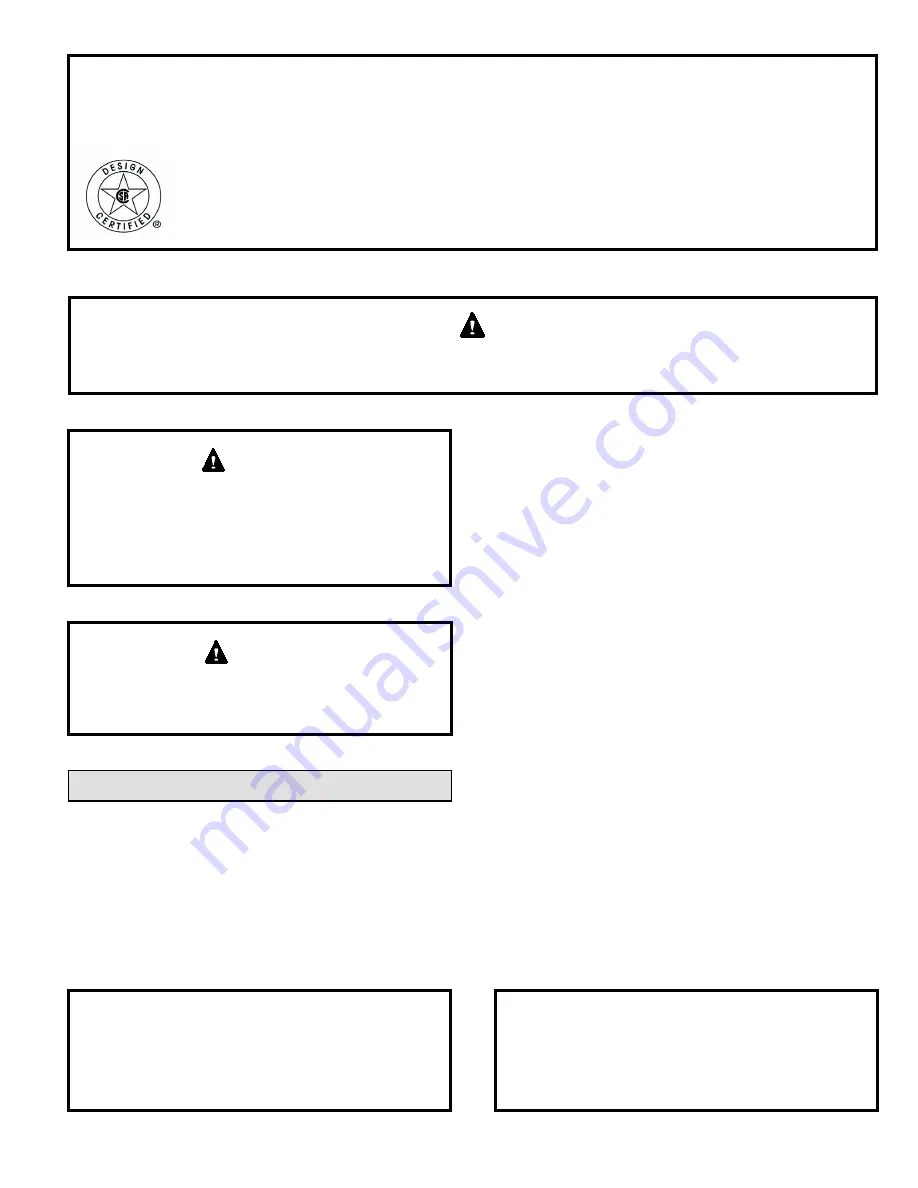
508144-01
Issue 2128
Page 1 of 42
INSTALLATION INSTRUCTIONS
A80UH2E & 80G2UHE(L)
Warm Air Gas Furnace
Upflow / Horizontal Left and Right Air Discharge
(P) 508144-01
*P508144-01*
Manufactured By
Allied Air Enterprises LLC
215 Metropolitan Drive
West Columbia, SC 29170
This manual must be left with the homeowner for future reference.
This is a safety alert symbol and should never be ignored. When you see this symbol on labels or in manuals, be alert to
the potential for personal injury or death.
Improper installation, adjustment, alteration, service
or maintenance can cause property damage, personal
injury or loss of life. Installation and service must be
performed by a licensed professional installer (or
equivalent), service agency or the gas supplier.
WARNING
As with any mechanical equipment, personal injury can
result from contact with sharp sheet metal edges. Be
careful when you handle this equipment.
CAUTION
Table of Contents
A80UH2E & 80G2UHE(L) Gas Furnace....................
Unit Dimensions ........................................................
Unit Dimensions ........................................................
Shipping and Packing List .........................................
Safety Information .....................................................
General ......................................................................
Combustion, Dilution & Ventilation Air .......................
Setting Equipment .....................................................
Filters ........................................................................
Duct System ............................................................
Venting.....................................................................
...............................................................
Electrical ..................................................................
Integrated Control DIP Switch Settings ...................
On-Board Links and Diagnostic Push Button ..........
Unit Start-Up ............................................................
Other Unit Adjustments............................................
Heating Sequence of Operation ..............................
Service.....................................................................
Repair Parts List ...................................................... 37
Blower Performance ................................................
A80UH2E & 80G2UHE(L) Gas Furnace
The A80UH2E & 80G2UHE(L) gas furnace is shipped ready
for installation in the upflow or horizontal right position (for
horizontal left position the combustion air pressure switch
must be moved). The furnace is shipped with the bottom
panel in place. The bottom panel must be removed if the
unit is to be installed in a horizontal application. The panel
may also be removed in upflow applications.