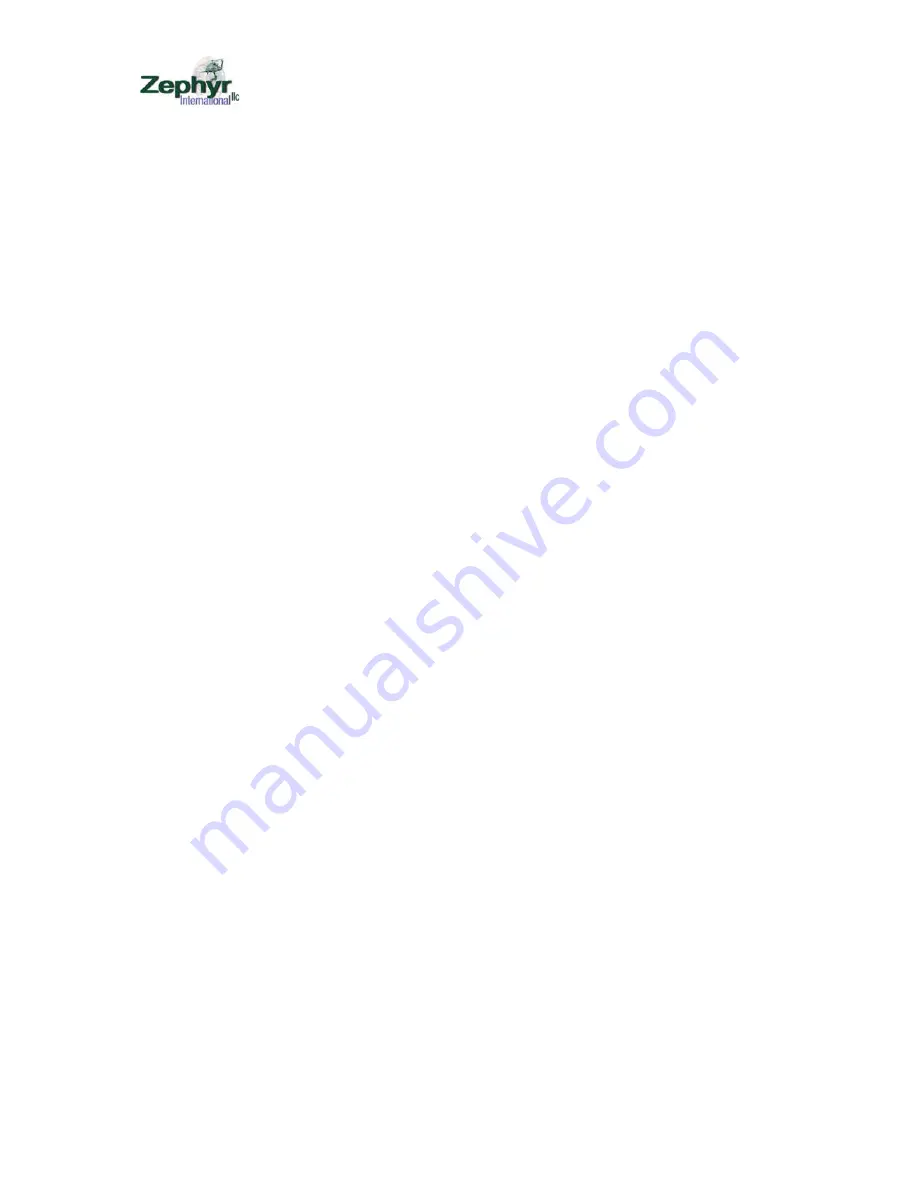
ZOM-12000-1 rev 0
Page2 of 15
Fixed Hoist Test Facility (FHTF)
Purpose
: The FHTF when used in conjunction with the Mobile Ground Support
Equipment (MGSE) provides the capability to operate the hydraulic rescue hoist off of
the aircraft in order to perform intermediate level maintenance and troubleshooting.
Description of FHTF
: The FHTF consists of an upright structure, an upper weldment
assembly, a hanging hoist mount, a chain hoist for raising and lowering the unit under
test (UUT), a load weigh system, a hydraulic power supply, a 28 volt power supply, a
differential pressure measuring system and a flow measuring system. The hydraulic
supply is powered by a 230 volt 3 phase electric motor, and two boost transformers are
used to boost the facility’s 208 volts 3 phase power to 230 volts.
The UUT control signals are provided by a government supplied controller and pendant.
Theory of Operation
: The FHTF provides 3000 psi hydraulic power at a maximum 6.5
gallons per minute. The hydraulic supply includes a shut off valve to bypass the flow
when the hoist is not running. The hydraulic system uses MIL-H-83282 hydraulic fluid
and includes a high pressure filter rated at 3 microns and a low pressure filter rated at 3
microns.
The upright structure is equipped with a chain hoist to raise the UUT up to the top of the
structure where it is attached to two load cells. The two load cells provide signals to a
load cell summing box where the signals are summed and sent to a display. The load
readout can be set to zero to tare the readout with no load applied to the rescue hoist
hook.
The wire rope tensile load is provided by the MGSE. The MGSE provides the capability
to extend the wire rope under approximately 150 lbs. maximum load, and provides the
capability to retract the wire rope under approximately 600 lbs. maximum load.
The hydraulic system includes two pressure transducers in the pressure and return lines.
The transducers provide signals to a microprocessor that displays the differential pressure
the UUT requires to lift the load. The hydraulic system is also equipped with a turbine
flow meter that provides a signal to the flow display.
The 28 volts required to control the UUT hydraulic control system is provided by a
power supply mounted in the junction box. The control pendant is mounted via its
connector directly to the front of the junction box, and the electrical control box is
mounted to the front of the test table. Two electrical cables couple the control box to the
junction box and the electrical controller to the hoist.
Electrical loads:
208 volts 3 phase is approximately 16 KVA requires a 125 amp line fuse
120 volts single phase approximately 15 amps
Summary of Contents for ZGS-12000-1
Page 1: ...ZOM 12000 1 rev 0 Page1 of 15 Fixed Hoist Test Facility FHTF ZGS 12000 1 ...
Page 10: ...ZOM 12000 1 rev 0 Page10 of 15 Assembly Drawing and major parts list ZGS 12000 1 ...
Page 11: ...ZOM 12000 1 rev 0 Page11 of 15 ...
Page 12: ...ZOM 12000 1 rev 0 Page12 of 15 ...
Page 13: ...ZOM 12000 1 rev 0 Page13 of 15 ...