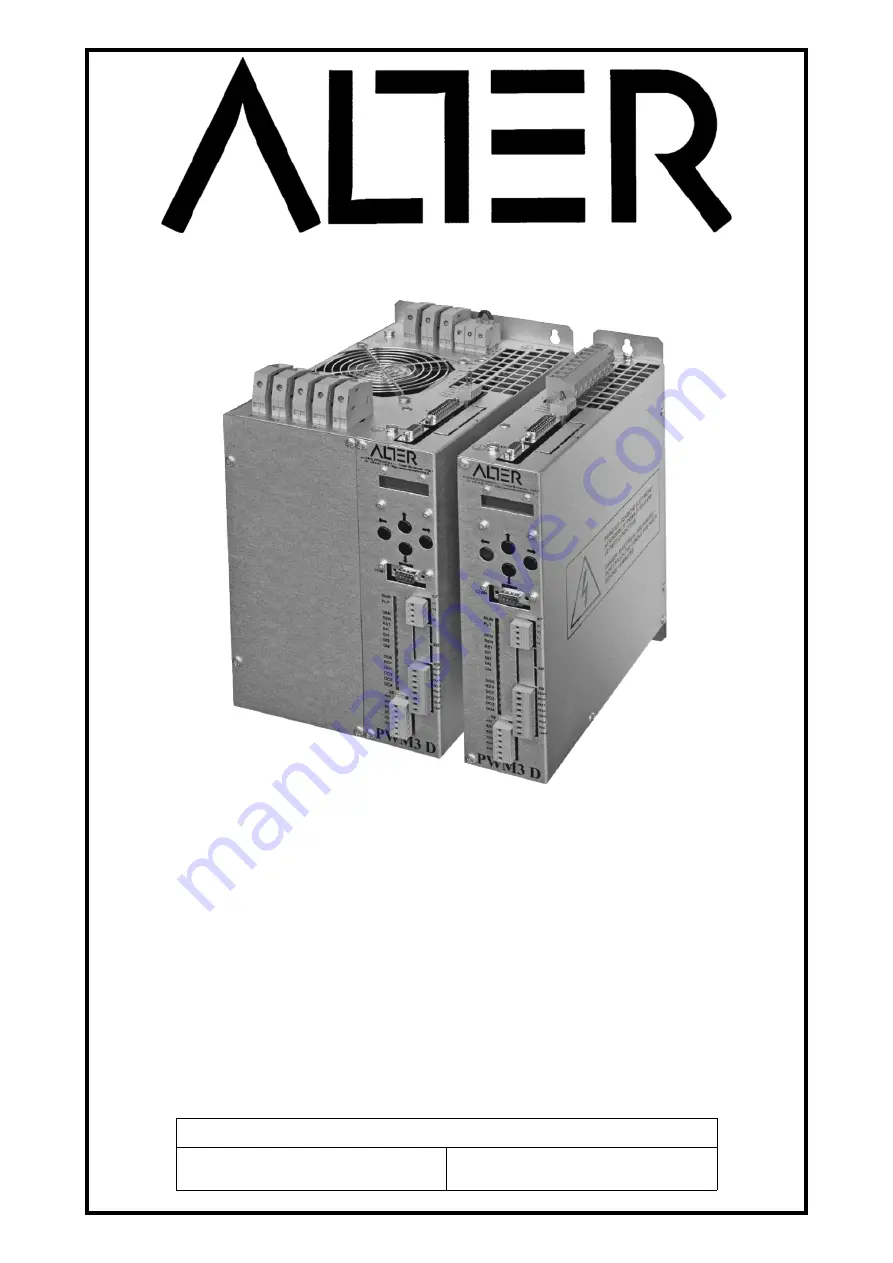
ALTER ELETTRONICA s.r.l.
15033 Casale Monferrato (AL) – ITALY
PWM3D-001
PWM3D-011
Drive 4 quadrants series PWM Digital
For brushless and DC motors with transducer
Instructions
Instructions
manual
manual
:
:
91/121
91/121
- Version
- Version
6.3
6.3
- Date:
- Date:
17/11/2021
17/11/2021
Compatible with Firmware V
Compatible with Firmware V
6.x
6.x
Combined with the drive:
Type No.: ___
/
___ ___ ___
Serial No.: ___ ___ ___ ___ ___