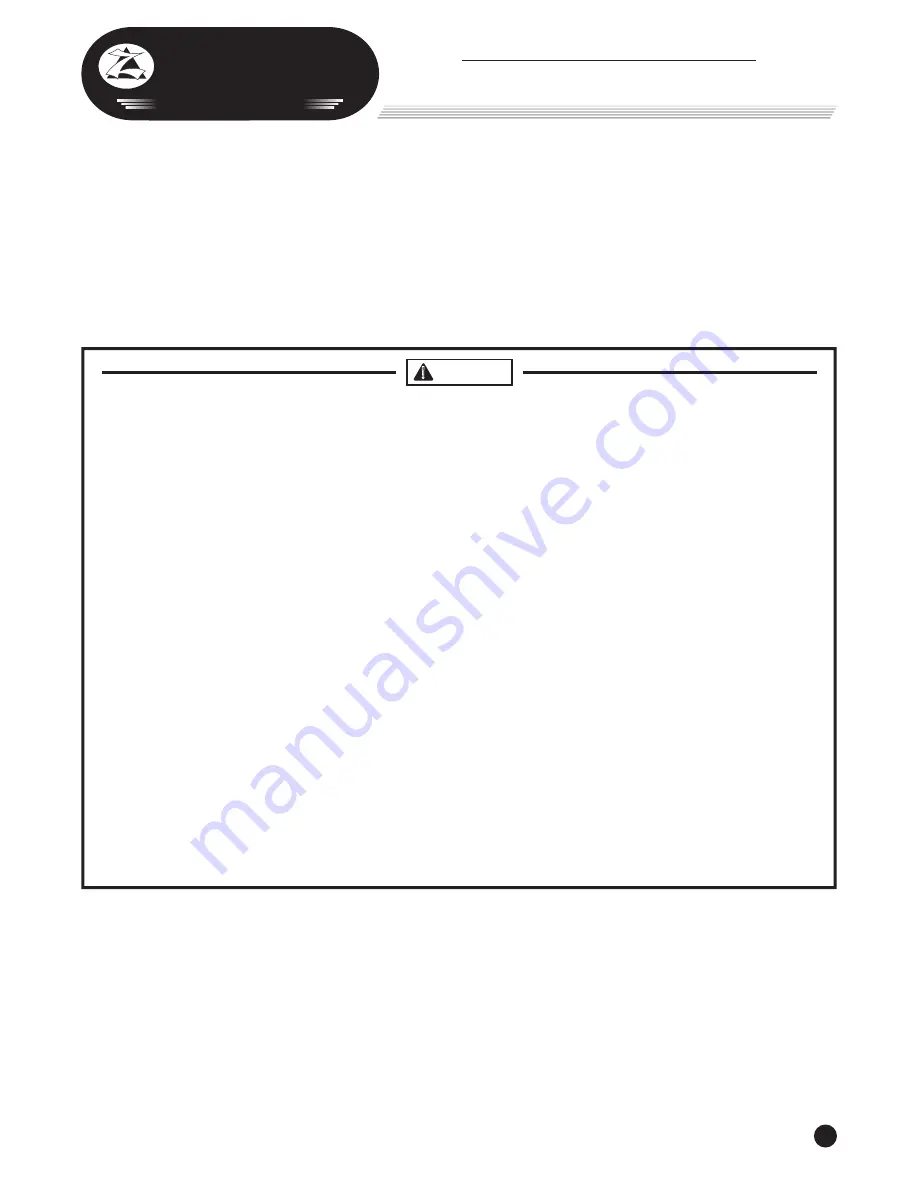
1
Preparations & Setup
Air Supply Hook-up
Remove the thread protector from the air inlet of the pump. Select and install the threaded fittings which are compatible
with your air supply fittings. The air supply should be 20 CFM (.57 M3/mm.) and 100 psi (7 bar) at the pump to obtain
the rated hydraulic pressure. Air pressure should be regulated to a maximum of 140 psi (9 bar). Secure your pump fitting
to the air supply.
If improperly used, pressurized equipment can be potentially hazardous. Therefore:
1. Hydraulic connections must be securely fastened before building pressure in the system.
2. Release all system pressure before loosening any hydraulic connection in the system.
Operating Instructions
Hydraulic Connections
Clean all the areas around the fluid ports of the pump and cylinder. Inspect all threads and fittings for signs of damage
and replace as needed. Clean all hose ends, couplers, and union ends. Remove the thread protectors from the hydraulic
fluid outlets. Connect the hose assembly to the hydraulic fluid outlet and couple the hose to the cylinder.
WARNING
!
All Warning Statements must be carefully observed to help prevent personal injury.
1. Before operating the pump, all hose connections must be tightened with proper tools. DO NOT OVER TIGHTEN.
Connections should only be tightened securely and leak-free. Over tightening can cause premature thread failure
or high pressure fittings to split at pressures lower than their rated capacities. Should a hydraulic hose ever
rupture, burst, or need to be disconnected, immediately shut off the pump and release all pressure.
Never
attempt to grasp a leaking pressurized hose with your hands.
The force of escaping hydraulic fluid could cause
serious injury.
2. DO NOT subject the hose to potential hazards such as fire, sharp surfaces, extreme heat or cold, or heavy
impact. Do not allow the hose to be altered or kink, twist, curl, crush, cut, or bend so tightly that the fluid
flow within the hose is blocked or reduced. Periodically inspect the hose for wear, because any of these
conditions can damage the hose and possibly result in personal injury.
3. DO NOT USE THE HOSE TO MOVE ATTACHED EQUIPMENT. Stress can damage hose and possibly cause
personal injury.
4. Hose material and coupler seals must be compatible with the hydraulic fluid used. Hoses also must not come
in contact with corrosive materials such as creosote-impregnated objects and some paints. Consult the
manufacturer before painting a hose. Hose deterioration due to corrosive materials can result in personal
injury. NEVER PAINT COUPLERS.
5. Inspect machine for wear, damage, and correct function before each use. Do not use machinery that is not in
proper working order, but repair or replace it as necessary.
6. REPLACE WORN OR DAMAGED SAFETY DECALS.
7. MODIFICATION OF A PRODUCT REQUIRES WRITTEN ZINKO AUTHORIZATION.
8. Use only components with the same pressure rating when assembling a system or machine.
PUMP
1. DO NOT EXCEED THE HYDRAULIC PRESSURE RATING NOTED ON THE PUMP DATA PLATE OR TAMPER
WITH THE INTERNAL HIGH PRESSURE RELIEF VALVE. Creating pressure beyond the rated pressure can result
in personal injury.
2. Before replenishing the fluid level, retract the system to prevent overfilling the pump reservoir. An overfill can
cause personal injury due to excess reservoir pressure created when cylinders are retracted.
AIR SUPPLY
1. SHUT OFF AND DISCONNECT THE AIR SUPPLY WHEN THE PUMP IS NOT IN USE OR BEFORE BREAKING
ANY CONNECTIONS IN THE SYSTEM.
Operator Responsibilities
It is the operator's responsibility to read and understand the following safety statements. Only qualified operators should
install, operate, adjust, maintain, clean, repair, or transport this machinery. These components are designed for general
use in normal environments. These components are not specifically designed for lifting and moving people, agri-food
machinery, certain types of mobile machinery, or special work environments such as: explosive, flammable, or corrosive.
Only the user can decide the suitability of this machinery in these conditions or extreme environments. ZINKO will supply
information necessary to help make the decision. These instructions are intended for end-user application needs. Most
problems with new equipment are caused by improper operation or installation. A detailed parts list can be obtained from
ZINKO upon request.
Operating Instructions & Repair Parts List
Toll Free:
1-800-579-8088
Web:
www.zinko.com
ZINKO
H y d r a u l i c J a c k
M O D E L S
Air Hydraulic Foot/Hand Pump
ZAP-100 Series