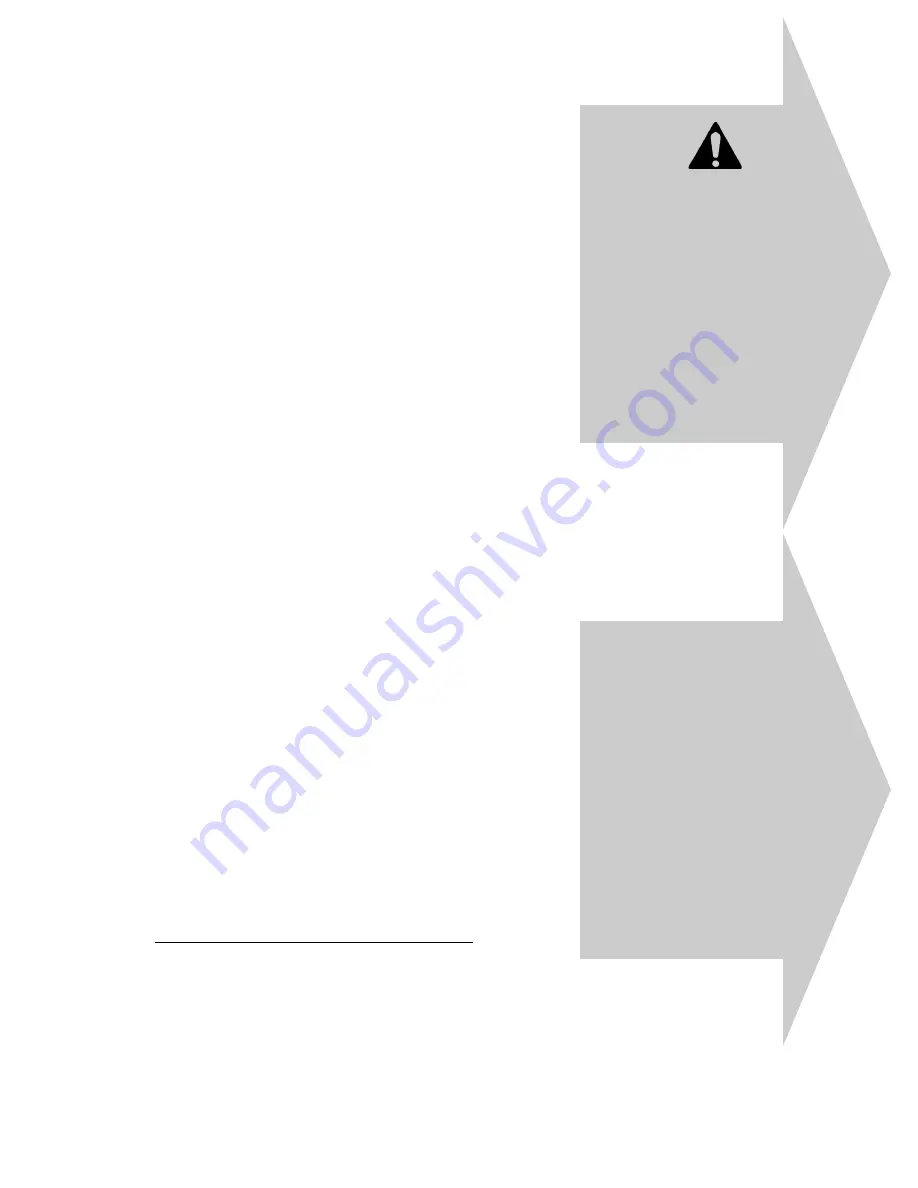
Instructions and Parts List
Serial No.
For reference, record machine serial number here.
Important
Safeguards
Spare Parts
700rks
Type 29800
Adjustable
Case Sealer
with
Taping Heads
"3M-Matic" and "AccuGlide" are Trademarks
of 3M, St. Paul, MN 55144-1000
Printed in U.S.A.
© 3M 2000 44-0009-1927-2(A)
3M Packaging Systems Division
3M Center, Building 220-8W-01
St. Paul, MN 55144-1000
Read "Important Safeguards",
pages 3-6 and also operating
"Warnings", page 18
BEFORE INSTALLING
OR OPERATING THIS
EQUIPMENT.
It is recommended you
immediately order the
spare parts listed on
page 39. These parts
are expected to wear
through normal use
and should be kept on
hand to minimize
production delays.
3
3M-Matic
KEEP THESE INSTRUCTIONS NEAR THIS
EQUIPMENT FOR FUTURE REFERENCE.
AccuGlide
II
Summary of Contents for 3M-Matic 700rks
Page 9: ...4 Figure 1 2 Replacement Labels 3M Part Numbers Important Safeguards Continued...
Page 10: ...5 Important Safeguards Continued Figure 1 3 Replacement Labels 3M Part Numbers...
Page 27: ...22 THIS PAGE IS BLANK...
Page 33: ...28 THIS PAGE IS BLANK...
Page 39: ...34 THIS PAGE IS BLANK...
Page 47: ...42 THIS PAGE IS BLANK...
Page 48: ...43 700rks Adjustable Case Sealer Frame Assemblies...
Page 49: ...44 700rks Adjustable Case Sealer Figure 3894...
Page 51: ...46 700rks Adjustable Case Sealer Figure 3895 1 of 2...
Page 53: ...48 700rks Adjustable Case Sealer Figure 3895 2 of 2...
Page 55: ...50 700rks Adjustable Case Sealer Figure 4046...
Page 57: ...52 700rks Adjustable Case Sealer Figure 7356...
Page 59: ...54 700rks Adjustable Case Sealer Figure 7357 1 of 2...
Page 61: ...56 700rks Adjustable Case Sealer Figure 7357 2 of 2...
Page 63: ...58 700rks Adjustable Case Sealer Figure 7358...
Page 65: ...60 700rks Adjustable Case Sealer Figure 7359 1 of 2...
Page 67: ...62 700rks Adjustable Case Sealer Figure 7359 2 of 2...
Page 69: ...64 700rks Adjustable Case Sealer Figure 7360...