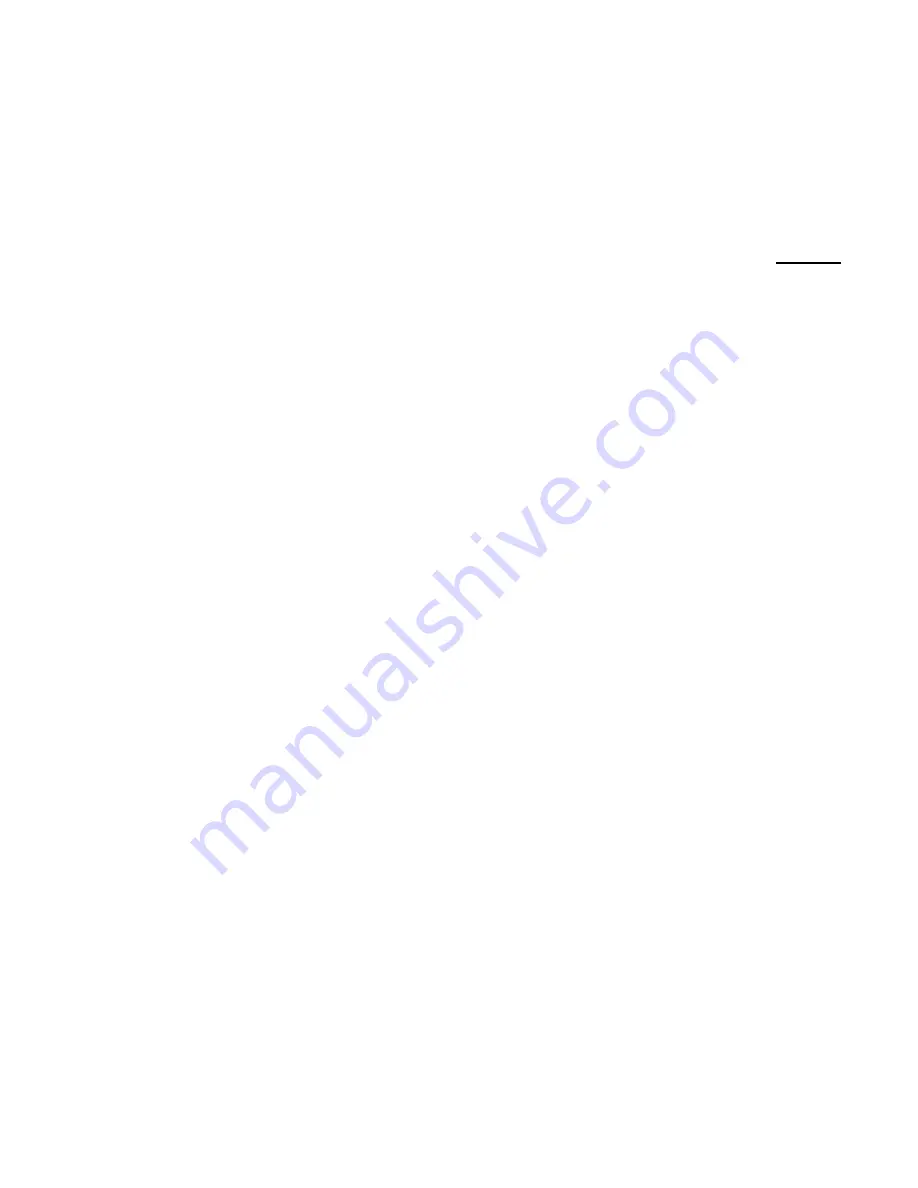
AIR TRACTOR, INC.
Olney, Texas
AT-502A/502B/504
TABLE OF CONTENTS
MAINTENANCE SECTION
Page No.
ENGINE MAINTENANCE ................................................................................................................. 01
Introduction .......................................................................................................................... 01
Maintenance ......................................................................................................................... 01
Cleaning Your Engine Exterior ............................................................................................. 01
Fuel
................................................................................................................................ 02
Figure 101 Fuel Nozzles ...................................................................................................... 03
Oil
................................................................................................................................ 03
Figure 102 Location of Oil Drain Plugs ................................................................................ 04
Air Filters .............................................................................................................................. 05
Miscellaneous ...................................................................................................................... 06
Compressor Washes............................................................................................................ 07
Figure 103 Gas Generator Case .......................................................................................... 07
Troubleshooting ................................................................................................................... 08
Starting Procedures ............................................................................................................. 08
Ground Run Procedures ...................................................................................................... 09
Routine Maintenance Inspection ........................................................................................ 010
INTRODUCTION ................................................................................................................................. 1
FUEL REQUIREMENTS ..................................................................................................................... 1
OIL REQUIREMENTS ........................................................................................................................ 1
Summary of Contents for AT-502A
Page 19: ...This Page Intentionally Left Blank...
Page 91: ...This Page Intentionally Left Blank...
Page 92: ......
Page 93: ......
Page 94: ......
Page 95: ......
Page 96: ......
Page 97: ......
Page 98: ......
Page 99: ......
Page 100: ......
Page 101: ......
Page 102: ......
Page 103: ......
Page 104: ......
Page 105: ......
Page 106: ......
Page 107: ......
Page 108: ......
Page 109: ......
Page 110: ......
Page 111: ......
Page 112: ......
Page 113: ......
Page 114: ......
Page 115: ......
Page 116: ......
Page 117: ......
Page 118: ......
Page 119: ......
Page 120: ......
Page 121: ......
Page 122: ......
Page 123: ......
Page 124: ......
Page 125: ......
Page 126: ......
Page 127: ......
Page 128: ......
Page 129: ......
Page 130: ......
Page 131: ......
Page 132: ......
Page 133: ......
Page 134: ......
Page 135: ......
Page 136: ......
Page 137: ......
Page 138: ......
Page 139: ......
Page 140: ......
Page 141: ......
Page 142: ......
Page 143: ......
Page 144: ......
Page 145: ......
Page 146: ......
Page 147: ......
Page 148: ......
Page 149: ......
Page 150: ......
Page 151: ......
Page 152: ......
Page 153: ......
Page 154: ......
Page 155: ......
Page 156: ......
Page 157: ......
Page 158: ......
Page 159: ......