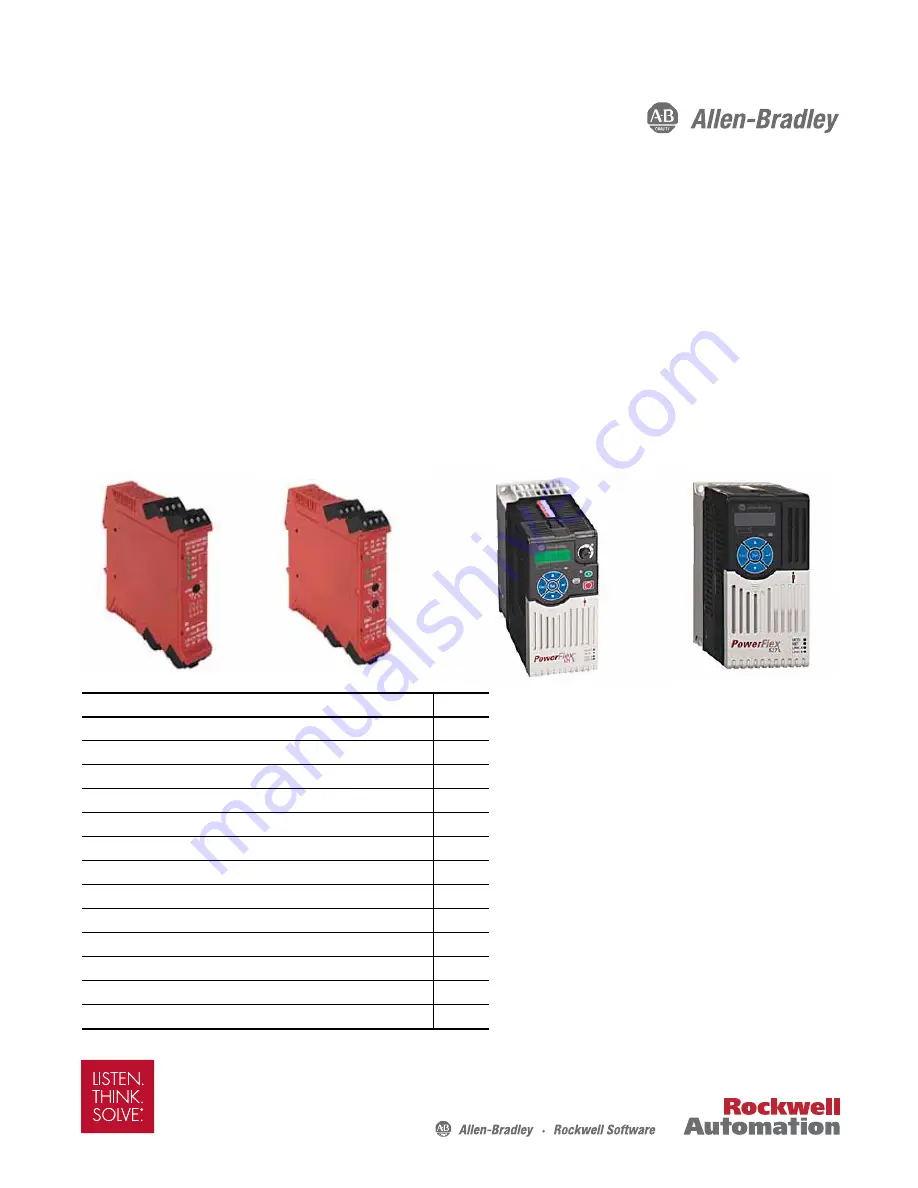
Application Technique
Safety Function: Actuator Subsystems – Stop Category 1 via
the PowerFlex 525 and PowerFlex 527 Drives with Safe
Torque-off
Products: Guardmaster Dual-input Safety Relay, Guardmaster Multifunction-delay Expansion Module, PowerFlex 525 Drive,
PowerFlex 527 Drive
Safety Rating: CAT. 3, PLd to ISO 13849-1: 2008
Topic
Page
Safety Function Realization: Risk Assessment
Calculation of the Performance Level