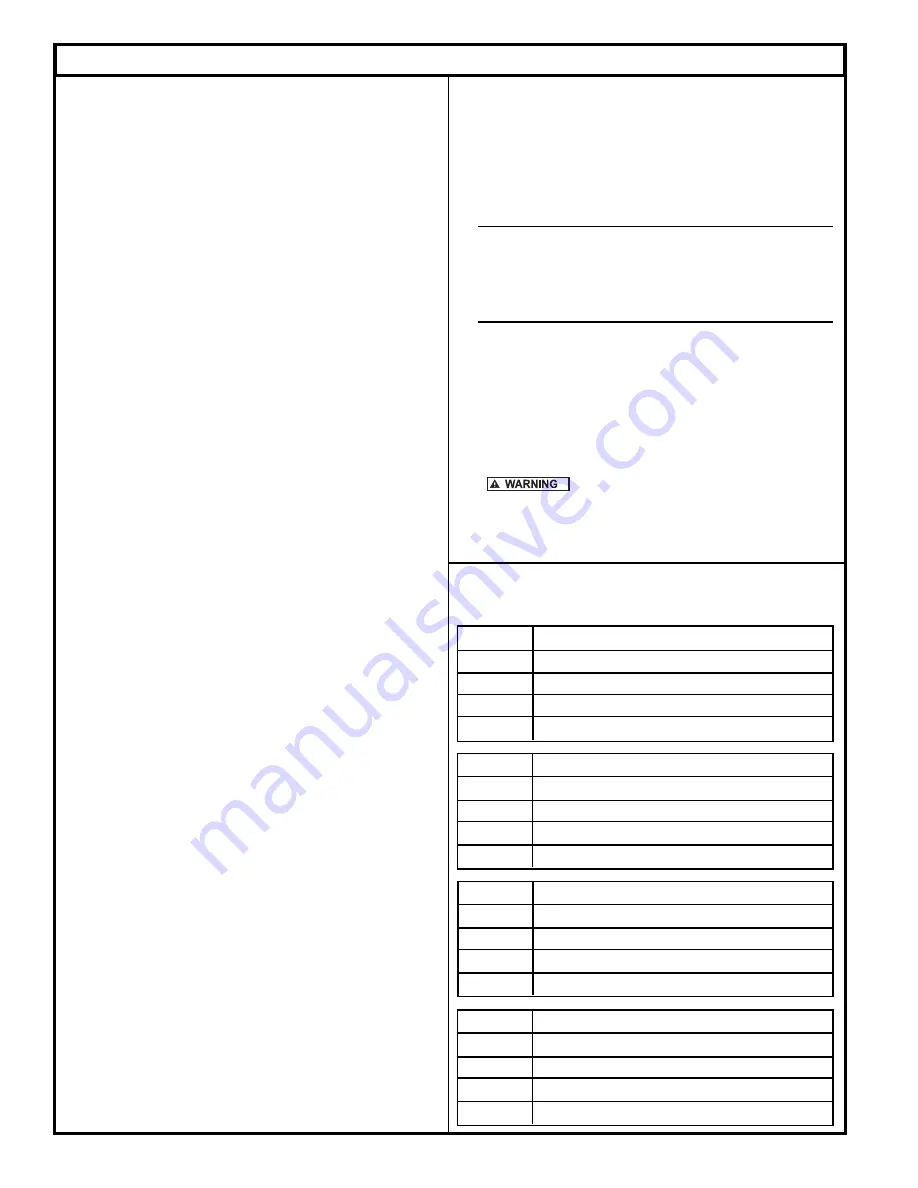
6
3. Apply 80-90 weight gear oil to the shaft and to the inside
diameter of the rotating section of rotary seal (20). Push the
rotating section onto the shaft in a continuous motion until the
seal faces meet.
4. Install the spring and spring holder over the shaft and seat
against the rotating section. Compress the spring as necessary
and install retaining ring (21) in the groove of the motor shaft.
5. Lightly oil and install seal ring (18) on the seal retainer (23).
6. Press the seal retainer (23) into the adapter (19) and secure
with the four socket head screws (22).
7. Install the seal seat and rotating section of the lower rotary seal
assembly (24) into the seal retainer (23) in the same manner
described in steps 2 and 3 above.
E. Installing the impeller...
1. Install the spring of the lower rotary seal (24) on the exposed
end of the rotor/shaft.
NOTE: Spring holder not required on lower rotary seal.
.2. Install the proper number of impeller shims (25) on the shaft
give the face of the impeller (26) a clearance of 0.015 to
0.030 inch with the wearing face of the pump housing (31).
(See impeller clearance diagram.)
3. Install the square key (15) in the groove in the shaft.
4. Install the impeller (26), impeller washer (27), lock washer (28).
Secure the impeller (26) by immobilizing it, use a pipe wrench
to grip the vanes and install the impeller bolt (29) in the end of
the shaft.
NOTE: Apply thread locking compound to impeller bolt (29) before
installing and torque bolt to 230-240 inch pounds.
5. Lightly oil and install the seal ring (30) on the adapter (19) and
install the adapter on the pump housing, securing it with the
four screws (2) and lock washers (3).
Leak Test
Before oiling pump perform a leak test on the pump seals by install-
ing a regulated air supply into the holes (¼” NPT access) the motor
chamber, seal chamber and cover chamber must be checked. The
pressure of the air supply should be set at approximately 9 psi. Sub-
merge the pump in clear water watching for small air bubbles around
square ring seals, rotary seal, cord connection, and oil fi ll plugs.
NOTE: Make certain that the pump is placed in the water so that
no areas are present that would trap air (such as the cavity around
the lower rotary seal), not allowing the bubbles to rise to the water
surface.
If it is not possible to leak test the pump using the submersion
method, a regulated air supply with a (0-15 psi) air gage can be
installed in the fi ll holes. The pump to be pressurized and held at 9
psi. After removing the air supply, the pressure should not drop more
than ½ psi in a 24 hour period.
Assembly Procedures (continued)
© Copyright 2010 Zoeller Co. All rights reserved.
START KITS AND COMPONENTS
FOR SINGLE PHASE 600 SERIES
F. Oiling and fi nal assembly.
1. After leak testing has been completed, clean pipe plugs and
reapply pipe dope or tefl on tape. Install pipe plug (1) in cover (4).
2. With the pump laying on its side, with the oil fi ll hole up, and fi ll
the seal chamber cavity with an anti-wear non-detergent, rust
inhibiting, paraffi ning oil of approximately 100 SUS. (See table
below for acceptable type of oil.)
Refi ner
Product Name
Arco
Duro 22 or 32
Exxon
Teresstic 22 or 32 or acceptable equal
Chevron
Clarity Hydrolic Aw ISO22 or ISO32
3. Clean pipe plugs and reapply pipe dope or tefl on tape. Install
pipeplug (1) in adapter (19).
4. While pump is on its side place approximately one quart of oil in
motor housing. (Use the same oil as used in the seal cavity.)
5. Set the pump upright and fi nish fi lling the motor chamber with
oil until it runs back out the fi ll hole. With the oil running out the
fi ll hole the oil will be at the proper level for the top bearing.
Do not over fi ll.
6. Clean pipe plug and reapply pipe dope or tefl on tape. Install
pipe plug (1) in motor housing (12).
PART #
DESCRIPTION (BEFORE 10/1/07)
10-0914
KIT, START MODELS 611 / 621
015030
CAPACITOR, 40UF / 370 VAC
007453
RELAY, UNIVERSAL SUPCO
007597
CAPACITOR, 324-389UF / 110-125V
PART #
DESCRIPTION (AFTER 10/1/07)
10-2221
KIT, START MODELS 611 / 621
015030
CAPACITOR, 40UF / 370 VAC
018967
RELAY, GE 3ARR3J4A2
008190
CAPACITOR, 216-259UF / 110-125V
PART#
DESCRIPTION
10-0915
KIT, START MODELS 631 / 641
012869
CAPACITOR, 50UF / 370 VAC
015156
RELAY, GE 3ARR22J6C22
012870
CAPACITOR, 270-324UF / 220-250V
PART #
DESCRIPTION
10-1434
KIT, START MODELS 651
012869
CAPACITOR, 50UF / 370 VAC
015154
RELAY, GE 3ARR22J9R2
012870
CAPACITOR, 270-324UF / 220-250V