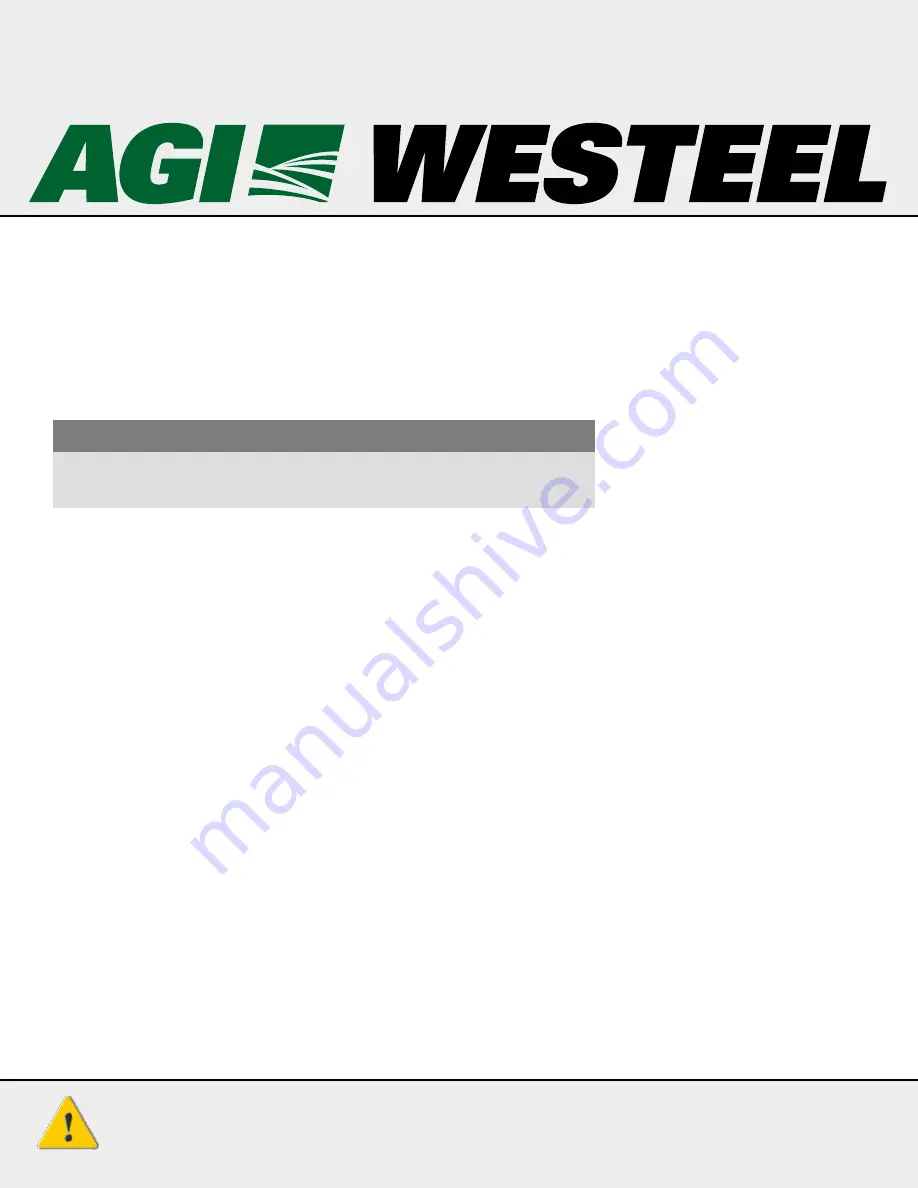
Read this manual before using product. Failure to
follow instructions and safety precautions can
result in serious injury, death, or property
damage. Keep manual for future reference.
Part Number: BU-0101704 R3
Revised: June 2021
Original Instructions
EasyFlow2 (100 Series)
Farm Tube Bin Unload System
Assembly & Installation Manual
This manual applies to:
8” Tube Unload
Bin Diameters: 24’, 27’, 30’, 33’, 36’,
39’, 42’, 45’, 48’, 54’, 60’
10” Tube Unload