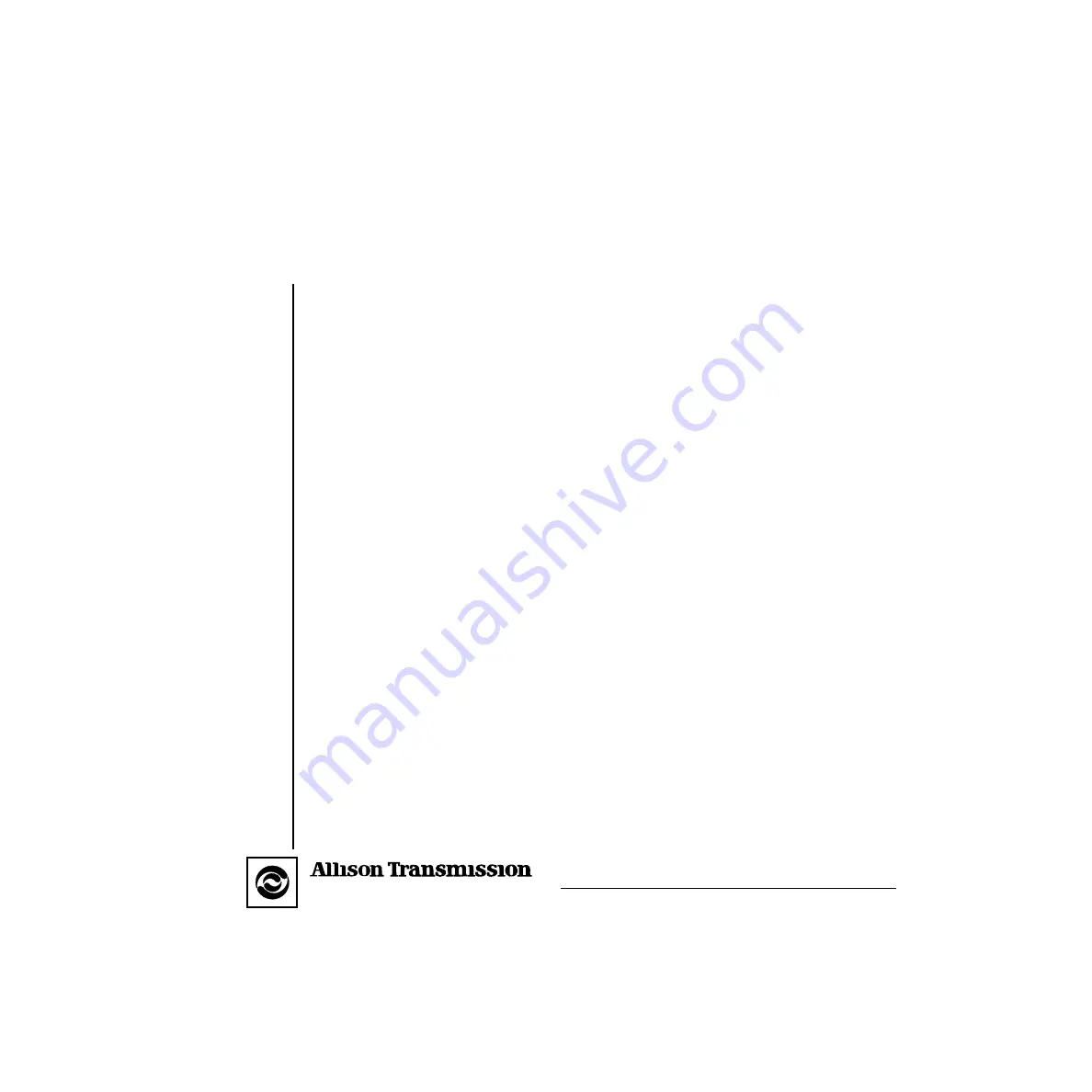
Printed in the U.S.A.
Copyright © 1996 General Motors Corp.
Service
Manual
Allison Transmission
SM1241EN
AUTOMATIC MODELS
AT 540,
AT 542(N)(R)(NFE),
AT 543,
AT 545(N)(R),
AT 1542P,
AT 1545P(N)
FEBRUARY 1996
Revision 1, 1999 April
Division of General Motors Corporation
P.O. Box 894 Indianapolis, Indiana 46206-0894