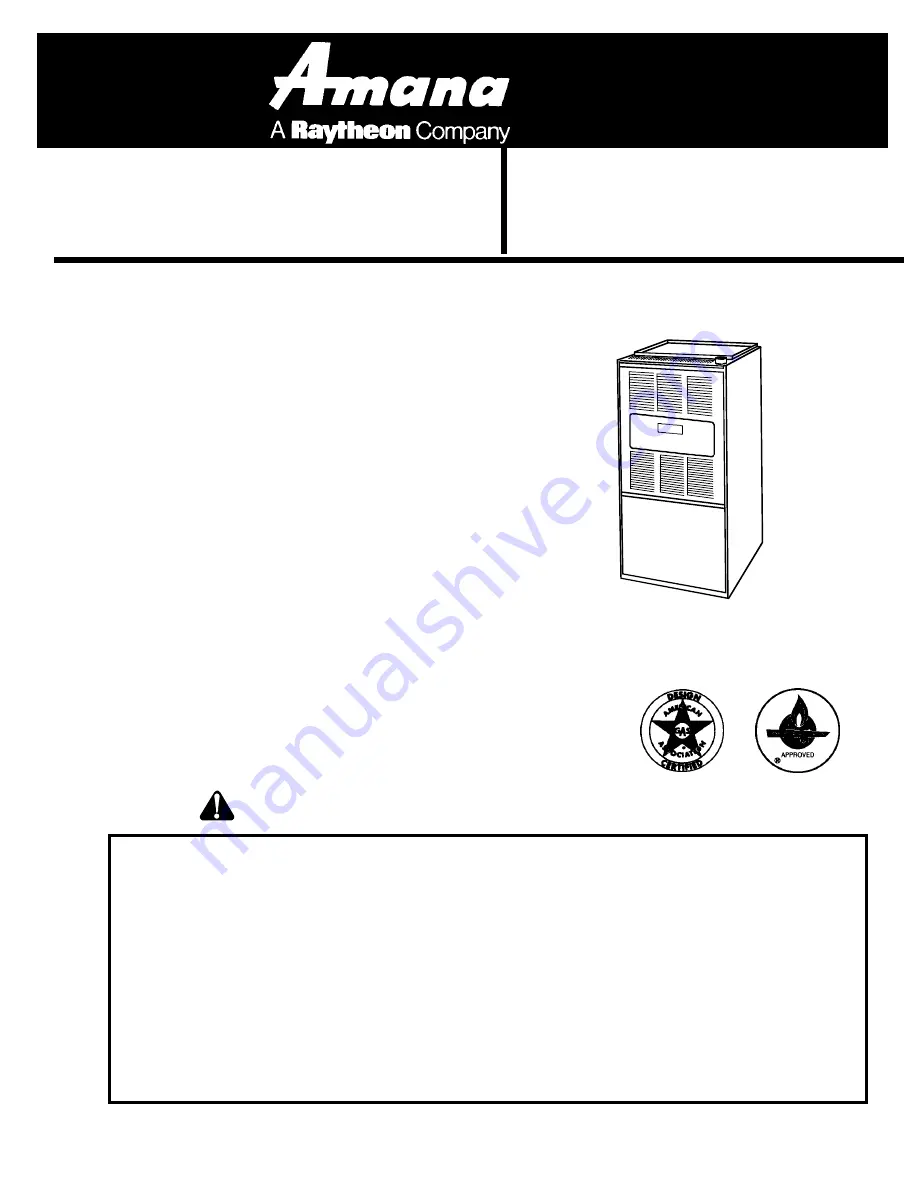
August 1996 (1)
As a professional installer you have an obligation to
know the product better than the customer. This
includes all safety precautions and related items.
Prior to actual installation, thoroughly familiarize your-
self with this Instruction Manual. Pay special atten-
tion to all safety warnings. Often during installation or
repair it is possible to place yourself in a position
which is more hazardous than when the unit is in
operation.
Remember, it is your responsibility to install the
product safely and to know it well enough to be able
to instruct a customer in its safe use.
Safety is a matter of common sense...a matter of
thinking before acting. Most dealers have a list of
specific good safety practices...follow them.
The precautions listed in this Installation Manual
should not supersede existing practices but should
be considered as supplemental information.
Amana Refrigeration, Inc.
Fayetteville, TN 37334
ATTENTION INSTALLING PERSONNEL
Amana Forced Air Central Furnace Design Complies With Requirements
Embodied in The American National Standard / National Standard of Canada
Shown Below.
ANSI Z21.47CAN/CGA-2.3 Central Furnaces
GUX-X, GUC-X, and GUD-X
Gas Fired Warm Air
Furnace
RECOGNIZE THIS SYMBOL AS A SAFETY PRECAUTION
Installation Instructions
Affix this manual, Specification Sheet and Users
Information Manual adjacent to the furnace.
Contents
To The Owner................................................................................. 2
To The Installer ............................................................................... 2
I. Safety and Unit Location............................................................ 3
II. General Information ................................................................... 4
III. Air Requirements ....................................................................... 6
IV. Vent Pipe (All Models) and Combustion Air Pipe
(GUD Models) Materials .......................................................... 8
V. Vent Piping - GUX (All Installations),
GUC (All Installations), and GUD (One Pipe Installations) .... 9
VI. Combustion Air And Vent Piping (GUD - Two Pipe) ............. 11
VII. Condensate Piping ..................................................................15
VIII. Gas Piping ..............................................................................16
lX. Electrical Wiring .......................................................................20
X. Circulating Air and Filters........................................................23
XI. Sequence of Operation ............................................................24
XII. Start-Up and Adjustment ........................................................25
XIII. Maintenance ...........................................................................29
XlV. Functional Parts List ..............................................................32
10318715