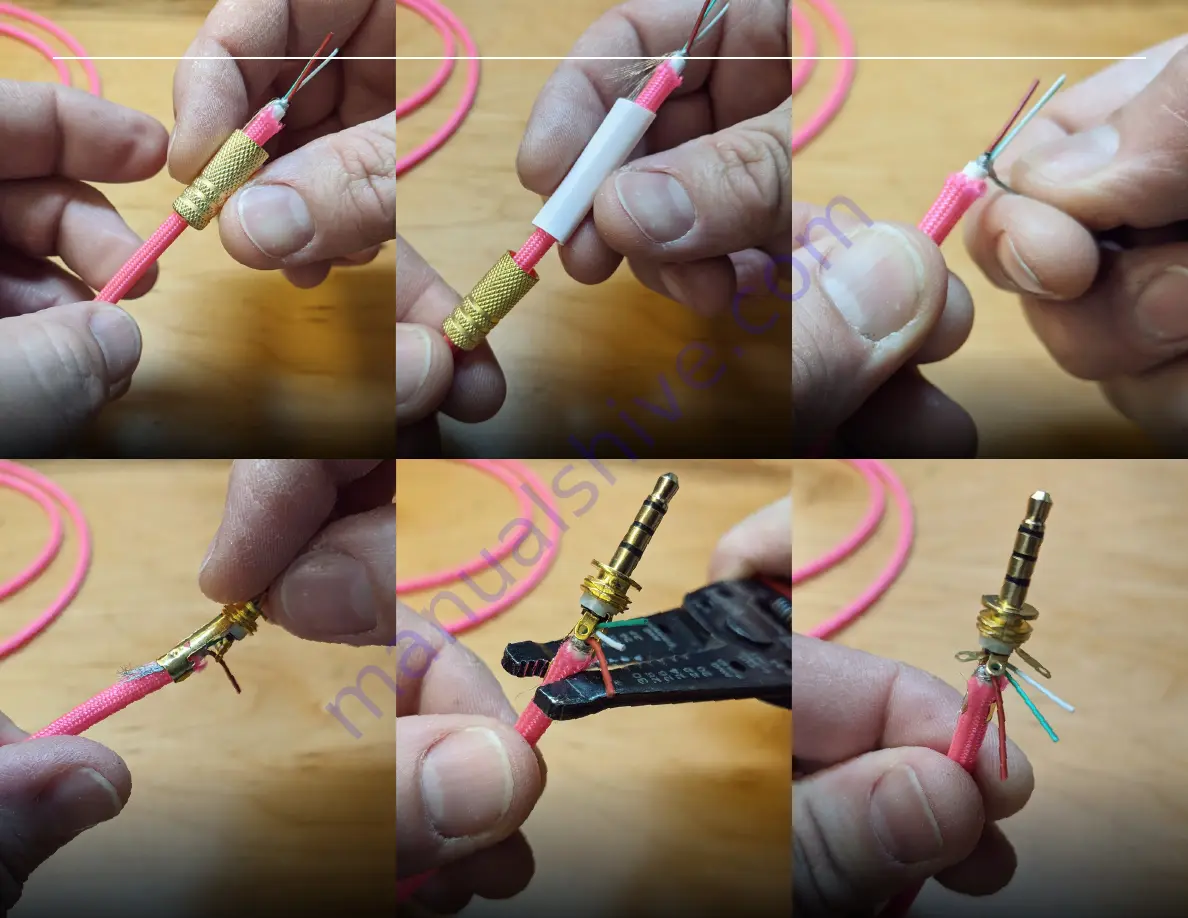
7
Important!
Before you start attaching the connector,
make sure you have slid the outer barrel onto the cable.
If you forget, you will need to re-do a lot of work later!
10
Place the connector onto the cable with the clamps
making solid contact with the gathered shielding. The
shielding needs to make physical contact with the clamp
tab for proper shielding/grounding.
8
Along with the barrel, remember to slide the heatshrink
onto the cable. You won't need the barrel and heatshrink
right away, so feel free to slide them further down the
cable and out of the way.
11
Using a pliers or wire stripper, crimp the clamps down
as securely as possible. Make sure the clamp is gripping
both cable and cord sleeving. Avoid crimping in only one
spot. Crimp, rotate a little, crimp again. You want the
clamps to hug the cable as much as possible.
9
Make sure the shielding is folded back, and gather/twist
it together on one side of the cable.
12
Inspect your work. Trim away any loose strands of
shielding. If they touch the other tabs/conductors later
it will cause a short. Gently fold the tabs up/out to make
inspection (and soldering) easier.
Note:
If you bend the tabs harshly, or too many times, they may
crack or break off.
Zap Cables Instructional Series
DIY TRRS Cable Kit Guide