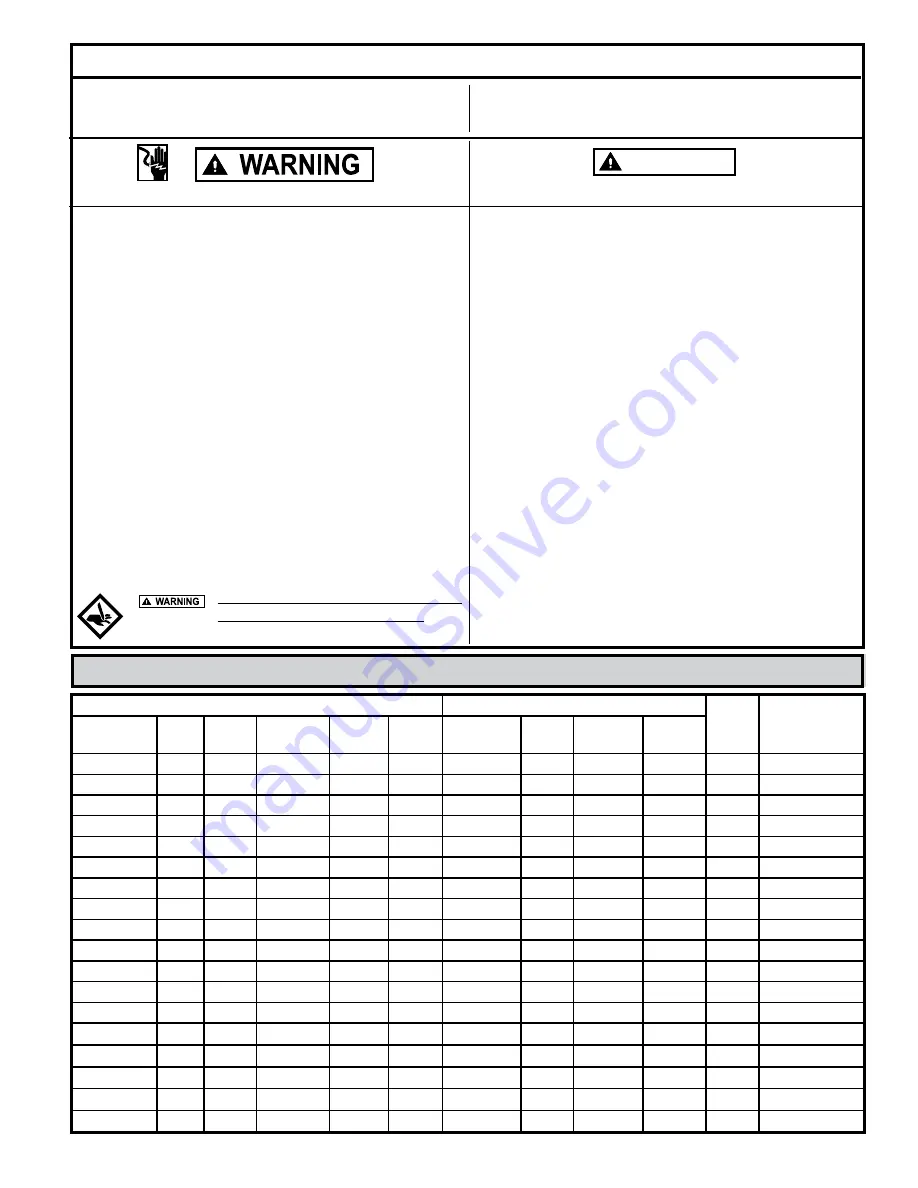
3
© Copyright 2018 Zoeller
®
Co. All rights reserved.
Preinstallation Checklist
SEE BELOW FOR LIST OF WARNINGS
CAUTION
SEE BELOW FOR LIST OF CAUTIONS
1.
Inspect your grinder pump.
If the unit has been damaged in
shipment, contact your dealer before installing.
Do Not
remove the
test plug in the cover nor the motor housing.
2.
Carefully read all literature
to familiarize yourself with details
regarding installation and use. Retain materials for future reference.
1.
Make sure pump connection contains a ground terminal.
The
power cord on all Zoeller Grinder Pumps contains a green conductor
for grounding to help protect you against the possibility of electric
shock.
2.
Make certain the electrical service is within reach of the power
supply cord
.
3.
Make sure any panels and branch circuits are equipped
with
proper size fuses and circuit breakers. An independent power circuit
is recommended, sized according to the National Electrical Code, for
the current shown on the grinder pump nameplate.
4.
For your protection, always disconnect the power source to the
grinder pump before handling.
All grinder pumps must be properly
grounded and wired in accordance with the “National Electrical Codes”
and all local codes and ordinances.
5. Installation of electrical hardware and checking of control panels
and circuits should be performed by a qualified licensed electrician.
6. Risk of electrical shock - These pumps have not been investigated
for use in swimming pool areas.
7. Prop65 Warning for California residents:Cancer and reproductive
Harm- www.P65Warnings.ca.gov.
1.
Make sure the power source
is capable of handling the electrical
requirements of the grinder pump, as indicated on the nameplate.
2.
A disconnect switch should be installed ahead of the pump.
3. The Grinder pumps are operated by control panels with variable level
float control switches. It is the responsibility of the installing party to
see that float control switches will not hang up on the grinder pump
or other pit peculiarities and are secured so that the grinder pump
will shut off. It is recommended to use rigid pipe and fittings and
the pit be 24" in diameter for simplex systems and 36" in diameter
for duplex systems or larger.
4. Grinder installations should be checked yearly for debris and/or build
up which may interfere with the “ON” or “OFF” positions of variable
level float control switches. Repair and service, other than cutter
assembly maintenance, should be performed by Zoeller Engineered
Products authorized service stations only.
5. Maximum operating temperature must not exceed 130 °F,
(54 °C).
6.
Pump and float switch electrical connections must be
permanently installed, operational and protected from
submergence.
7.
Junction box conduit must be installed with watertight
connection. Zoeller junction boxes include a UL Listed potting
kit for sealing the conduit. Failure to properly install this sealant
material could void warranty.
Electrical Data
Amps
KVA
Code
Winding
Resistance
Line-to-Line
Model
BHP
RPM
Voltage
Phase
Hertz
Full Load In Air Shut Off Locked
Rotor
I7011
2
3450
200
1
60
20.0
6.6
12.1
60
H
1.0 / 1.5
E7011
2
3450
230
1
60
17.2
4.0
10.9
56
F
1.3 / 4.0
J7011
2
3450
200
3
60
12.3
3.7
7.7
54
L
1.9
F7011
2
3450
230
3
60
10.8
3.3
6.9
42
K
2.4
G7011
2
3450
460
3
60
5.5
1.6
3.5
21
K
9.7
BA7011
2
3450
575
3
60
4.5
1.0
2.5
11
F
15.3
I7012
2
3450
200
1
60
20.0
6.6
12.1
60
H
1.0 / 1.5
E7012
2
3450
230
1
60
17.2
4.0
10.9
56
F
1.3 / 4.0
J7012
2
3450
200
3
60
12.3
3.7
7.7
54
L
1.9
F7012
2
3450
230
3
60
10.8
3.3
6.9
42
K
2.4
G7012
2
3450
460
3
60
5.5
1.6
3.5
21
K
9.7
BA7012
2
3450
575
3
60
4.5
1.0
2.5
11
F
15.3
I7013
2
3450
200
1
60
20.0
6.6
12.1
60
H
1.0 / 1.5
E7013
2
3450
230
1
60
17.2
4.0
10.9
56
F
1.3 / 4.0
J7013
2
3450
200
2
60
12.3
3.7
7.7
54
L
1.9
F7013
2
3450
230
2
60
10.8
3.3
6.9
42
K
2.4
G7013
2
3450
460
2
60
5.5
1.6
3.5
21
K
9.7
BA7013
2
3450
575
2
60
4.5
1.0
2.5
11
F
15.3
Do not attempt to turn star cutter located
on bottom of the unit with fingers. Use a
wrench when checking or removing star cutter.