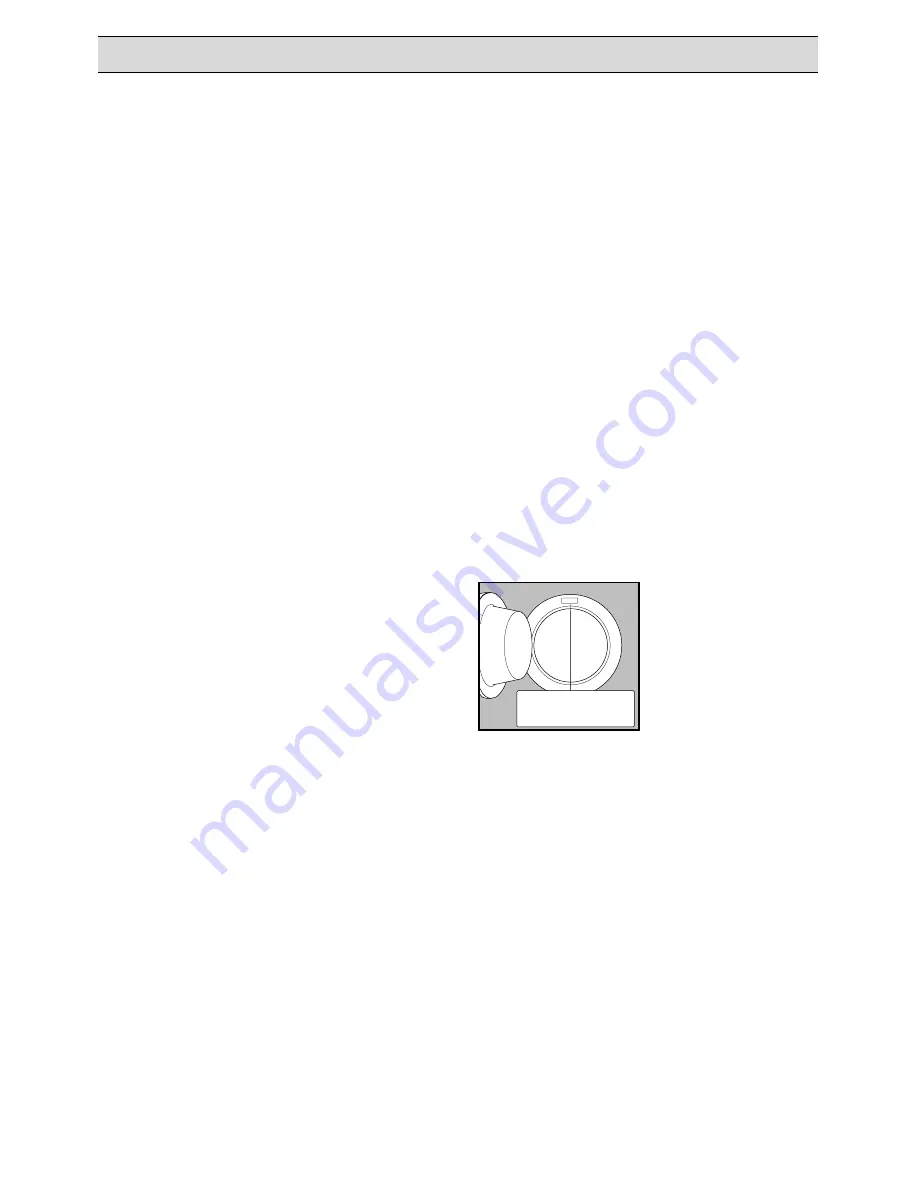
SERVICING
17
Before contacting your local ZANUSSI
Service Centre, please make the following
checks:
The machine does not start up
■
The door is not closed properly
■
No water is entering the machine (see: the machine
does not fill)
■
The selector dial is not correctly positioned and pulled
out
The machine does not fill
■
The water taps are not turned on
■
The water supply has been disconnected
■
The inlet hoses are kinked
■
The water pressure is too low
■
The water inlet filters are clogged
■
The door is not closed properly
The machine empties as it fills
■
The end of the drain hose is too low
■
The end of the drain hose is submerged in water
■
Drain pipe has no vent-hole
The machine does not drain or spin
■
You have selected a gentle programme with the rinse
hold option
■
The drain filter is clogged
■
The drain hose is kinked
■
The drainage system pipes are blocked
■
The drain hose extension is incorrect
■
The wash load is unbalanced: redistribute the clothes
inside the drum to allow the machine to spin
The machine leaks or overflows
■
Too much detergent
■
Unsuitable detergent
■
The inlet hose(s) is (are) loose
■
The detergent dispenser drawer or recess is clogged
■
The end of the drain hose is not securely positioned
■
The drainage system pipes are blocked
The machine vibrates or is noisy
■
The internal packing has not been removed
■
The machine is not level
■
The machine is in contact with the wall or furniture
■
The washing load is badly distributed
■
The machine is overloaded
The door does not open
■
The safety device has locked it
■
Water in the tub: the door cannot be opened if water
is present in the tub
If after the above checks, there is still a fault, call your
local Zanussi Service Force Centre.
In-guarantee customers should ensure that the
above checks have been made as the engineer will
make a charge if the fault is not a mechanical or
electrical breakdown. Please note that proof of pur-
chase is required for any in-guarantee service calls.
Service & Spare Parts
If you require an engineer or wish to purchase spare
parts contact your local Zanussi Service Force Centre by
telephoning:
0990 929929
Your telephone call will be routed to the Service Centre
covering your post code area.
Further information can be found in the accompanying
customer care booklet and also in your telephone direc-
tory under “Z”.
When you call the Service Force Centre please make
sure you give the model and serial number of the appli-
ance.
This information can be
found on the rating plate
(see picture) or on the
guarantee card.
Customer Care
For general enquiries concerning your Zanussi appliance
or for further information on Zanussi products, please
contact our Customer Care Department by letter or tele-
phone as follows:
Customer Care Department
Zanussi
Zanussi House
Hambridge Road
Newbury
Berkshire
RG14 5EP
Tel 01635 521313
Mod. ..........
Prod. No. ...........
Ser. No. .........
Mod.
..........
Ser.
P0042