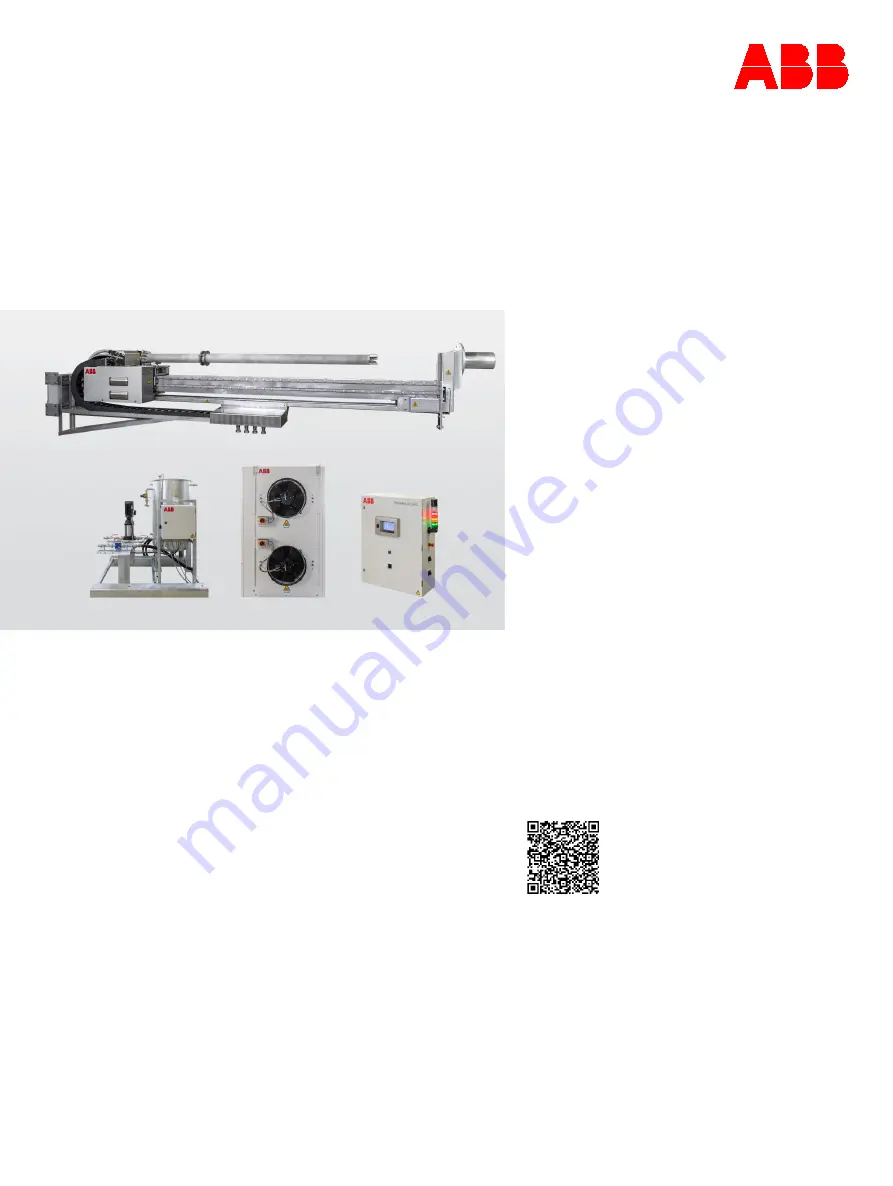
—
A BB MEA SU RE ME NT & ANA L YT ICS | O PE RATI N G I NS T RUCT IO N | OI/ GAC4 00- EN RE V. A
ProKiln GAC400
Probe gas sampling system
—
ABB Measurement & Analytics
For your local ABB contact, visit:
www.abb.com/contacts
For more product information, visit:
www.abb.com/analytical
Sampling system for dry gas
sampling at rotary cement kiln gas
exit and calciner gas exit.
Measurement made easy
O
I/
G
A
C4
0
0
-EN
R
ev
. A
0
9.
20
23
O
rig
in
al
In
st
ru
ct
io
n
—
ProKiln GAC400
Introduction
The ProKiln sampling system is especially
designed for analysis in hot cement flue gases
with high content of dust and aggressive gas
components. The system is made by cement
specialists for use in the rough environment of a
cement plant.
The ProKiln sampling system is preferably
combined with ABB’s AO2000 System. However,
the ProKiln sampling system is built to be self-
supporting which allows it to easily be connected
and retrofitted to any existing well-functioning
gas analysis system or other third-part suppliers
solution.
The system controller interface offers a large
variety of industry leading communication
options together with conventional terminal
based digital and analogue status signals.
Additional Information
Additional documentation on ProKiln GAC400 is
available for download free of charge at
www.abb.com/analytical.
Alternatively simply scan this code:
—
We reserve the right to make technical changes or modify the contents of this
document without prior notice. With regard to purchase orders, the agreed particulars
shall prevail.
ABB does not accept any responsibility whatsoever for potential errors or possible lack
of information in this document.
We reserve all rights in this document and in the subject matter and illustrations
contained therein. Any reproduction, disclosure to third parties or utilization of its
contents – in whole or in parts – is forbidden without prior written consent of ABB.
© ABB 2023
3KXG174400R4201