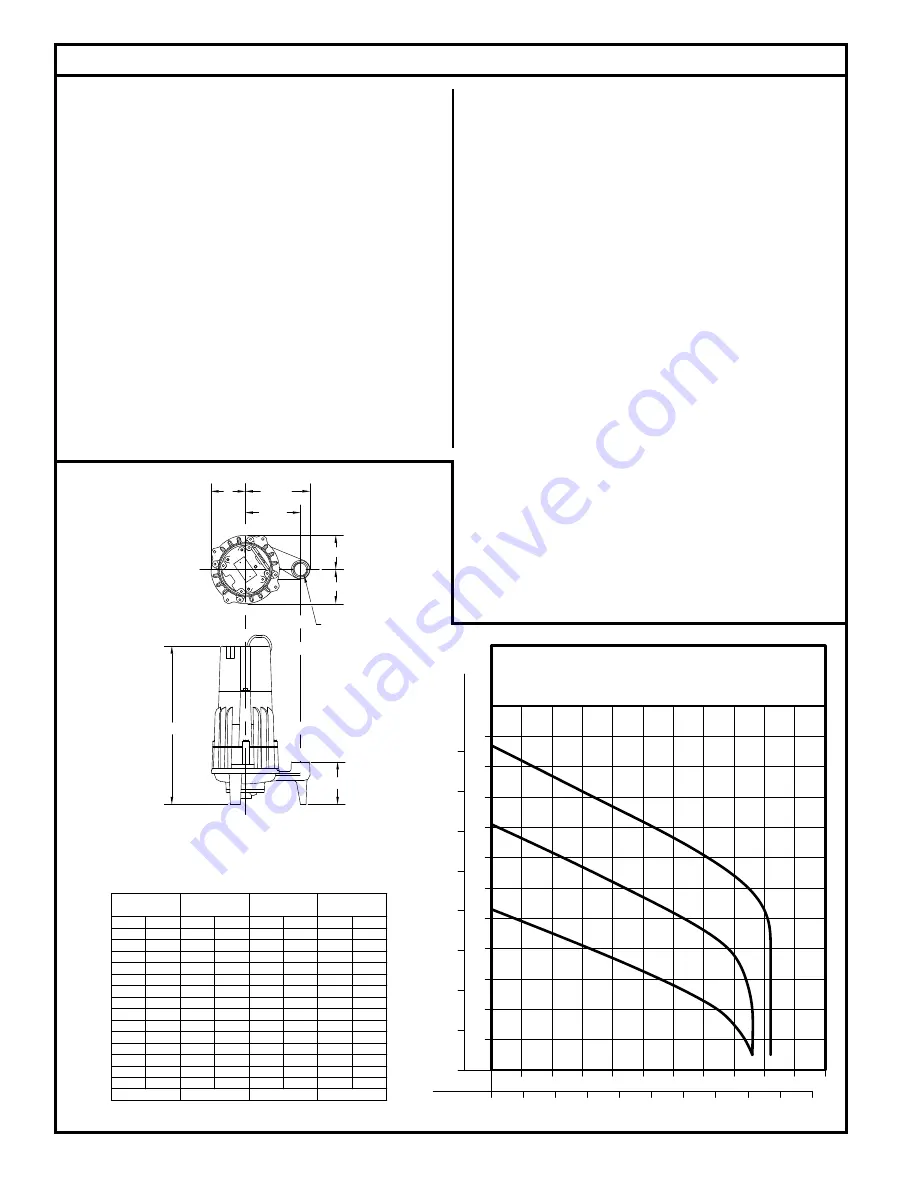
4
© Copyright 2017 Zoeller
®
Co. All rights reserved.
1-1/4" N.P.T.
18-5/8" [473 mm]
5" [127 mm]
6-1/2"
[165 mm]
4" [102 mm]
4" [102 mm]
7-5/8"
[194 mm]
4"
[102 mm]
General Information
GRINDER PUMP DESCRIPTION
1. Pumps are constructed of class 30 cast iron with powder
coated epoxy protection for long life when pumping sew-
age in submersible applications. The cutter assembly is
comprised of 440 C stainless steel components hardened
to a value of 55-60 on the Rockwell C scale; a cutter and
a precision ground flat disk. Cutting action takes place
with the rotation of the cutter in the clockwise (looking
down on the unit) direction only, see Fig. 6 on page 11.
2. Pump motors are single phase design. Single phase
motors require a starting relay, starting capacitor and
a run capacitor. These items are located in the switch
case on the pump.
3. These grinder pumps have a single seal design and do
not have sensor wires.
4. Automatic reset thermal overload protection is integral on
single phase motors. For three phase models, overload
protection is to be provided in the control panel.
FIELD ASSEMBLED INSTALLATION
1. Installation and piping instructions are included with
the rail system and basin instructions. If pump is being
retrofitted to an existing rail system, accessory parts
may be required. Consult the factory and advise make
and model of rail system being used.
2. Refer to the appropriate Indoor/Outdoor prepackaged
instructions on pages 6-9 for more information on
system installation.
3. All electrical connections including pump to control
box and power supply to control panels must comply
with the “National Electrical Code” and applicable local
codes. Conduit and panel enclosure openings must
have a gas and watertight seal. Installation of electrical
panels, conduit and connections should be made by a
qualified licensed electrician. A UL Listed potting kit,
P/N 10-2350, is available from Zoeller Company.
4. When installing a pump with a check valve, or a rail
system with a check valve, you must give the pump
case time to fill to help prevent air lock when lowering
the unit into the liquid. The pump case has an air vent
located behind the discharge. This air vent is across the
pump housing mounting surface and must be cleaned
before each reinstall. An extra air vent hole (3/16") may
be drilled in discharge pipe below the check valve to
help prevent air lock. This drilled hole must be cleaned
before each reinstall. After the pump is installed, run
the unit submerged to assure the pump case is filled
(Water should come out of 3/16" diameter hole).
SK1621
FIGURE 1.
154108
154108
TOTAL DYNAMIC HEAD/FLOW
PER MINUTE
SEWAGE AND DEWATERING
Shut-off Head:
90
100
80
70
53 ft. (16.2m)
27.4
30.5
24.4
21.3
-
-
-
-
MODEL
60
50
40
30
20
10
5
Feet
-
-
16.5
28
37
42
15.2
18.3
12.2
6.1
9.1
3.0
-
-
62
140
106
159
43
Gal.
1.5
Meters
820
Liters
163
-
-
12
81 ft. (24.7m)
-
-
-
-
45
22
32
39
42
43
43
121
83
148
159
43
Gal.
819
Liters
Gal.
818
Liters
-
-
-
-
16.7
27
36
107 ft. (32.6m)
7
63
26
102
136
43
46
46
46
46
46
174
163
174
174
174
174
46
174
15
40
35
41
25
33
43
4.6
7.6
10.7
163
163
163
151
125
83
22
163
155
43
163
46
174
46
174
46
174
20
30
40
50
60
10
15
20
25
30
35
40
45
50
55
5
20
40
60
80
100
120
140
160
180
200
0
METERS
FEET
PUMP PERFORMANCE CURVE
MODELS 818/819/820
0
TOT
AL
DYNAMIC HEAD
FLOW PER MINUTE
U.S. GALLONS
LITERS
70
10
80
90
100
110
4
8
12
16
20
24
28
32
820
819
818