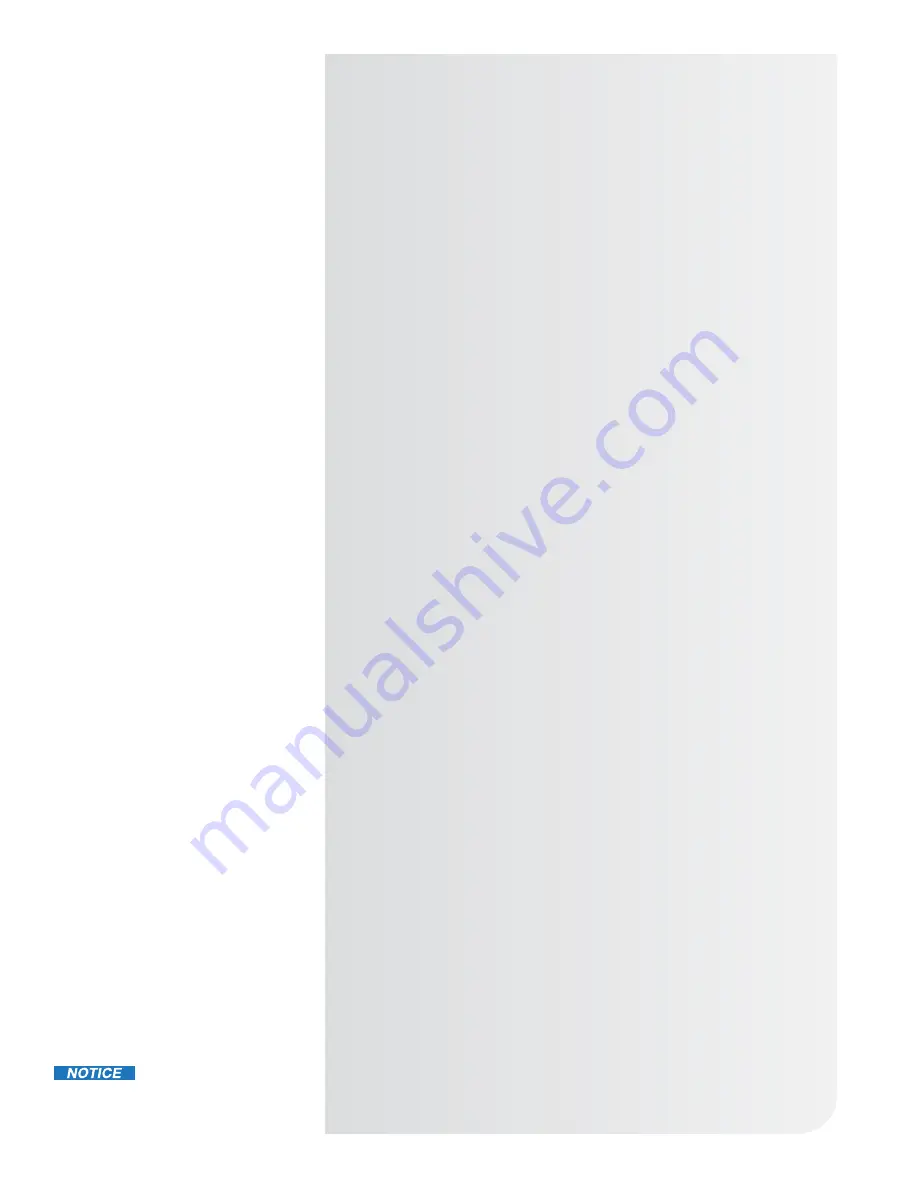
6
Installation
Inspection
Upon receipt of the equipment, carefully check the shipment against
the bill of lading. Make sure all units have been received. Inspect the
packaging of each unit, and inspect each unit for damage. Ensure that
the carrier makes proper notation of any shortages or damage on all
copies of the freight bill and completes a common carrier inspection
report. Concealed damage not discovered during unloading must be
reported to the carrier within 15 days of receipt of shipment. If not
filed within 15 days, the freight company can deny the claim without
recourse.
Storage
Equipment should be stored in its original packaging in a clean,
dry area.
Unit protection
Cover units on the job site with either the original packaging or an
equivalent protective covering. Cap the open ends of pipes stored on
the job site. In areas where painting, plastering, and/or spraying has not
been completed, all due precautions must be taken to avoid physical
damage to the units and contamination by foreign material. Physical
damage and contamination may prevent proper start-up and may result
in costly equipment clean-up.
Examine all pipes, fittings, and valves before installing any of the
system components. Remove any dirt or debris found in or on these
components.
Pre-installation
Before unit start-up, read all manuals and become familiar with the unit
and its operation. Thoroughly check the system before operation.
It is the responsibility of the purchaser to file all
necessary claims with the carrier. Notify your
equipment supplier of all damage within fifteen
(15) days of shipment.
Summary of Contents for Fanvector FV-04
Page 15: ......