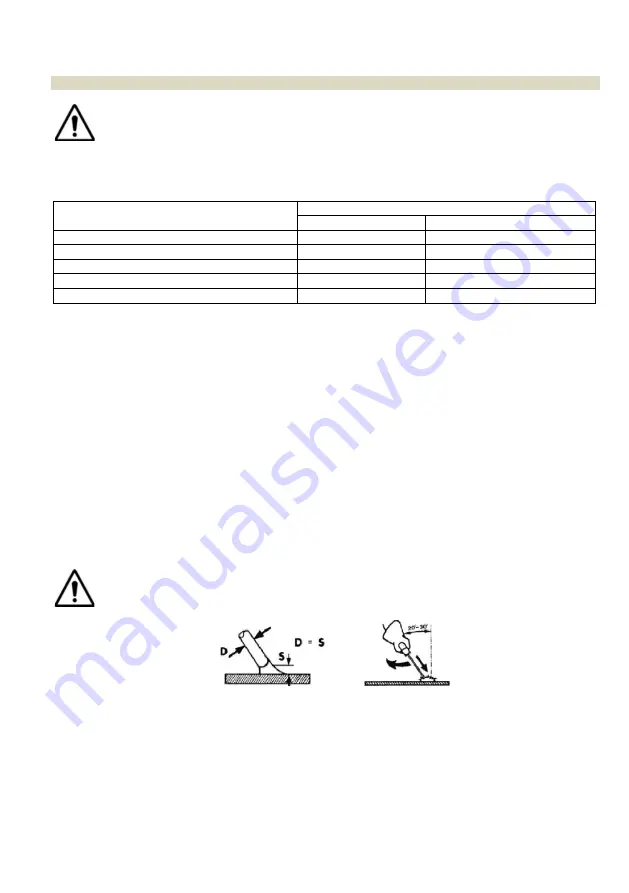
34
Never use metallic constructions which are not the part of the piece to be welded instead of cable with
functional terminal, as this will violate safety and lead to poor welding.
WELDING
WARNING!
Most welding electrodes are connected to the positive pole, although some
types have to be connected to the negative pole. It is important to follow manufacturer’s
instructions on the package of the electrodes, as they indicate right polarity of the welding
electrode as well as the most suitable current for welding operations.
Adjust welding current according to diameter of used electrode and according to type of welding seam.
Below is the table of admissible current according to diameter of the electrode:
Electrode diameter, mm
Welding current
, А
Min
Max
1,6
25
50
2
40
80
2,5
60
110
3,2
80
160
4
120
200
Pay attention, that depending on the diameter of the electrode, higher values of welding
current are used for welding in lower position, whereas vertical welding (or welding in vertical position,
so called «overhead welding») requires lower values of welding current.
Except for welding current power mechanical characteristics of the welding seam are
determined by other parameters:
- diameter and quality of the electrode;
- arc length;
- speed and position of welding;
- proper storage of electrodes (they must be protected from environmental exposure and kept in a
special package).
Welding
When welding
ALWAYS
wear protecting mask with special goggles for eye protection from strong
light emission, generated by electric arc. Mask allows watching the process of welding and protects
the user.
Keeping mask
IN FRONT OF YOUR FACE,
lead the electrode on welding area. Hand movement
must resemble lighting a match. This is the right way to strike the arc.
WARNING!
Never knock with electrode trying to strike the arc, as this may lead to its
damage and will hamper arc striking.
As soon as the arc is struck, try keeping the distance from welding point equal to electrode
diameter. Remember that electrode angle when moving should be 20-30 degrees.
After making welding seam move the electrode back. This is necessary for filling the welding crater.
Dangerous factors when performing welding operations
Fire prevention:
• all inflammable materials should be removed from the welding area;
• do not strike the arc on a gas tank or near it;
• never attempt to weld fuel tanks or tanks filled with gas unless all measures are taken to guarantee
that they contain no fumes;
• before welding fuel tanks they must be thoroughly cleaned with steam.
Summary of Contents for ZSI-255
Page 1: ...255 255 Inverter welding machine ZSI 255 RU UA ENG...
Page 2: ...2 CONTENTS 1 3 2 17 3 Instruction manual English 31...
Page 3: ...3 255 255 220 1 1 1 1 1 1 1 1 2 1 1 3 1 1 4 1 1 5...
Page 5: ...5 10 1 2 2 5 40 2 2 2 1 2 1 1 255 220 2 1 2 5 40 80 2 1 3 I 220 15 50 60 2 1 4 2 2 255 1...
Page 6: ...6 1 1 2 3 4 5 6 2 3 2 3 1 IGBT 50 30...
Page 7: ...7 2 3 2 Anti stick 2 3 3 5 2 3 4 4 2 3 5 3 2 3 6 3 1 3 1 2 3 2 3 3 2...
Page 10: ...10 4 2 20 30 4 3...
Page 11: ...11 4 4 5 5 5 1 5 2 5 2 5 2 1 5 2 2 5 2 3...
Page 12: ...12 5 3 5 3 1 6 5 3 2 1 6 6 1 6 2...
Page 13: ...13 3 25 40 1 220 15 10 4 4 25 4 25 80 1 7 7 1 3 7 2 5 40 80 7 3...
Page 17: ...17 255 255 220 1 1 1 1 1 1 1 1 2 1 1 3...
Page 20: ...20 1 1 2 3 4 5 6 2 3 2 3 1 IGBT 50 30 2 3 2 anti stick 2 3 3 5...
Page 21: ...21 2 3 4 4 2 3 5 3 2 3 6 3 3 1 2 3 2 3 3 2 1...
Page 24: ...24 4 3 4 4...
Page 25: ...25 5 5 5 1 5 2 5 2 5 2 1 5 2 2 5 2 3 5 3 5 3 1 6 5 3 2 1...
Page 26: ...26 6 6 1 6 2 3 25 40 1 220 15 10 4 4 25 4...