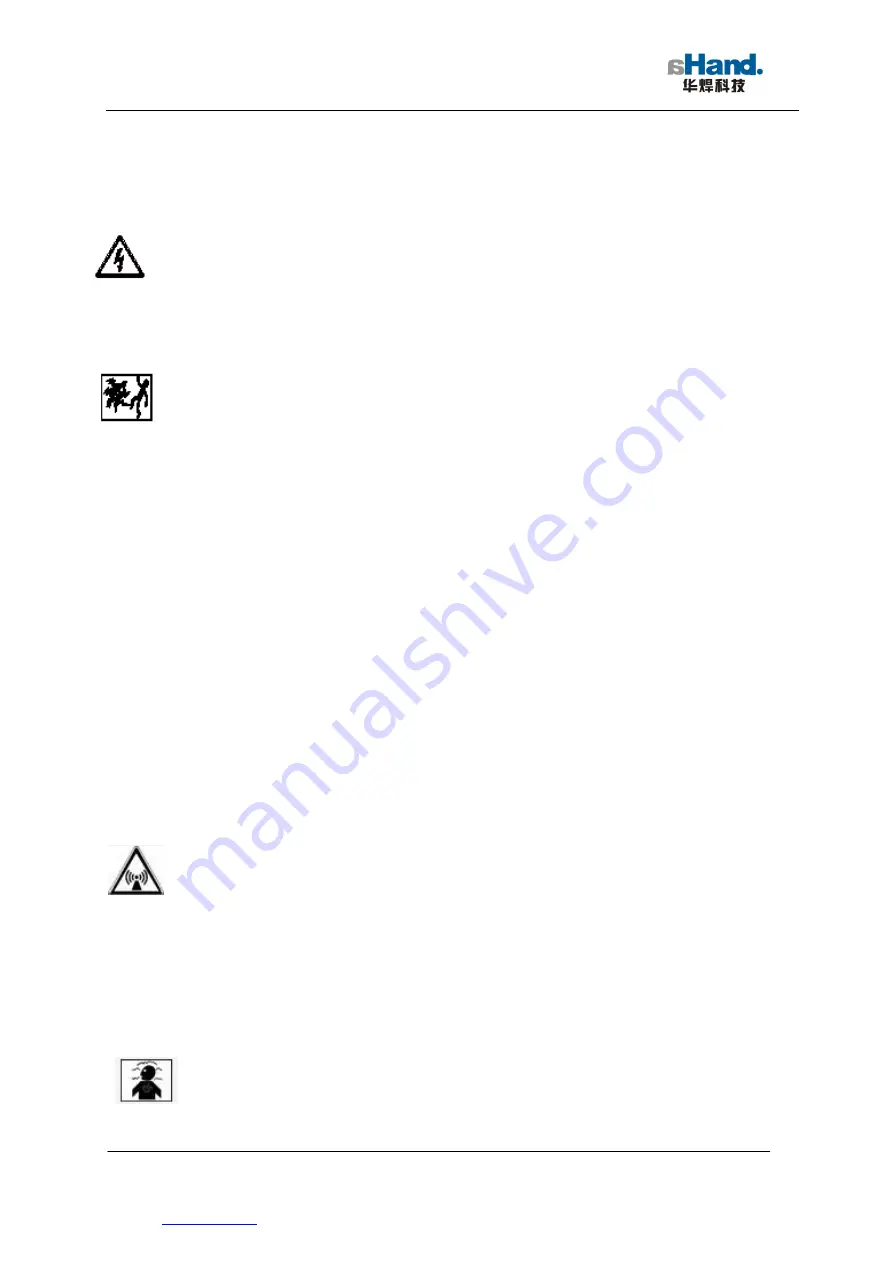
Suzhou A-hand Technology Co., Ltd. (215021)
Instruction
Address: No. 88, Tangzhuang Road, Suzhou Industrial Park, China
NO.
1
Tel: +86-512-6252-9140
http://
www.a-hand.com
Safety Precautions
Warning: For your safety:
Arc welding dangerous
In order to avoid unnecessary casualties, please protect your and other people's safety, children
should be away from the welding site, the operator must wear protective clothing and glasses!
Electric shock will hurt you
Before using the device, the power supply and water containers must be reliably grounded
!
In the process of welding, the temperature of electrode and workpiece is very high, please do not let
your skin and damp cloth touch these hot parts, in order to prevent your hands from being injured,
please put on dry gloves for construction!
Use dry insulating materials so that you and your workpieces can be isolated, and the insulating
material should have sufficient surface!
In the process of automatic welding, the temperature of the electrodes, welding head, nozzle and
torch is respectively quite high!
Ensure that the working cable is well connected to the welded parts, and it should be close to
welding joints of the workpiece!
The workpiece and the welded metal need to be grounded well.
In the safe operation mode, please check whether the electrode, ground clamp, welding
cable and welding machine are intact, replace the damaged components!
The electrode can not be cooled by water!
Do not touch the conductive parts connected to the two welding electrodes at the same time!
Arc rays may cause injury on the human body
When it comes to welding, please wear the safety goggles to avoid hurt caused by sparks and arc
rays!
Please wear protective clothing made of flame-retardant materials to ensure that your skin is kept
away from arc radiation damage!
Smoke is harmful to health!