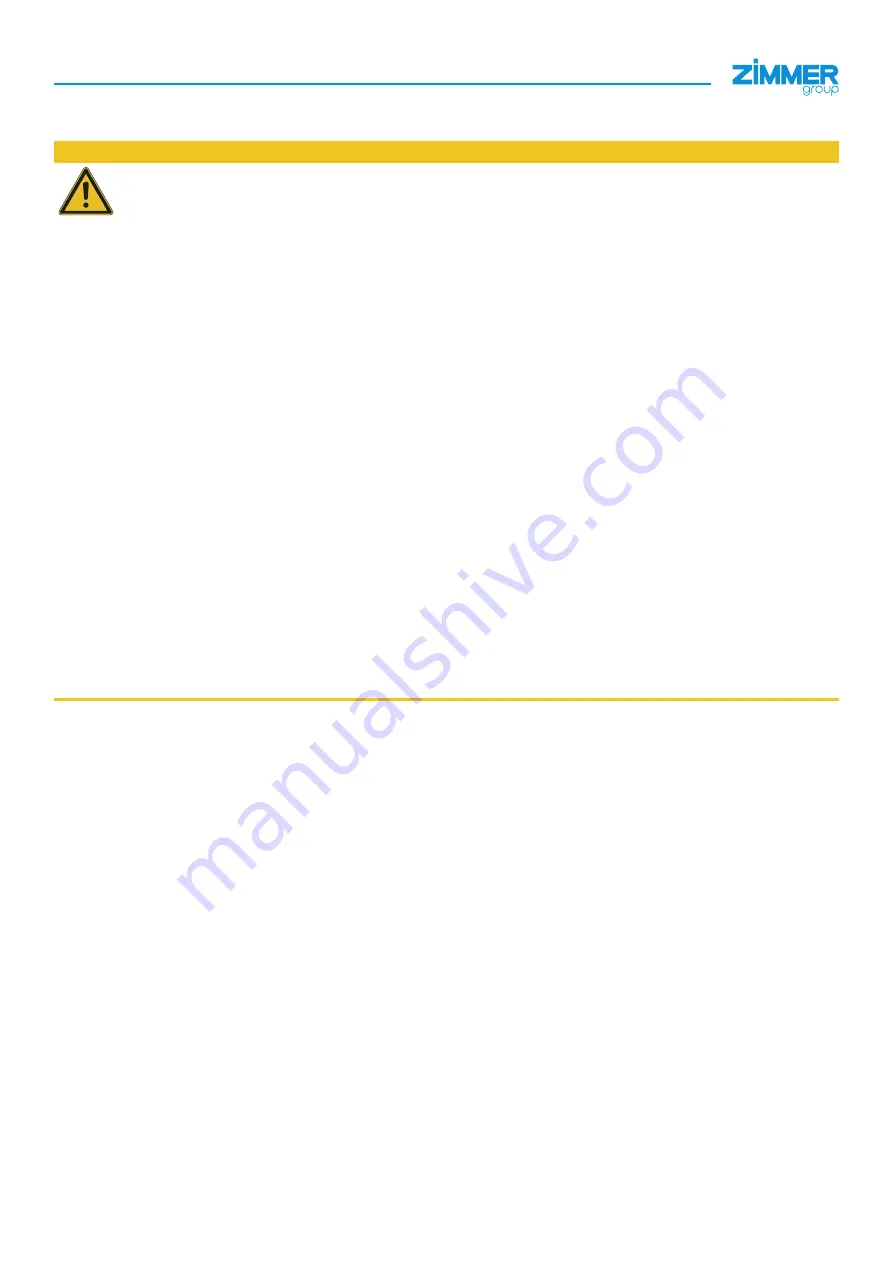
5
2 Safety notices
CAUTION
Risk of injury and material damage in case of non-compliance
Installation, commissioning, maintenance and repairs may only be performed by qualified specialists in
accordance with these installation and operating instructions.
The product is state-of-the-art.
It is mounted to industrial machines and is used to hold tools.
The following are examples of situations in which the product may cause a hazard:
• The product is not properly installed, used or maintained.
• The product is not used for its designated purpose.
• The locally applicable regulations, laws, directives or guidelines are not observed.
►
The product may only be used in accordance with these installation and operating instructions and the
product's technical data. Any changes or additions to the intended use of the product, as well as modifications
to the product, such as those in the following examples, require the written permission of the manufacturer:
•
Use of the product under extreme conditions, such as aggressive fluids or abrasive dusts
• Additional drilled holes or threads
Ö
Zimmer GmbH shall accept no liability for any damage caused by improper use. The operator bears sole
responsibility.
►
Make sure that the power supply is disconnected before you mount, adjust, modify, maintain or repair the
product.
►
Whenever work is carried out on the product, make sure that the product cannot be actuated by mistake.
►
Perform maintenance tasks, renovation work or attachment work outside of the machine's danger zone when
possible.
►
Do not reach into the operational range of the product.
►
Observe the specified maintenance intervals and specifications regarding the quality of the operating material.
►
When using the product under extreme conditions, adjust the maintenance interval according to the degree of
contamination.
INSTALLATION AND OPERATING INSTRUCTIONS:
WWR
DDOC00227 / p
EN / 2023-05-15
Zimmer GmbH • Im Salmenkopf 5 •
77866 Rheinau, Germany •
+49 7844 9138 0 • www.zimmer-group.com
Summary of Contents for WWR Series
Page 2: ......