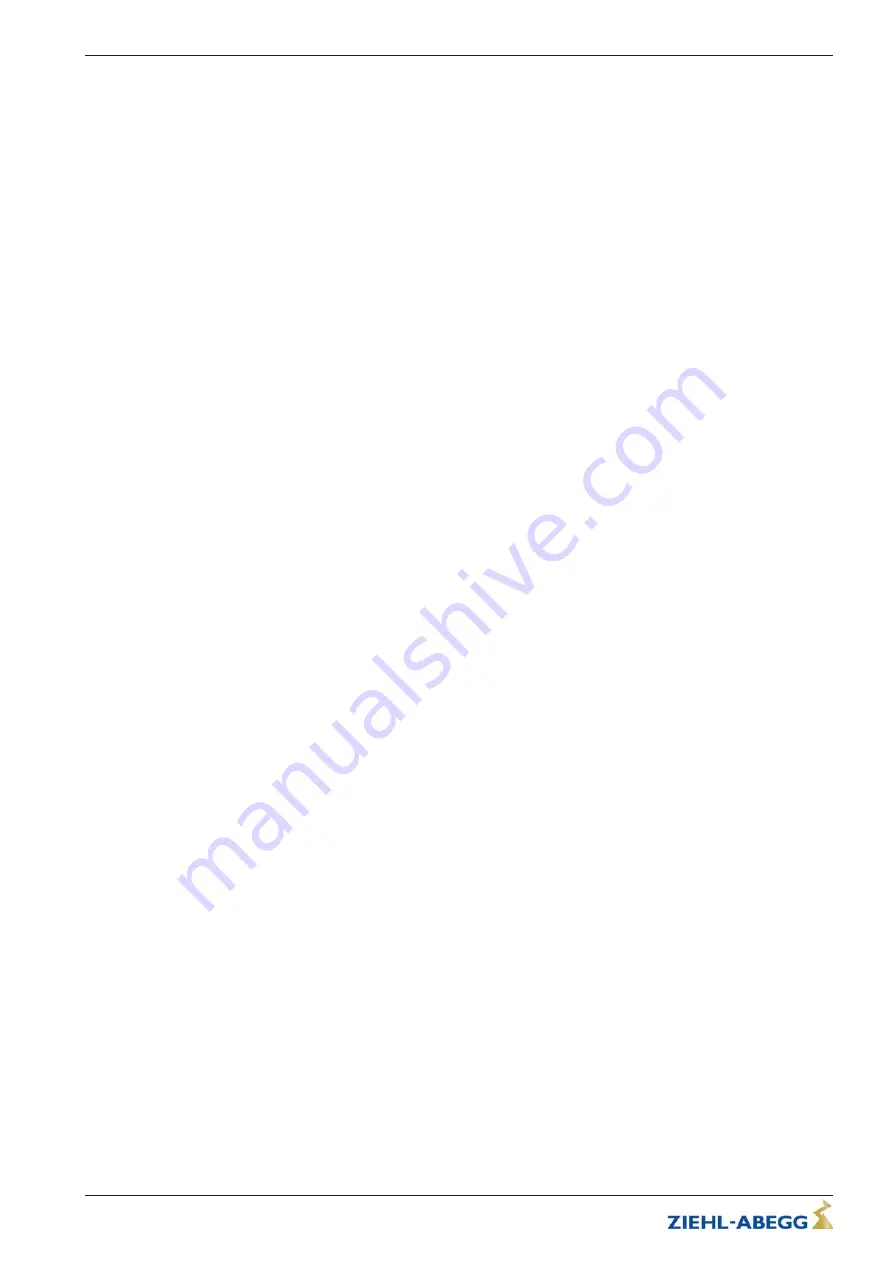
Half load test with release of the brake only
"
The shorting circuit, if installed, should be disabled for the duration of the half load test.
"
With a half load and the brake released, the car may not move.
"
After the half load test, the shorting circuit is to be reactivated.
6.3.2
Testing the brake in accordance with EN 81-20:2014
"
When testing the brakes, the short-circuit wiring has to be deactivated to only test the effect of the
brake.
"
It is recommended to perform the tests when the car position is about in the middle of the shaft.
1. Overload
"
The test shall be carried out whilst the car is descending at rated speed with 125 % of the rated
load and interrupting the supply to the motor and the brake.
2. Failure of one brake circuit:
"
The test shall be carried out whilst the car is descending at rated speed with rated load.
"
To simulate failure of a brake circuit, it must be possible to keep the brake circuits open mechan-
ically independently of one another even when opening the safety circuit.
"
This condition may not be permanent and must therefore be created using buttons or similar.
"
At the same time, the safety circuit should be opened when using this function.
"
For this test, the elevator must be observed.
"
If no discernible delay occurs, the brake circuit held open is to be closed immediately.
"
The system should be stopped and the brake tested.
As an example, refer to the principle circuit diagram in the
“
Electrical installation / Brake / Brake
control
”
chapter. The logic of the principle circuit diagram should be understood. Transferability to the
relevant application must be veri
fi
ed and ZIEHL-ABEGG SE provides no guarantee of suitability.
If the circuit is designed in accordance with the principle circuit diagram:
"
At the nominal speed, press one of the buttons and hold it down until the elevator has stopped.
"
Repeat the test with the other button to test the second brake circuit.
3. Testing the microswitches / inductive proximity switches
"
The release monitoring for the brakes must be evaluated.
"
Before every trip, the change in the state of both brake circuits must be monitored separately.
"
Switching must thus be tested individually, according to the function as an NC and/or NO contact.
"
If there is a missing or incorrect signal, the elevator cabin may not leave the stopping point.
6.4
Pull out of safety gear
If the car loaded with the nominal load enters the trap due to a malfunction or during the TÜV
certi
fi
cation, it is possible that the trap device is seated rather
fi
rmly. In such a case, it is entirely
possible that the elevator machine torque is no longer suf
fi
cient to pull the car out of the trap.
With gearless elevator machines in the shaft, the elevator machine is usually not accessible. A
handwheel is unnecessary in such a layout.
With gearless elevator machines in machine rooms, a handwheel does not make any sense because
there is no gear reduction. That is because due to the low moment arm of force, only slight force can
be applied. A handwheel could even present a hazard, as even with only a slight imbalance in the
installation, it is no longer possible to stop the elevator with the handwheel.
For both cases involving gearless elevator machines:
"
If the elevator machine torque or the driving capability is not suf
fi
cient, a block and tackle or similar
should be used.
"
It is advisable to have a suitable block and tackle on hand for the TÜV inspection.
Information
Note that an overload in the car leads to an increase in the motor torque. 25 % overload results in
150 % of the required motor torque! As regulated elevator machines are normally designed for a
maximum torque of ca. 170 - 200 % rated torque, only slight reserves are available during such
special cases.
Correspondingly, section
6.3.4 "Capture device on the cabin"
in
EN 81-20:2014
must be followed:
“
To enable the cabin to be lifted out of the trap more easily, we recommend performing the test close
to a door so that the load can be removed from the cabin there.
”
Original operating instructions
ZAtop
–
model series SM180
Start-up
A-TBA17_05-GB 2008 Index 003Part.-No. 01015765-GB (EU-BD 845/1 + 845/2)
22/76