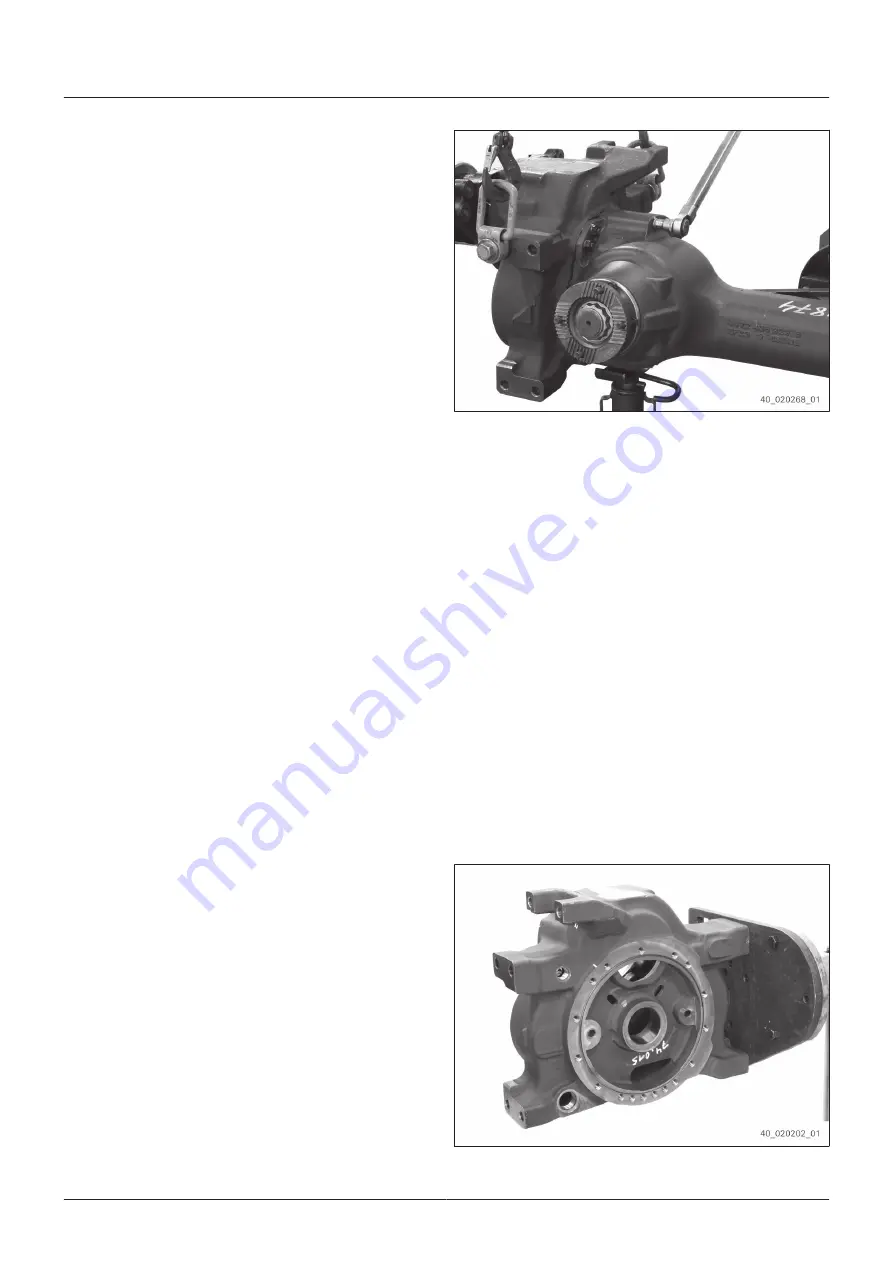
5.
Support axle from below.
6.
Push differential into the axle housing and
bring portal housing into contact position
with the axle housing.
7.
Fix portal drive with Torx screws.
Tightening torque: 185 Nm
Fix portal drive with hexagon nuts.
Tightening torque: 200 Nm
Fig. 198
9.6
Assemble and install right portal drive
9.6.1
Assemble right portal drive
Special tools:
▪
▪
▪
▪
▪
▪
▪
▪
▪
▪
▪
▪
AA00.387.830 Pressing fixture no.
1.
Use 5870.350.110 [Connection plate] to fix
the portal housing to
5870.350.000 [Assembly truck].
Fig. 199
Assembly
EN 4472.751.001 - 2015-11
103
Summary of Contents for AV 110
Page 1: ...REPAIR INSTRUCTIONS AV 133 Bus axle with compact bearing BUSES ...
Page 137: ......