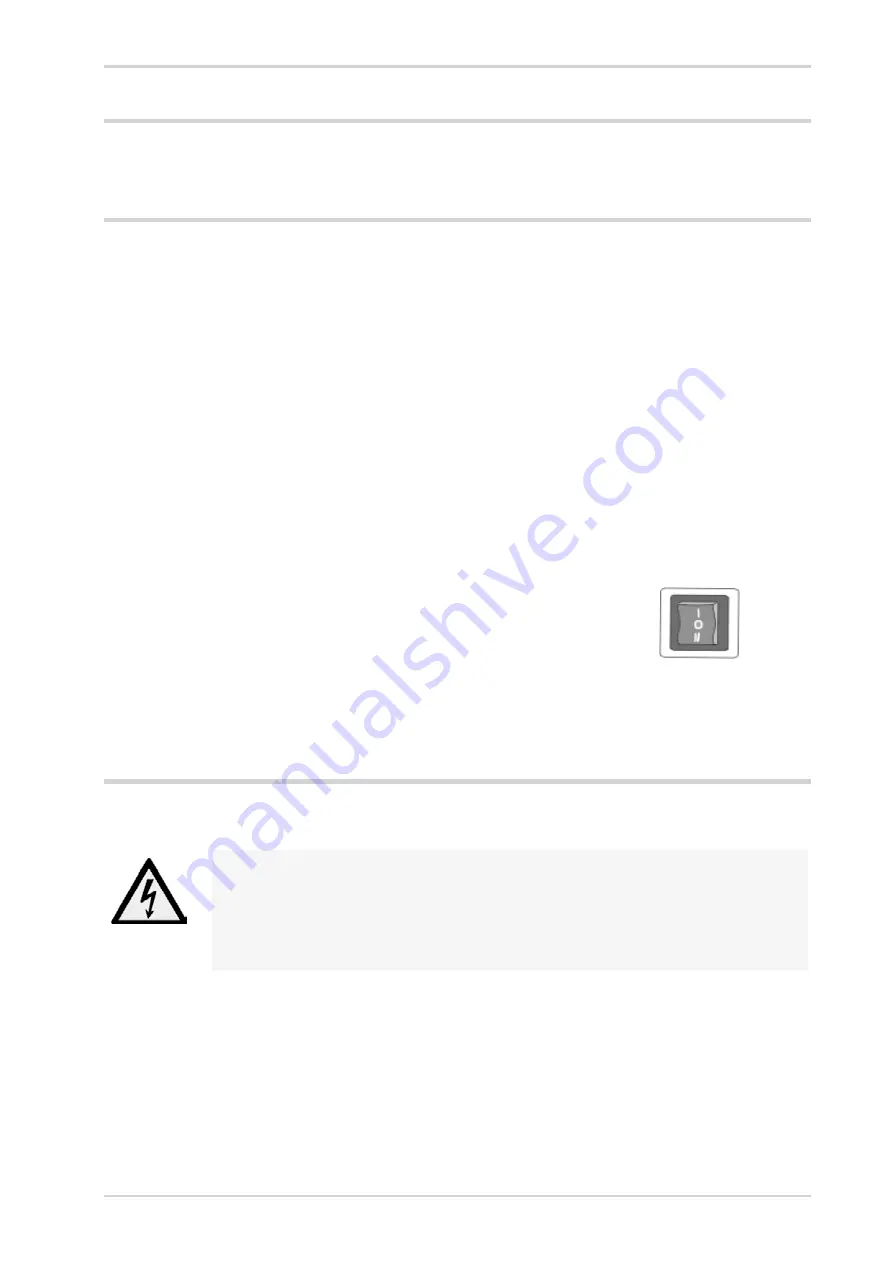
Shutdown and restart dryer
HDK350_EN_01_2005-05-10
43
Emergency shutdown
In any emergency proceed as described in the next section.
Depressurising and shutting down the dryer
In order to make the dryer safe, follow the instructions in the next three sections:
Disconnect dryer from compressed air system
►
Close the compressed air outlet valve (provided by operator).
►
Close the compressed air inlet valve (provided by operator).
Depressurise dryer
►
Leave the dryer on until the expansion phase in both vessels has been
completed.
During the expansion phase, the vessels are completely depressurised.
►
Check the pressure in the dryer at both vessel pressure gauges. The
pressure gauges should show value "0".
Disconnect voltage supply
►
Switch off the dryer by setting the ON/OFF
switch to position
0
.
ON/OFF switch
If work is to be carried out on the electrical system
►
Depressurise and shut down the dryer, following the instructions in the above
chapter.
Risk of injury due to voltage-carrying parts!
The electrical supply cable and external power lines are live even after the
dryer is switched off and, in the event of body contact, may cause serious
injury! Before carrying out any work on the electrical system, the electrical
supply cable and all external power lines must be made voltage-free!
►
Make the electrical supply cable to the dryer voltage-free.
►
Secure the electrical supply cable to the dryer against switch-on.
Summary of Contents for HDK 50/100
Page 1: ...High Pressure Dryer HDK 50 100 600 350 Operating Instructions Issue 05 2005 EN...
Page 3: ......
Page 4: ......
Page 6: ......
Page 72: ...Dimensional drawing 72 HDK350_EN_01_2005 05 10 Items Option...