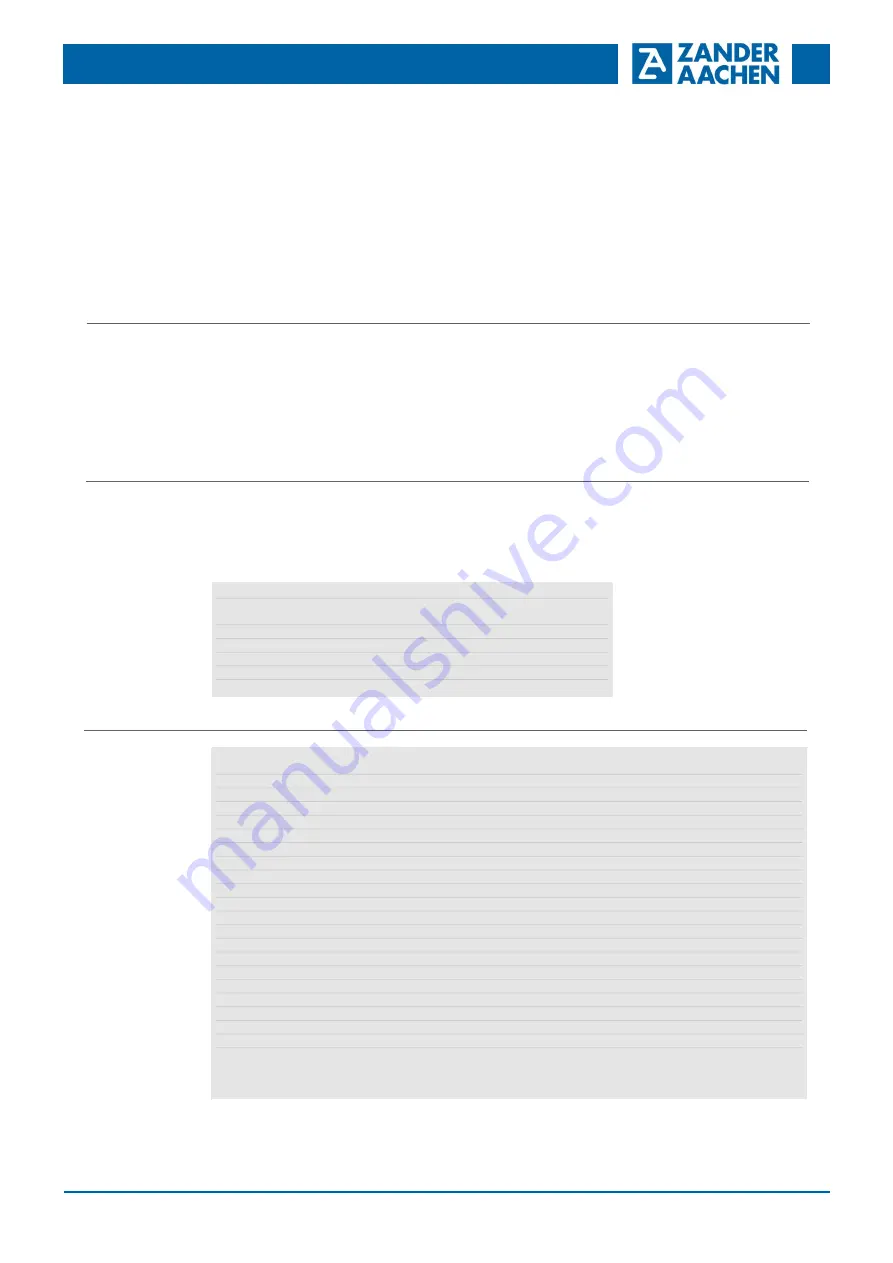
User Manual
Coded Non Contact Safty Magnetic Switch ZCode -RC(E)
4
M07
E61-352-00
H. ZANDER GmbH & Co. KG • Am Gut Wolf 15 • 52070 Aachen • Deutschland
Tel +49 241 910501-0 • Fax +49 241 910501-38 •
[email protected] • www.zander-aachen.de
Techn. Data
Correspondents to the standards
EN ISO 13849-1; EN ISO 14119; EN 60204-1;
EN 60947-5-3; UL 508; CSA-C22.2 No. 14
Approvals
CE, TÜV, UL
Power Supply
DC 24
V, +/- 10%
Contact rating safety outputs
DC 24
V, max. 500
mA, short circuit proof
Contact rating auxiliary output
DC 24
V, max. 200
mA, short circuit proof
Contact release time
max. 2
ms
Dielectric withstand
AC 250
V
Insulation resistance
100
MOhm
Recommended setting gap
5
mm
Switching distance, max.
Sao 10
mm Close / Sar 20
mm Open
Tolerance to misalignment
5
mm in each direction at 5
mm setting gap
Switching frequency
max. 1,0
Hz
Approach speed
200
mm/min - 1000
mm/s
Body material
Red Plastic / Stainless Steel 316
Dimensions Ø x L
30 mm x 60 mm (switch: 15 mm)
Weight (with M12-Connector)
approx. 110 g (Plastic) / approx. 220
g (Stainless Steel)
IP Protection
IP67, IP69K (with M12 connector IP67)
Temperature Range
-25
°C to +80
°C Plastic, +105
°C Stainless Steel
Shock Resistance
11
ms, 30
g
according to IEC 68-2-27
Vibration Resistance
10 - 55
Hz, 1
mm
according to IEC 68-2-6
Cable Type
PVC 8-core, 6
mm O.D. for 2NC/1NO, 0,25 mm²
Mounting
30.5 mm through hole; 1x M4 screws; tightening torque
max. 2 Nm; any position
If the fault still exists, perform the steps listed under
“Commissioning Procedure”.
If these steps do not remedy the fault either, return the
device to the manufacturer for examination.
Opening the device is impermissible and will void the
warranty.
Device does not switch on:
Check the wiring by comparing it to the wiring diagrams.
Check the safety switch for correct adjustment.
Check if the green LED is lit when the switch is closed.
Check the operating voltage.
What to Do in
Case of a Fault?
Safety
Characteristics
According to
EN ISO 13849-1
EN ISO 62061
The device is certified according to DIN EN ISO 13849-1
up to a Performance Level of PL e .
The specified PL (for applications according to Fig. 5 to Fig.
11) values were determined under the following worst-case
conditions for a guard door monitoring.
Safety Characteristics according to DIN EN ISO 13849-1 / EN 62061
Performance Level (PL)
e (Depending on the application. See Fig. 5 to Fig. 11)
MTTF
d
866 years
Safety Integrity Level (SIL) SILCL 3
PFHd (1/h)
2.6 x 10
-10
Proof Test Interval
20 years
Maintenance
Check each switch function by opening and closing each
guard individually in turn and ensure that the green LED on
the switch and the appropriate LED’s on the Safety Relay or
Control Device are illuminated when the switch is closed
and are extinguished when the switch is open. Check that
the machine stops and cannot be re-started when each
switch is open.
Never repair any switch, actuator or integral cables.
Replace any switch displaying signs of mechanical damage
to casing or cables.
The device is otherwise maintenance free, provided that it
was installed properly.
Monthly:
Check alignment of actuator and look for
signs of mechanical damage to the switch casing.
For applications were infrequent guard access is foresee-
able, the system must have a manual function test to detect
a possible accumulation of faults. At least once per month
for PL e Cat. 3/4 or once per year for PL d Cat. 3 (ISO
13849-1). Where possible it is recommended that the
control system of the machine demands and monitors
these tests, and stops or prevents the machine from
starting if the test is not done (ISO 14119).