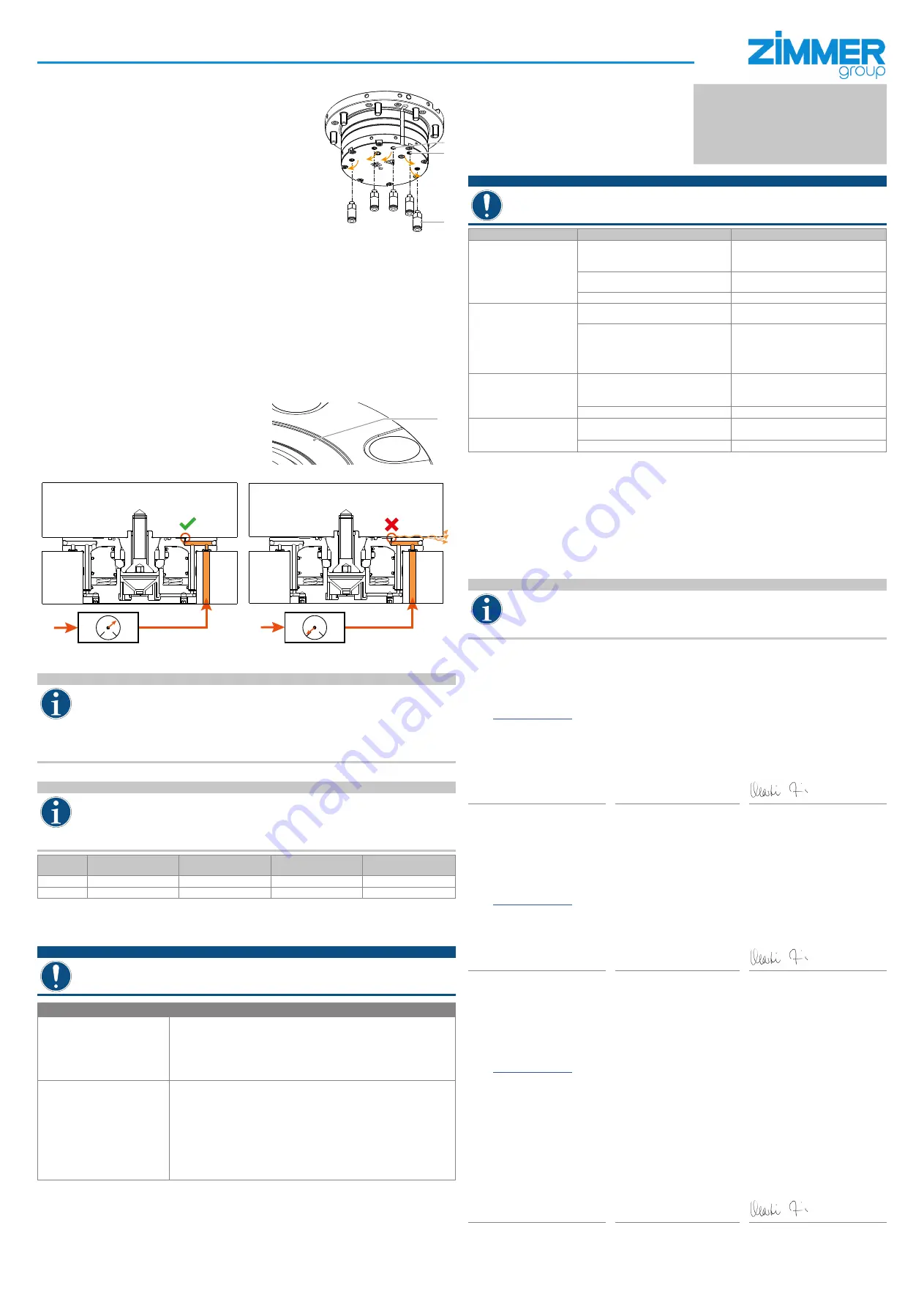
Zimmer GmbH
●
Im Salmenkopf 5
●
77866 Rheinau
●
Germany
●
+49 7844 9138 0
●
+49 7844 9138 80
●
www.zimmer-group.com
INSTALLATION AND OPERATING INSTRUCTIONS:
Zero-point clamping system, pneumatic, SPN series
Installation and
Im Salmenkopf 5
operating
instructions
77866 Rheinau
SPN series
Germany
DDOC00836
+49 7844 9138 0
Index c
EN 2021-12-09
www.zimmer-group.com
8.2 Installing alternative hose connections
The following work steps must be observed when installing the power
supplies:
►
Unscrew the grub screws
cn
.
►
Insert the O-rings
cp
.
Ö
Lubricate the O-rings.
►
Screw the pneumatic connections
co
into the alternative
connections.
Ö
If the PLUS connection
2
is not in use, insert a filter cm into the
connection (filter included loose).
Ö
The filter cm must be flush with the bottom of the product during
installation.
Ö
If the standard connections are to replace the alternative
connections, the alternative connections must be tightly sealed.
co
cn
cm
8.3 Checking operational readiness
After the product has been properly installed, the following properties must be checked to verify that it is ready to be operated:
• Check pneumatic connections for leaks by looking and listening
• Check all fastening screws for their prescribed tightening torque
• Check the product for leaks while it is pressurized by looking and listening
8.4
Disassembly
Removal is carried out in the reverse order of that described in Section „Montage Mechanik“.
9. Operation
During machining, the entire contact surface of the zero-point clamping system must be covered so that no dirt can penetrate.
►
Before any clamping, thoroughly clean the contact surfaces between the zero-point clamping system, the clamping pin and
the material to be clamped.
►
Protect the pin hole from dirt when the product is not in use.
►
To do this, use accessories such as the sealing pin or automatic seal.
►
During operation, secure the zero-point clamping system against unintentional loosening.
9.1 Positioning check
The product enables the testing or monitoring of the support using an
externally connected flow meter or dynamic pressure indicator.
This inspection verifies that the workpiece or clamping plate is
correctly supported on the product.
The flow or dynamic pressure is measured by means of the
designated borehole
bo
in the housing.
bo
Ö
The following illustrations depict an example of dynamic pressure sensing.
P
0
10
bar
P
0
10
bar
The clamped product is resting correctly on the contact surface.
Ö
This generates dynamic pressure.
The clamped product is not resting correctly on the contact
surface.
Ö
No dynamic pressure is generated (leakage).
INFORMATION
The operator of the product has sole responsibility for the positioning check. Sensing for the positioning check
is performed by means of an external flow meter or dynamic pressure indicator. The entire contact surface of the
product must be covered to ensure correct sensing during the positioning check.
Operating pressure for the positioning check: 1.5 bar
To use this function, an adjustable pressure switch must be connected upstream. This reduces the operating
pressure to the required 1.5 bar.
Ö
The power supply line is for blowing out, cleaning and the positioning check.
Please contact Zimmer Customer Service if you have any questions.
9.2 Piston position sensor
INFORMATION
The operator of the product has sole responsibility for piston position sensing. Sensing is performed by means of an
external flow meter or dynamic pressure indicator.
The entire contact surface of the product must be covered to ensure correct sensing during the piston position
sensing.
Operating pressure for piston position sensing: 1.5 bar
Please contact Zimmer Customer Service if you have any questions.
Connection
Operating pressure [bar]
Product unlocked
Pin clamped
Product closed/no pin
present
4
1 to 1.5
0
1
1
5
1 to 1.5
1
0
1
0 = dynamic pressure 1 = flow
10. Maintenance
The maintenance interval depends on the respective application. The higher the strain, the more frequently maintenance must
be carried out.
NOTICE
In case of visible damage or signs of malfunction, the zero-point clamping system must be taken out of operation
immediately. Do not start the product again until the damage has been repaired.
►
Replace any worn components.
Interval
Maintenance work
After 10,000 cycles or every 3 weeks
Visual inspection
The visual inspection merely involves visually inspecting component parts and their
function. If any irregularities or damage are identified during the visual inspection, a
more detailed check of the component parts must be carried out.
►
Carry out a visual inspection.
►
Clean the product if it is dirty.
After 50,000 cycles or every year
Measure the clamping force
►
Measure the clamping force.
•
Suitable devices for measuring the clamping force are available as
accessories.
Ö
Clamping force undershot by less than 15%
• Further use at the customer's discretion.
• Or have Zimmer GmbH perform the check.
Ö
Clamping force undershot by more than 15%
• Have Zimmer GmbH perform the check.
Dismantling and reassembling the product without authorization may result in complications, as special installation equipment is
required in some cases. Zimmer GmbH accepts no liability for any resulting malfunctions or damage.
11.
Troubleshooting
NOTICE
For error-free function of the product, it is necessary that the contact surface is always completely covered.
►
This prevents dirt from penetrating the system and causing malfunctions.
Error/fault
Possible cause
Measure
Product does not open
• Operating pressure is too low
•
Leakage/blockage/pinching of the power
supply lines
►
Increase operating pressure (4 to 6 bar)
►
Check power supply lines
• Excess force is acting upon the centering
pin
►
Reduce the tensile load or compressive
load on the product.
• Clamp dog does not move
►
Vent the PLUS connection
Long response time (too little
air is fed in)
• Valve is too small (product opens after a
delay)
►
Choose a larger valve accordingly
• Power supply lines from the valve to the
product are too long (product opens after
a delay)
►
Shorten the power supply lines (keep the
distance from the product to the valve as
short as possible).
►
Enlarge the cross-section of the power
supply lines.
Air leak or blow-off noise
•
Housing parts are leaky (O-rings not fitted
correctly)
• Installation error
►
Align/mount the product again.
►
Check the O-rings.
►
Open/close the product several times.
• Connecting cables are leaky.
►
Check power supply lines.
Dimensional deviations/chatter
marks
• Centering pin is not correctly retracted.
• Contamination of the product
►
Clean the product.
• Product worn
►
Completely replace the product.
12. Transportation/storage/preservation
►
The product must be transported and stored only in the original packaging.
►
If the product has already been installed on the superordinate machine unit, care must be taken during transport to ensure
that no unintentional movements can occur. Before commissioning and after transport, check all power connections and all
mechanical connections.
►
If the product is stored for an extended period, the following points are to be observed:
Ö
Keep the storage location as dust-free and dry as possible.
►
Clean all components. There must be no dirt left on the components.
►
Seal pneumatic connections by using suitable covers.
►
Observe the required temperature.
13. Decommissioning and disposal
INFORMATION
When the product reaches the end of its operational phase, it can be completely disassembled and disposed of.
Completely disconnect the product from the power supply. The product can be disassembled and properly disposed
of according to material groups.
When disposing of them, observe the locally applicable environmental regulations and codes and regulations for
disposal.
14. RoHS declaration
In terms of the EU Directive 2011/65/EU
Name and address of the manufacturer:
Zimmer GmbH
Im Salmenkopf 5, 77866 Rheinau, Germany
+49 7844 9138 0
+49 7844 9138 80
www.zimmer-group.com
We hereby declare that the incomplete machine described below
Product designation:
Zero-point clamping system, pneumatic
Type designation:
SPN series
conforms to the requirements of the directive in its design and the version we put on the market.
Michael Hoch
Rheinau, Germany, 2020-03-31
Authorized representative for compiling
the relevant technical documents
(Place and date of issue)
Martin Zimmer
(Legally binding signature)
Managing Partner
15. REACH declaration
In terms of the EU Regulation 1907/2006
Name and address of the manufacturer:
Zimmer GmbH
Im Salmenkopf 5, 77866 Rheinau, Germany
+49 7844 9138 0
+49 7844 9138 80
www.zimmer-group.com
REACH stands for
R
egistration,
E
valuation,
A
uthorisation and
R
estriction of
C
hemicals.
A full declaration of REACH can be obtained from the manufacturer due to the duty to notify in accordance with Art. 33 of the
REACH regulation ("Duty to communicate information on substances in articles").
Michael Hoch
Rheinau, Germany, 2020-03-31
Authorized representative for compiling
the relevant technical documents
(Place and date of issue)
Martin Zimmer
(Legally binding signature)
Managing Partner
16. Declaration of Conformity
In terms of the EU Machinery Directive 2006/42/EC (Annex II 1 A)
Name and address of the manufacturer:
Zimmer GmbH
Im Salmenkopf 5, 77866 Rheinau, Germany
+49 7844 9138 0
+49 7844 9138 80
www.zimmer-group.com
We hereby declare that the following, identically constructed safety components
Product designation:
Zero-point clamping system, pneumatic
Type designation:
SPN series
conform to the requirements of the 2006/42/EC directive in their design and the version we put on the market.
The following harmonized standards have been used:
Basic health and safety requirements:
DIN EN ISO 12100:2011-03 Safety of machinery – General principles for design – Risk assessment and risk reduction
DIN EN ISO 13849-1/-2
Safety of machinery – Safety-related parts of control systems
EN 349:1993+A1:2008
Safety of machinery – Minimum gaps to avoid crushing of parts of the human body
A full list of applied standards can be obtained from the manufacturer.
Clemens Kimmig
Rheinau, Germany, 4/30/2021
Authorized representative for compiling
the relevant technical documents
(Place and date of issue)
Martin Zimmer
(Legally binding signature)
Managing Partner