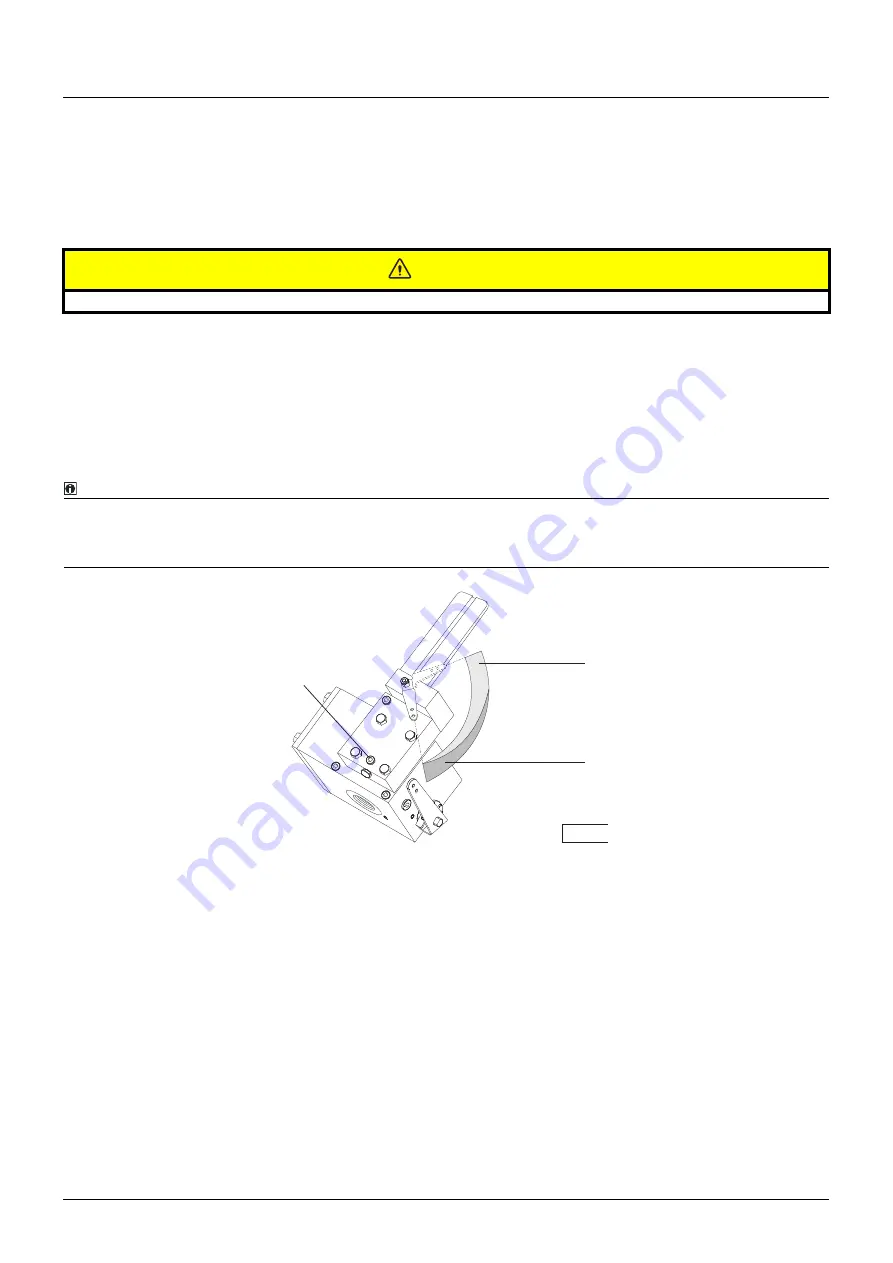
Introduction
14
EN_3224.758.102d_2021_12
1.6.5 Mechanical trolling valve (MTV)
The trolling valve is a device that allows for varying the speed of the propeller, regardless of the engine's rotation spe-
eds. The MTV is commonly applied in the following cases:
1. the watercraft's speed is too high even though the engine is at minimum power.
2. the rotation speed of the PTO must exceed the propeller's rotation speed.
• Maximum rotation speed = (max engine revolutions x 0.5) rpm, for engines with maximum rotation speed below
2000 rpm.
• Maximum rotation speed = (1000) rpm, for engines with maximum rotation speed above 2000 rpm.
Depending on the reverse transmission's reduction ratio, the propeller's dimensions and the features of the watercraft,
the actual rotation speed of the propeller can be reduced by a percentage varying between 30% and 70% of the useful
speed.
Recommended range of use: 60-80°C.
a. Clutch slipping
b. Clutch pressure
c. pressure gage fitting (15)
The MTV can be used in both directions of motion and the maximum usage speeds are:
NOTE:
Mode of use
Verify that the MTV is excluded before engaging the gear. After engaging the gear, gradually move the MTV lever until reaching the
desired maneuver speed.
The number of revolutions can be varied during operation in trolling mode within the limits mentioned above.
CAUTION
c (15)
Fig. 5
a
b
Summary of Contents for 400 Series
Page 1: ...ZF 400 Family Operating Instructions...
Page 4: ...4 Index EN_3224 758 102d_2021_12...
Page 29: ......