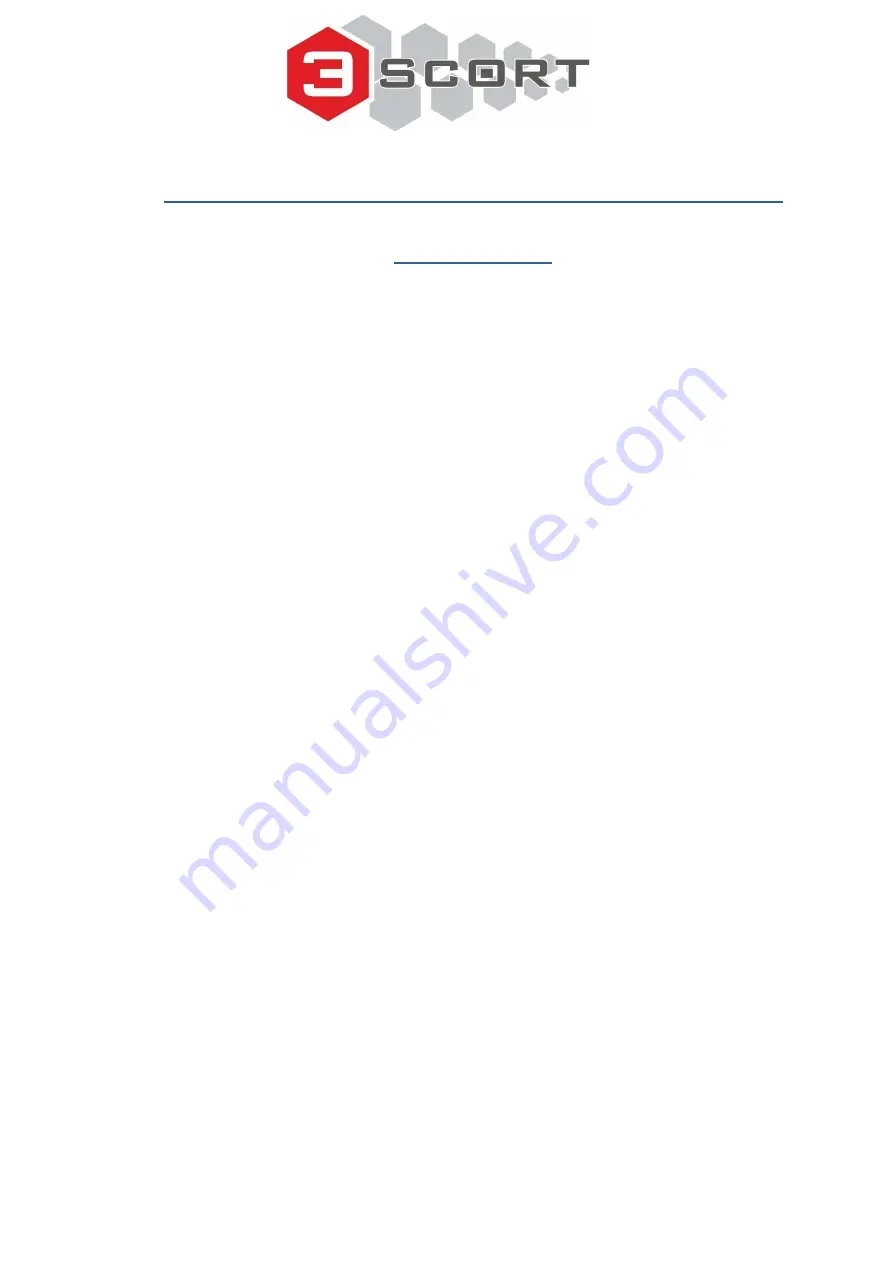
TD-150 and TD-500 Installation and Configuration
User Manual
Contents
TD-150 and TD-500 Installation and Configuration
Definition and purpose of the sensor
Sensor configuration and fine-tuning
2. Setting the “Empty” calibration value
Sensor installation. Tank calibration
Connecting sensor to GPS tracker
Checking connection between sensor and tracker via Rs485.
Common issues and how to resolve them
Setting Full and Empty calibration manually
Using the same tank calibration table for different sensors
1