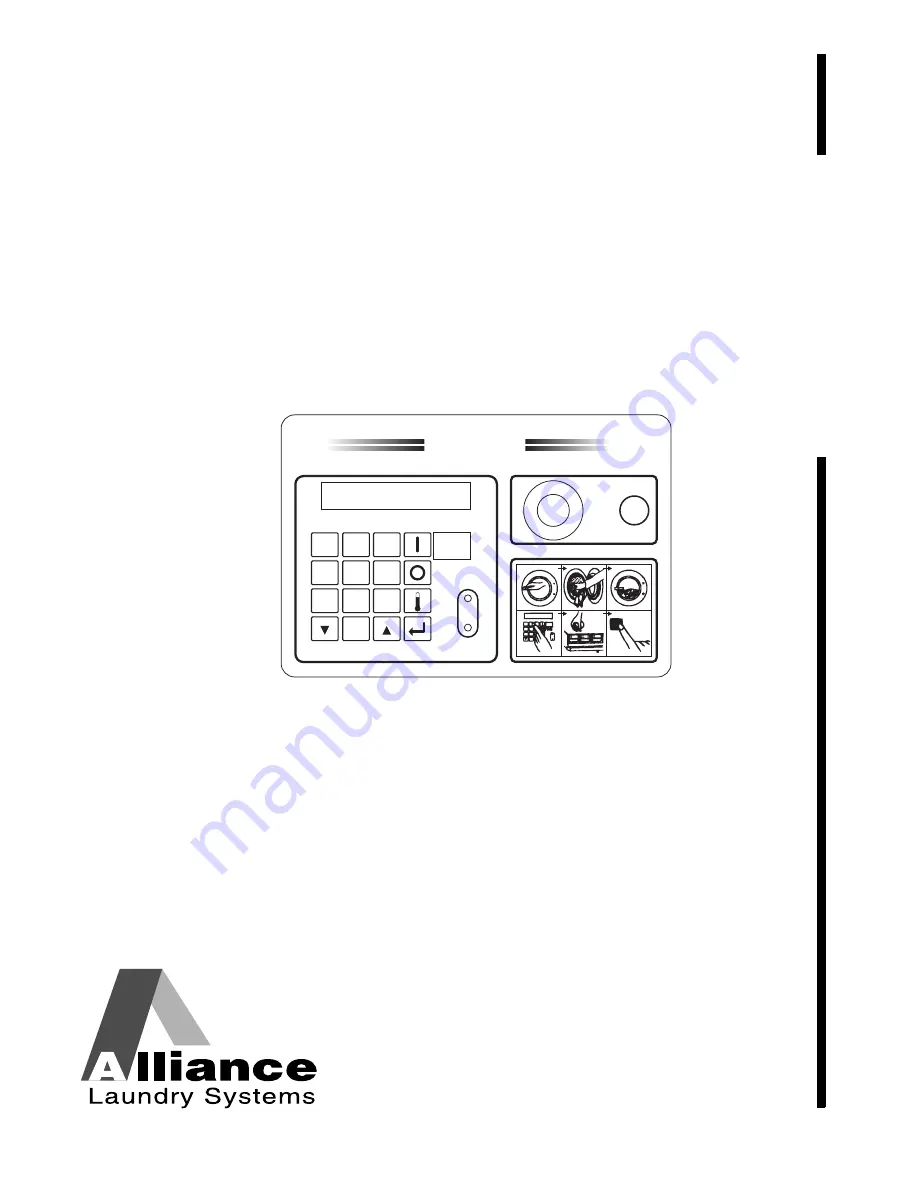
Pr
ogramming
www.alliancelaundry.com
Washer-Extractors
Pocket Hardmount Variable-Speed
PS40 Control
Refer to Page 9 for Model Identification
PHM1398C
1
2
3
4
5
6
7
8
9
0
PS40
PROG
RUN
PHM1398C
Part No. F8112301R3
August 2015
Keep These Instructions for Future Reference.
(If this machine changes ownership, this manual must accompany machine.)
www.groupdynamics-laundry.com