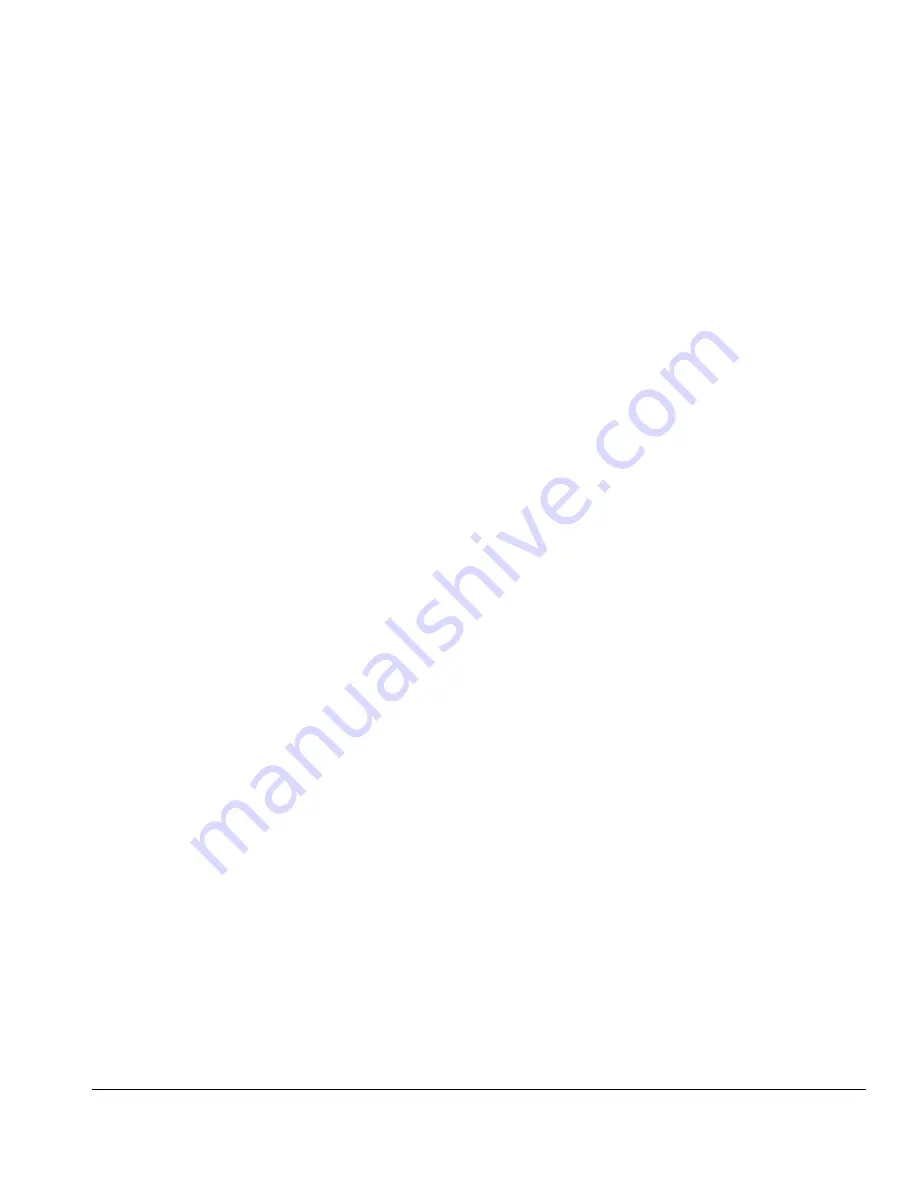
S L R M I S S I L E
6
Before we can start building, we need to do some prep work. Good prep work will pay off later
with a straight, true running boat.
First, we need a flat work surface. Nothing else will do.
The entire boat will be built on this, so make sure it is right.
We are ready to start the build!
Let’s identify the parts in the sheets. Don’t remove the parts until you actually need them, as
some look similar, but are not the same. This boat is not symmetrical.
The right and left are not
the same
, so it is critical that you note the parts correctly, or they will not fit. Note that all
reference to right or left are as if you were sitting in the boat.
All parts are marked with either a laser etch or two holes. Two holes ALWAYS indicate right
side.
A note about glue:
We use and recommend Titebond III wood glue for most of the construction.
This is available at Home Depot or Lowes.
For any raw wood to wood joint, we prefer Titebond III.
For any joint that is not wood, or wood that has been sealed, we recommend 30 minute epoxy.
The decks should always be glued with 30 minute epoxy, as they will already have been sealed
with two coats of epoxy.
You can also build the entire boat with 30 minute epoxy if you wish.
Summary of Contents for SLR Missile Thunderboat
Page 48: ...S L R M I S S I L E 48...